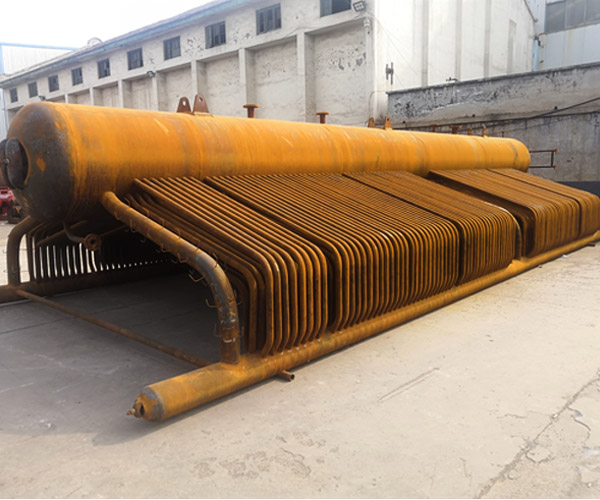
Biomass boilers can be roughly divided into two categories according to their uses: one is biomass thermal energy boiler, and the other is biomass electric energy boiler. Gansu Steam generator In fact, the principle of the two is basically the same. Both obtain energy by burning biomass fuel, which is just one way to directly obtain heat energy. The second way is to convert heat energy into electric energy. Among the two boilers, one is widely used and has mature technology. If we continue to subdivide, one kind of boiler - biomass heat energy boiler mainly has the following two types: one is small biomass heat energy boiler. vertical Steam generator manufactor The boiler uses solidified or gasified biomass fuel to provide heat energy in the form of hot water. Its advantages are small size, simple structure and low price; Class II: medium-sized biomass heat energy boiler. Such boilers mainly use solidified biomass fuel to provide hot water or steam. Its advantages are relatively mature technology, small energy loss and strong heat supply capacity.
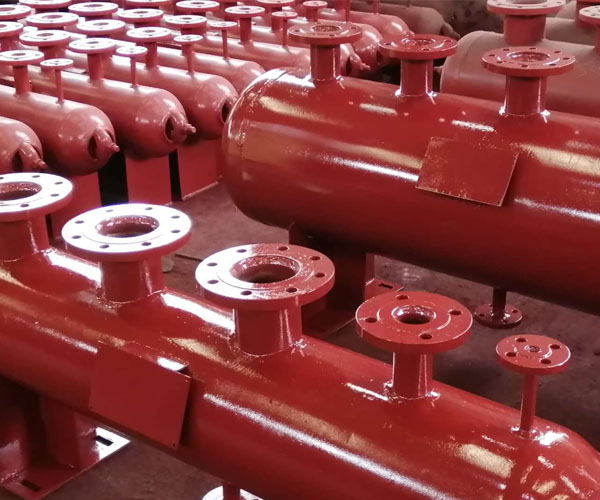
In the chemical industry, the electric heating heat conduction oil furnace is used for distillation, evaporation, polymerization, condensation, steel gate, fatliquoring, monotony, melting, dehydrogenation, forced heat preservation, and the heating of equipment composed of pesticides, intermediates, antioxidants, surfactants, spices, etc. Gansu Steam generator In the plastic and rubber industries, the electric heating heat conduction oil furnace should be used for heating and insulation of hot pressing, hot rolling, kneading, kneading, internal mixing, vulcanization molding, jet injection molding machine, slurry mixer, conveyor belt dryer, screw kneading machine and mold. In metallurgy, machining and casting industries, electric heating heat conduction oil furnaces are used to heat metal degreasing tanks, dewar tanks, electric gate valves, cleaning tanks, electroplating tanks, aluminum plate oxidation tanks, electrode manufacturing, shower heat treatment equipment, phosphate treatment equipment, baking machine rooms, sand core drying, varnish spraying and monotonous equipment. vertical Steam generator manufactor In the food industry, the electric heating heat conduction oil furnace should be used for bread baking equipment, biscuit food baking equipment, candy production equipment, grain monotone equipment, cooking oil pressing and refining equipment, distillation pot, autoclave, conveyor belt dryer electric heater equipment.
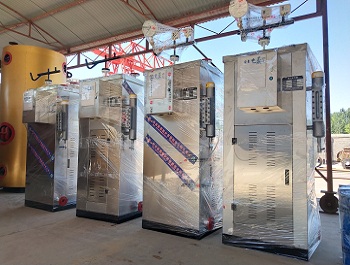
The produced waste heat boiler for hazardous waste incineration is a natural circulation water tube boiler, which adopts a single drum vertical layout and a full membrane water wall structure. Gansu Steam generator The surrounding, top and three middle membrane water-cooled walls form a tight series of heat exchange flues. The convection heating surface is no longer arranged inside the heat exchange flue, and radiation heat exchange is adopted, so as to ensure the smooth flow of high-temperature flue gas containing strong coking adhesive ash in the heat exchange flue. Full automatic shock soot blower is arranged on the membrane water wall, and inspection holes and observation holes are reserved. vertical Steam generator manufactor The bottom of the boiler is composed of membrane water walls on both sides to form a water-cooled ash bucket, and the lower part is connected with a closed spiral ash extractor. The settled soot in the waste heat boiler and the ash removed by the soot blower are discharged out of the boiler by the ash extractor. The furnace wall is of pipe laying structure, and the outside is covered with corrugated steel plate.
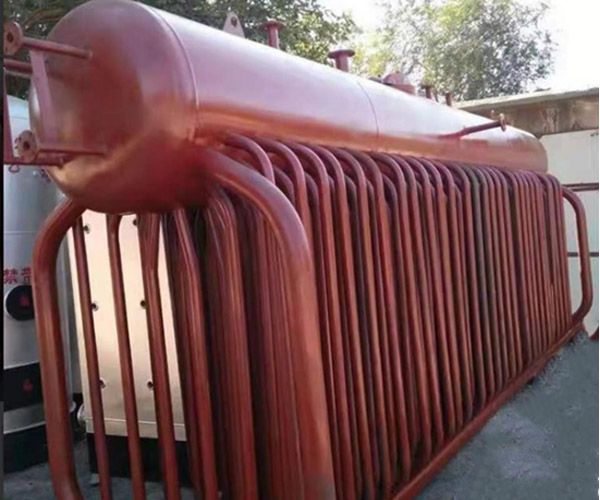
Energy saving. The waste heat boiler adopts new heat exchange fins and heat exchange elements, which enables full heat exchange. The boiler efficiency can be increased by 6~15%, and the condensate drainage structure can fully recover the latent heat in the flue gas. The energy-saving effect is remarkable. Gansu Steam generator Due to the special structure, the total pressure drop is small and the power consumption is small, that is, the smoke pressure drop is small and meets the system requirements. beautiful. Due to the use of efficient heat exchange elements and reasonable structural configuration, the waste heat boiler has the characteristics of compact structure, small size, beautiful appearance, etc. Durable. Heat exchange tubes of waste heat boiler facilities are made of stainless steel aluminum fins for corrosion prevention. vertical Steam generator manufactor The thermal stress, anti-corrosion performance and strength are fully considered when the equipment is manufactured, which can ensure the safety, reliability and stability of the equipment, with a service life of more than 25 years.
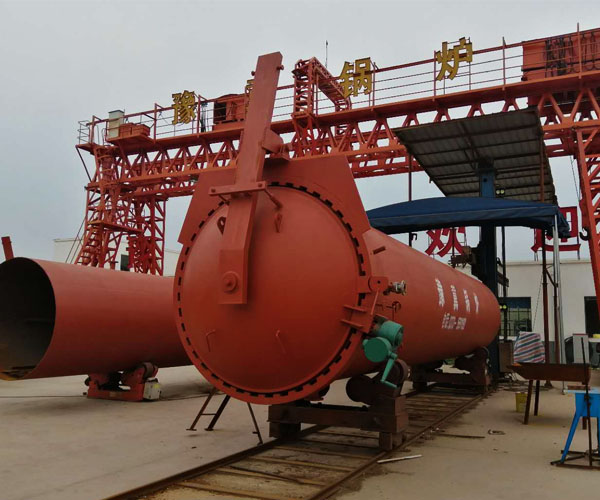
When the boiler is shut down, the temperature of the heat transfer oil can be reduced to below 70 ℃ before the shutdown of the hot oil pump. In case of sudden power failure, extinguish the fire immediately, and then implement the operating procedures. Otherwise, the furnace tube will be burned out and the loss will be large. According to the type of heat transfer oil boiler, heat transfer oil shall be reasonably selected to prevent overheating. Gansu Steam generator When purchasing unqualified heat transfer oil, do not save money or mix heat transfer oil indiscriminately. Otherwise, the consequences will be very serious. Prevent the oxidation of heat transfer oil. The strict heat transfer oil is more than 50 degrees in contact with the air, which will make the heat transfer oil crack. Its speed is amazing, and the consequences are relatively serious. After normal operation, the test crew needs to close the exhaust valve on the auxiliary exhaust pipe. After 6 months of use, the heat transfer oil must be sampled and tested according to the instructions. If problems are found, the heat transfer oil must be replaced immediately. vertical Steam generator manufactor However, it should be noted that different types of heat transfer oil should not be mixed. The circulation speed of the heat transfer oil should not be less than 1.5m/s. Due to the excessive temperature difference between some entrances and exits, the original design requirements were destroyed, the heat transfer oil could not maintain the original circulation state, the boundary layer became thicker, and the thermal resistance became larger, making the furnace wall exceed the oil film temperature, leading to carbon deposition, cracking, polymerization, coking, and even burning through the furnace tube.