As a large equipment, the maintenance of gas-fired hot blast stove is one of the things that must be done. Jinan Energy saving steam generator Regular maintenance can not only keep the hot blast stove clean, but also improve the service life of the hot blast stove. Therefore, it is the top priority in the use of hot blast stove. Today's editor will tell you how to maintain the hot blast stove regularly. In many manufacturers that use hot blast stoves, in order to better develop the enterprise, it is necessary to increase the number of hot blast stoves and improve the performance of hot blast stoves. small-scale Energy saving steam generator factory When enterprises purchase hot blast stove equipment, they must understand their own needs and the products of hot blast stove manufacturers in the market. Therefore, the small edition of gas-fired hot blast stove tells us the problems to be considered in the selection of hot blast stove.
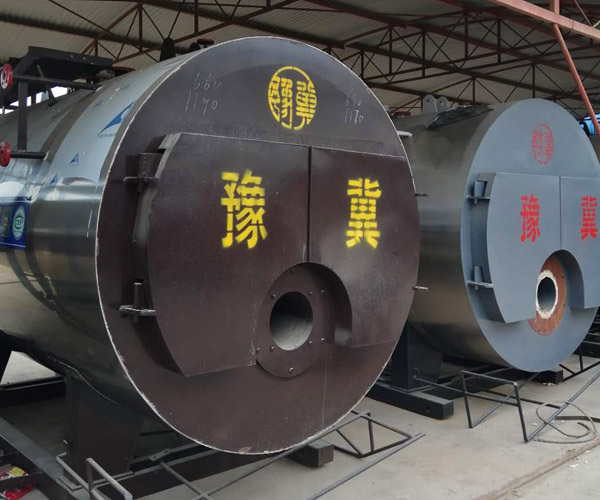
The fluctuation of waste heat boiler flue gas in flow, temperature, composition, dust content and other aspects is one of its characteristics. The nature of the fluctuation can be regular, periodic, or irregular, aperiodic; The characteristics of fluctuation can be gradual. Jinan Energy saving steam generator It can also be impulsive; It can be a single parameter or a composite fluctuation of multiple parameters. The selection of waste heat boiler shall first analyze the whole cycle of the main process flow, and determine the flue gas characteristics of each time section in the cycle. small-scale Energy saving steam generator factory Therefore, corresponding measures shall be implemented one by one in the design of waste heat boiler. The prominent feature is often the main basis for the selection of waste heat boiler.
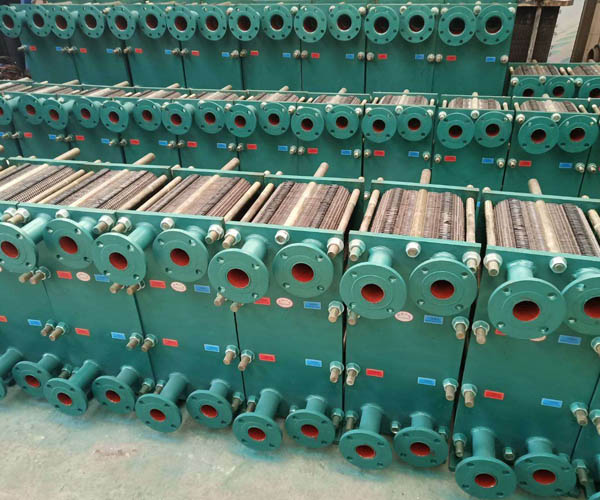
Energy saving. The waste heat boiler adopts new heat exchange fins and heat exchange elements, which enables full heat exchange. The boiler efficiency can be increased by 6~15%, and the condensate drainage structure can fully recover the latent heat in the flue gas. The energy-saving effect is remarkable. Jinan Energy saving steam generator Due to the special structure, the total pressure drop is small and the power consumption is small, that is, the smoke pressure drop is small and meets the system requirements. beautiful. Due to the use of efficient heat exchange elements and reasonable structural configuration, the waste heat boiler has the characteristics of compact structure, small size, beautiful appearance, etc. Durable. Heat exchange tubes of waste heat boiler facilities are made of stainless steel aluminum fins for corrosion prevention. small-scale Energy saving steam generator factory The thermal stress, anti-corrosion performance and strength are fully considered when the equipment is manufactured, which can ensure the safety, reliability and stability of the equipment, with a service life of more than 25 years.
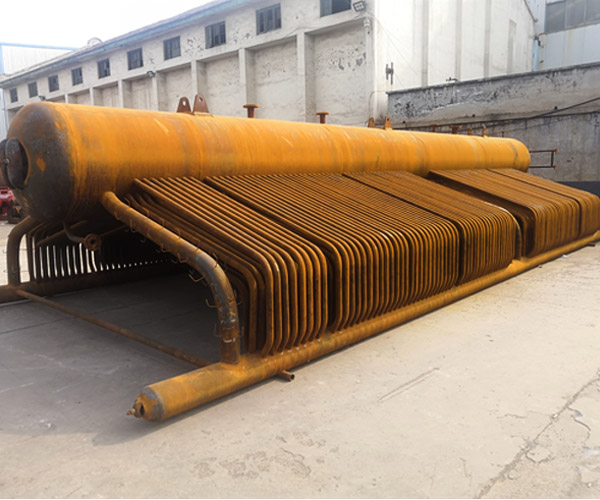
High heat exchange efficiency. The fusion rate at the contact is more than 95%, the contact thermal resistance is small, and the thermal conductivity is good. Low flow resistance. Jinan Energy saving steam generator Since H-shaped finned tubes are similar to square structures, after being assembled into heat exchangers, the tubes are divided into many small channels by fins, which has a certain uniform effect on the air flow. The air flow is similar to longitudinal downstream flow, and the air flow resistance is relatively small. However, spiral finned tubes have strong air flow disturbance, high turbulence, and large air flow resistance due to the directivity of the fins. Less ash. The flue gas contains fly ash, which is easy to deposit on the windward side and leeward side of the pipe bundle. The H-shaped fin tube bundle has the characteristics of flow equalization and downstream flow, which is not easy to cause serious local ash deposition, and the fly ash can be taken away with the air flow in time. Therefore, compared with spiral finned tube heat exchanger, H-type finned tube heat exchanger has less ash deposition. small-scale Energy saving steam generator factory Small size and low weight. H-shaped finned tube has high area expansion rate, less ash deposition, and high heat transfer efficiency. When the heat transfer capacity is equal, the space occupied by the heat exchanger can be small. For reconstruction projects, the heat exchange area can be arranged as much as possible in the limited space to reduce the exhaust gas temperature, improve the waste heat recovery efficiency, or increase the maintenance space to facilitate maintenance.
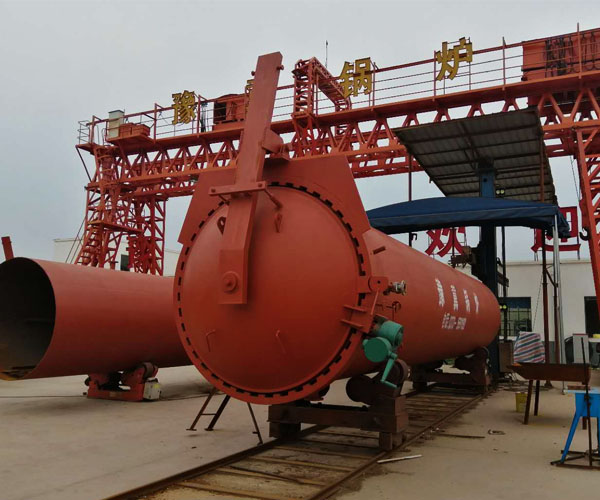
System oil drainage: circulate the heat transfer oil between 120 ± 5 to drain the heat transfer oil in the system (if you do not replace the oil, please find a clean container to store it properly). Prepare an appropriate amount of coke removal cleaning agent for the heat transfer oil system, drain the oil in the gas-fired heat transfer oil boiler system, and disconnect the cleaning system from the oil storage tank (close the valve), including the connection between the high-level tank and the oil storage tank. Jinan Energy saving steam generator Residual oil blowing steps: connect the air compressor at the pressure gauge or other places that can be connected, boost the system to 0.3-0.4MPa, and discharge it instantaneously; Repeat this process until the residual oil is blown out. The gas-fired heat transfer oil boiler, circulating pump, and other heat users form a cleaning circulating circuit for decoking and cleaning: add diluted cleaning agent to the system and fill it up to 1/2 of the water level of the high-level tank. Dosage of coke removal cleaning agent: 10~20%, the specific dosage shall be determined according to the scale thickness. Temperature: 90-95, time: 12-72 hours, which can be determined according to the scale thickness. Rinsing and cleaning: after cleaning, drain the residual liquid in the system and add clean water to rinse twice until the coke remover is free of foam and the water is clear. small-scale Energy saving steam generator factory Temperature: 85-95, time: 5-8 hours Water blowing steps: after cleaning, connect the air compressor at the pressure gauge or other places that can be connected, use compressed air to boost the system to 0.3-0.4 MPa, and vent at each low point. Repeat this process until the water is blown out. Waste liquid treatment: the cleaning waste liquid generated in the cleaning process is discharged after being treated in the biochemical tank.
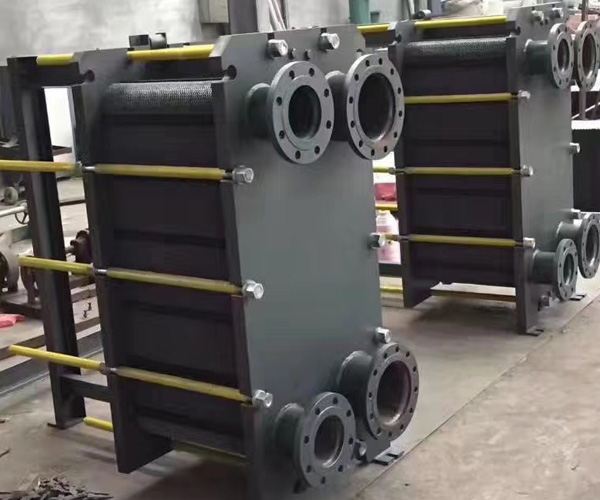
The furnace liner is the combustion chamber of the horizontal gas-fired heat transfer oil furnace. The burner nozzle is placed in the front of the furnace liner, and the high-temperature flue gas generated by combustion extends to the rear, leaving the furnace liner and returning to the space. Generally, the number of times of returning is not more than four, and the common one is the three return heat conduction oil furnace. Jinan Energy saving steam generator This type of heat transfer oil furnace can be divided into dry back type heat transfer oil furnace and full wet back type heat transfer oil furnace according to the structure of the flue gas reentry space at the rear of the furnace. The flue gas reentry space of the dry back heat conduction oil furnace is enclosed by refractory materials; The flue gas reentry space of the full wet back type heat conduction oil furnace is composed of a recuperative chamber immersed in water. In addition, there is a central regenerative heat conduction oil furnace: that is, the back wall of the furnace liner is sealed inside the boiler shell, and the flue gas is turned back to the front from the inner wall around the furnace liner after encountering. This type of heat transfer oil furnace can also be regarded as a full wet back heat transfer oil furnace. small-scale Energy saving steam generator factory Although the dry back heat transfer oil furnace is simple in structure, the refractory material at the rear of the furnace liner is easily damaged, and the rear tube plate is often directly washed by high temperature flue gas. The temperature difference is large, so the dry back heat transfer oil furnace is obsolete. At present, few manufacturers produce it; Although the full wet back heat conduction oil furnace has a complex structure, it avoids the problem of flue gas sealing in the reentry space and is suitable for micro positive pressure combustion.