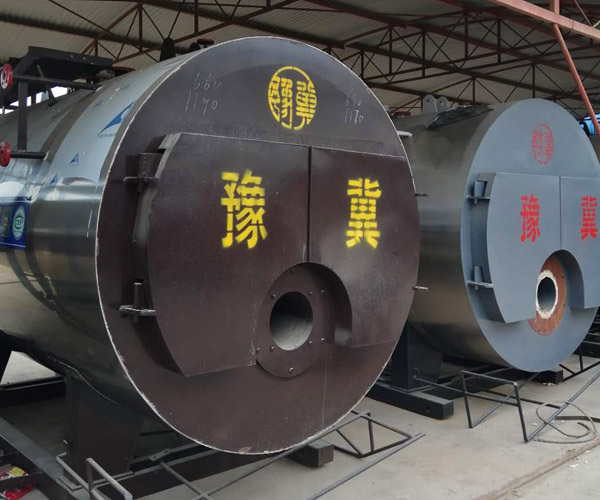
The waste heat boiler greatly improves the utilization rate of heat released by fuel combustion, so this kind of boiler saves energy; Fuel oil, gas and coal combustion generate high-temperature flue gas to release heat. The high-temperature flue gas first enters the furnace, then enters the waste heat recovery device of the front smoke box, then enters the pyrotechnic tube, and then enters the waste heat recovery device in the flue of the rear smoke box. The high-temperature flue gas turns into low-temperature flue gas and is discharged into the atmosphere through the chimney. Kunming Oil fired gas steam generator Conditions conducive to quick startup of waste heat boiler: (1) The waste heat boiler adopts forced circulation, which has the priority of quick startup. (2) The flue gas baffle is hydraulically controlled, which can be used to adjust the sky in principle. The flue gas flow into the boiler is reduced. (3) The adjustable guide vane at the inlet of gas turbine can not only adjust the flue gas flow of gas turbine, but also increase or decrease the exhaust gas temperature of gas turbine through the selection of IGV temperature control mode. (4) The steam turbine bypass is designed for the rated evaporation capacity of the boiler. (5) The welded bends and headers of each heating module of the boiler are in the boiler. (6) Similar boilers in other gas turbine power plants can not be reduced when starting, and can be used to adjust the main steam pressure of the boiler. Outside the wall, contact with high-temperature smoke is avoided. small-scale Oil fired gas steam generator factory Operating experience of gas turbine load, such as simultaneous startup of gas turbine and waste heat boiler (flue gas damper fully open). Under the possibility of quick startup of waste heat boiler, the water level of steam drum and deaerator will lose control after the flue gas baffle is opened.
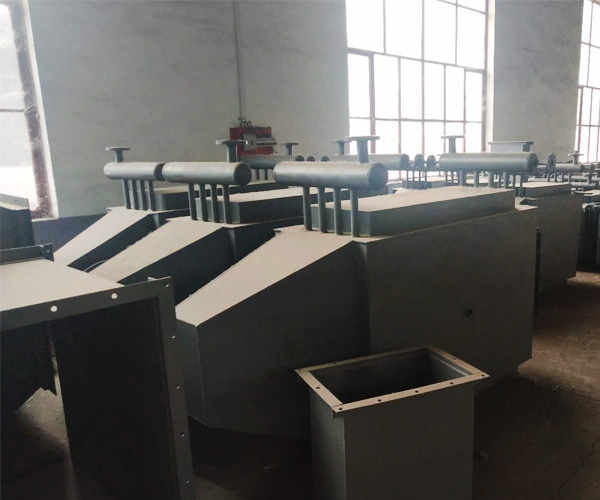
The existing industrial boiler flue gas waste heat recovery equipment mainly includes tubular heat exchanger and full heat pipe heat exchanger. Tube and tube heat exchanger can be composed of finned tube bundles. The advantage of finned tube is that it can withstand higher temperature, but has low heat transfer coefficient and large floor area. Kunming Oil fired gas steam generator The flue gas of industrial boilers contains sulfur and other acidic substances. In the low temperature zone (flue gas outlet section), the temperature may be lower than the dew point of the acidic substances. The acidic substances will dew on the pipe wall, corrode the shell of the fin tube. The fin tube heat exchanger has poor operating reliability and low service life. small-scale Oil fired gas steam generator factory The total heat pipe heat exchanger of boiler flue gas waste heat recovery equipment is composed of heat pipe bundles. Its shell is made of multi-layer composite materials. The heat pipe structure is complex, the cost is relatively expensive, the service life is short, and the steel consumption is large. It is difficult for users to accept it, and it is difficult to promote its application in production. The composite heat pipe heater not only takes into account the heat exchange effect, but also takes into account the economic affordability of the investors in production, which is particularly suitable for the current situation in China's industrial production.
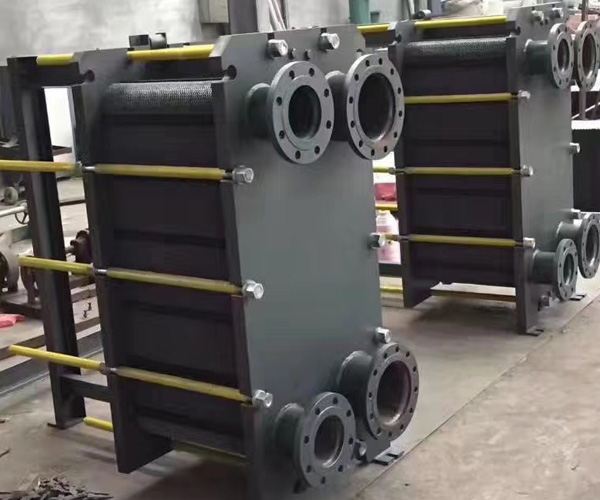
As is known to all, the boiler using sensible heat of various waste gases and waste heat after waste incineration as heat source is called waste heat boiler, also called waste heat boiler. Therefore, the country advocates vigorously developing waste heat utilization, energy conservation and emission reduction, which plays a positive role in protecting energy and improving the quality of human living environment. Kunming Oil fired gas steam generator In the design of waste heat boiler, how to reasonably divide the temperature range is the basis for reasonably arranging the heating surface of waste heat boiler and making maximum use of waste heat. Under the condition of a given exhaust gas temperature at the inlet of the waste heat boiler, there are two requirements for the exhaust gas temperature. One is to limit the exhaust gas temperature, which is required to be within a reasonable range; The other is that the exhaust gas temperature is not limited, requiring greater use of waste heat. small-scale Oil fired gas steam generator factory In either case, for medium and low temperature waste heat utilization, the narrow point temperature difference directly affects the evaporation capacity of the waste heat boiler and the layout of the heating surface. Narrow point temperature difference, also known as node temperature difference, is a small temperature difference between evaporator outlet flue gas and heated saturated water vapor during heat exchange. With the change of narrow point temperature difference, the relative total heat exchange area, relative evaporation capacity and relative exhaust gas temperature of the waste heat boiler also change.
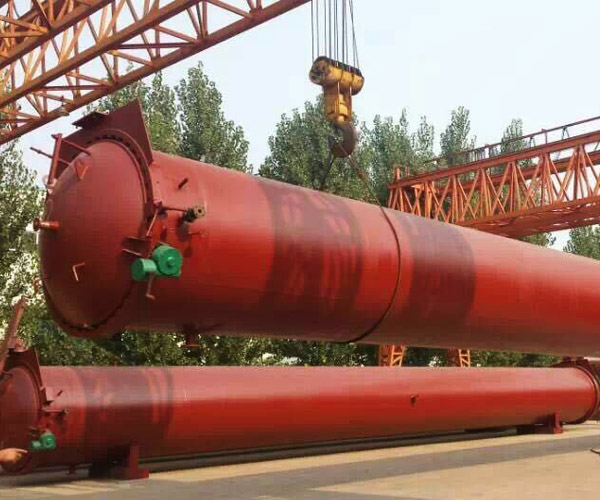
The starting of gas-fired boiler shall be carried out according to the operating procedures. The following is the accurate starting process of the analyzed gas-fired boiler: turn on the main power supply, start the gas-fired incinerator, and close the vent valve on the drum when it emits steam. Kunming Oil fired gas steam generator Check the manhole, handhole flange and valve of the gas boiler. If any leakage is found, fasten them. If leakage occurs after fastening, shut down the boiler for maintenance. When the gas pressure of the gas boiler rises by 0.05~0.1MPA, make up water, blow down, check the experimental water supply system and blow down equipment, and flush the water level gauge together. When the gas boiler pressure rises to 0.1~0.15MPA, flush the pressure gauge trap; When the gas pressure of the gas-fired boiler rises to 0.3MPA, turn the "load high fire/low fire" knob to "high fire" to strengthen incineration. When the pressure of the boiler rises to 2/3 of the operating pressure, start pipe warming and air supply, slowly open the main steam valve to prevent water hammer. small-scale Oil fired gas steam generator factory When the drain valve emits steam, close it. After all the drain valves are closed, slowly open the main gas valve to fully open, and then reverse it for half a circle. Turn the "Control of gas incinerator" knob to the automatic gear.
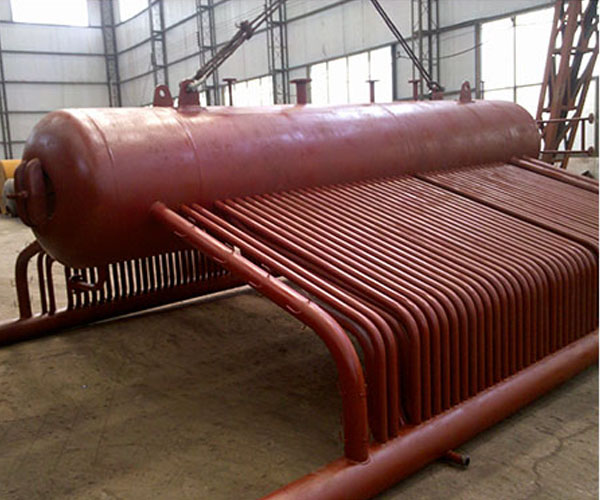
The furnace liner is the combustion chamber of the horizontal gas-fired heat transfer oil furnace. The burner nozzle is placed in the front of the furnace liner, and the high-temperature flue gas generated by combustion extends to the rear, leaving the furnace liner and returning to the space. Generally, the number of times of returning is not more than four, and the common one is the three return heat conduction oil furnace. Kunming Oil fired gas steam generator This type of heat transfer oil furnace can be divided into dry back type heat transfer oil furnace and full wet back type heat transfer oil furnace according to the structure of the flue gas reentry space at the rear of the furnace. The flue gas reentry space of the dry back heat conduction oil furnace is enclosed by refractory materials; The flue gas reentry space of the full wet back type heat conduction oil furnace is composed of a recuperative chamber immersed in water. In addition, there is a central regenerative heat conduction oil furnace: that is, the back wall of the furnace liner is sealed inside the boiler shell, and the flue gas is turned back to the front from the inner wall around the furnace liner after encountering. This type of heat transfer oil furnace can also be regarded as a full wet back heat transfer oil furnace. small-scale Oil fired gas steam generator factory Although the dry back heat transfer oil furnace is simple in structure, the refractory material at the rear of the furnace liner is easily damaged, and the rear tube plate is often directly washed by high temperature flue gas. The temperature difference is large, so the dry back heat transfer oil furnace is obsolete. At present, few manufacturers produce it; Although the full wet back heat conduction oil furnace has a complex structure, it avoids the problem of flue gas sealing in the reentry space and is suitable for micro positive pressure combustion.