Stainless steel for pressure vessels and its welding characteristics. The so-called stainless steel refers to the addition of a certain amount of chromium in the steel to keep the steel in a passive state and free from rust. Shenzhen Miniature steam generator For this purpose, the chromium content must be more than 12%. In order to improve the passivity of steel, it is often necessary to add nickel, molybdenum and other elements that can passivate steel into stainless steel. Stainless steel is generally referred to as stainless steel and acid resistant steel. Stainless steel companies do not have certain acid resistance, and acid resistant steel generally has a good stainless property. vertical Miniature steam generator factory According to its steel structure, stainless steel can be divided into four categories, namely, austenitic stainless steel, ferritic stainless steel, martensitic stainless steel, and austenitic ferritic duplex stainless steel.
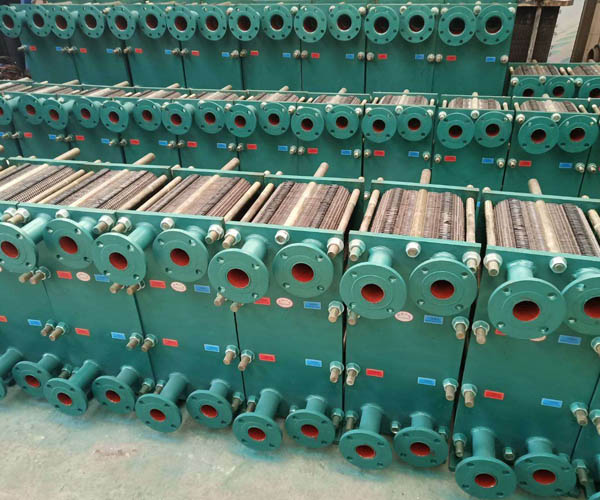
The waste heat boiler for hazardous waste incineration is an important part of the hazardous waste rotary kiln incineration system. The heat source is the high-temperature waste gas containing strongly coking and cohesive ash after hazardous waste incineration. Shenzhen Miniature steam generator Generally, this type of waste heat boiler adopts single flue or multi flue layout, and convection heating surface is arranged in the flue. During operation, strongly coking cohesive ash is easy to adhere to the convection heating surface, leading to flue blockage, affecting the safe and normal operation of the waste heat boiler. According to the characteristics of hazardous waste rotary kiln incineration system, a kind of waste heat boiler with special structure suitable for the system was developed, which successfully solved the problems of ash deposition, wear, air leakage, corrosion, etc. vertical Miniature steam generator factory The water circulation mode of the waste heat boiler is natural circulation. The working medium directly enters the drum, then is led out from the drum, flows into each membrane water wall through the downcomer, is heated here, then led back to the drum through the steam conduit, and is separated by the steam water separator, and then led out of the drum saturated steam with rated parameters.
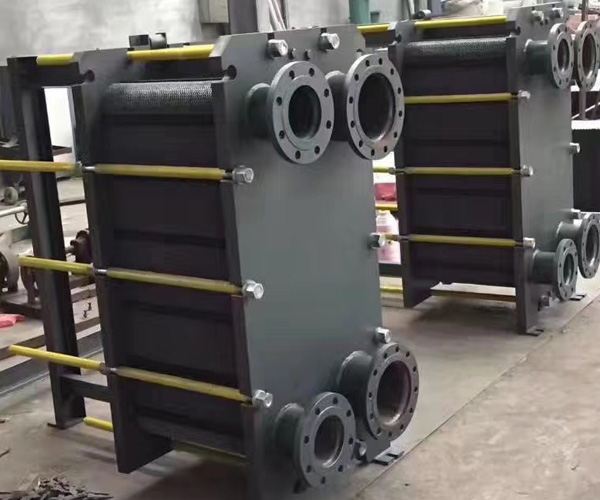
The furnace liner is the combustion chamber of the horizontal gas-fired heat transfer oil furnace. The burner nozzle is placed in the front of the furnace liner, and the high-temperature flue gas generated by combustion extends to the rear, leaving the furnace liner and returning to the space. Generally, the number of times of returning is not more than four, and the common one is the three return heat conduction oil furnace. Shenzhen Miniature steam generator This type of heat transfer oil furnace can be divided into dry back type heat transfer oil furnace and full wet back type heat transfer oil furnace according to the structure of the flue gas reentry space at the rear of the furnace. The flue gas reentry space of the dry back heat conduction oil furnace is enclosed by refractory materials; The flue gas reentry space of the full wet back type heat conduction oil furnace is composed of a recuperative chamber immersed in water. In addition, there is a central regenerative heat conduction oil furnace: that is, the back wall of the furnace liner is sealed inside the boiler shell, and the flue gas is turned back to the front from the inner wall around the furnace liner after encountering. This type of heat transfer oil furnace can also be regarded as a full wet back heat transfer oil furnace. vertical Miniature steam generator factory Although the dry back heat transfer oil furnace is simple in structure, the refractory material at the rear of the furnace liner is easily damaged, and the rear tube plate is often directly washed by high temperature flue gas. The temperature difference is large, so the dry back heat transfer oil furnace is obsolete. At present, few manufacturers produce it; Although the full wet back heat conduction oil furnace has a complex structure, it avoids the problem of flue gas sealing in the reentry space and is suitable for micro positive pressure combustion.
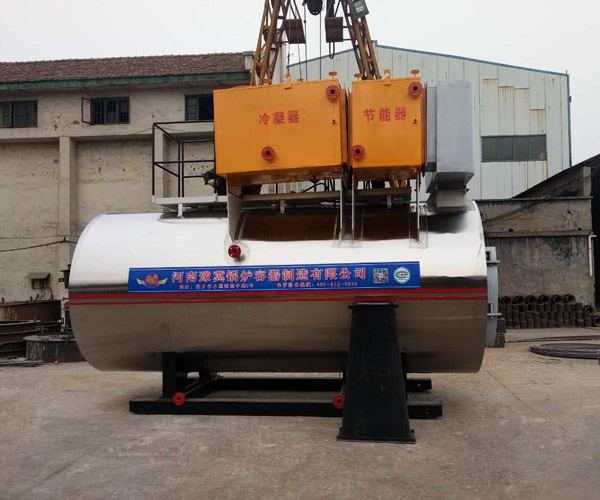
The main parts of the waste heat boiler can be divided into drum, pipe, header, membrane wall, tube panel, tube box, etc. These parts are the parts with specific process requirements in the waste heat boiler. Shenzhen Miniature steam generator For example, the drum should go through metal flaw detection, heat treatment, hydrostatic test and other processes to improve the stability of the waste heat boiler. At the same time, because the header needs high sealing, manual welding is required, and the welding quality needs to be tested. It can be seen that due to the complexity of the working environment of the waste heat boiler, it has special requirements for its internal structural members. vertical Miniature steam generator factory In the process of designing and manufacturing the waste heat boiler, the process designer should consider the advantages and disadvantages of various processes, and then select a reasonable process to complete the manufacturing of the waste heat boiler. For example, the serpentine parts in the waste heat boiler cannot be bent automatically by the machine, so they can only be bent manually.