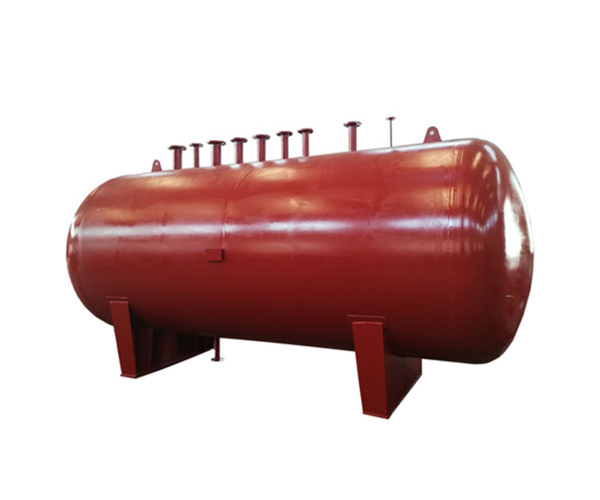
The waste heat boiler for hazardous waste incineration is an important part of the hazardous waste rotary kiln incineration system. The heat source is the high-temperature waste gas containing strongly coking and cohesive ash after hazardous waste incineration. Heilongjiang Gas fired hot blast stove Generally, this type of waste heat boiler adopts single flue or multi flue layout, and convection heating surface is arranged in the flue. During operation, strongly coking cohesive ash is easy to adhere to the convection heating surface, leading to flue blockage, affecting the safe and normal operation of the waste heat boiler. According to the characteristics of hazardous waste rotary kiln incineration system, a kind of waste heat boiler with special structure suitable for the system was developed, which successfully solved the problems of ash deposition, wear, air leakage, corrosion, etc. vertical Gas fired hot blast stove factory The water circulation mode of the waste heat boiler is natural circulation. The working medium directly enters the drum, then is led out from the drum, flows into each membrane water wall through the downcomer, is heated here, then led back to the drum through the steam conduit, and is separated by the steam water separator, and then led out of the drum saturated steam with rated parameters.
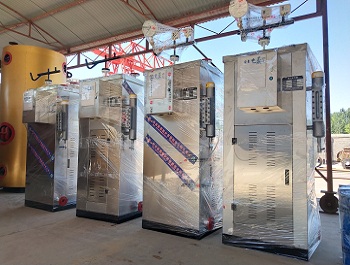
Effectively prevent and reduce low temperature corrosion of air preheater. Low temperature corrosion is caused by sulfur dioxide generated by combustion of sulfur in fuel. Heilongjiang Gas fired hot blast stove Under the action of catalyst, sulfur dioxide is further oxidized to sulfur trioxide. Sulfur trioxide and water vapor in the flue gas generate sulfuric acid vapor, which greatly increases the dew point of the flue gas, condenses the sulfuric acid vapor on the flue gas side of the preheater tube wall, causing sulfuric acid corrosion of the preheater. The content of sulfur trioxide has a great impact on the corrosion rate of the preheater. The content of sulfur trioxide is not only related to the sulfur content in the fuel, but also related to the oxygen content in the flue gas. vertical Gas fired hot blast stove factory Low oxygen combustion can significantly reduce the oxygen content in flue gas, greatly reduce the amount of sulfur dioxide oxidized to sulfur trioxide, reduce the dew point of flue gas, and effectively reduce the corrosion of preheater. Low oxygen combustion reduces the amount of flue gas. It can not only reduce the exhaust gas temperature, improve the boiler efficiency, but also reduce the power consumption of the forced draft fan and the wear of the heating surface.
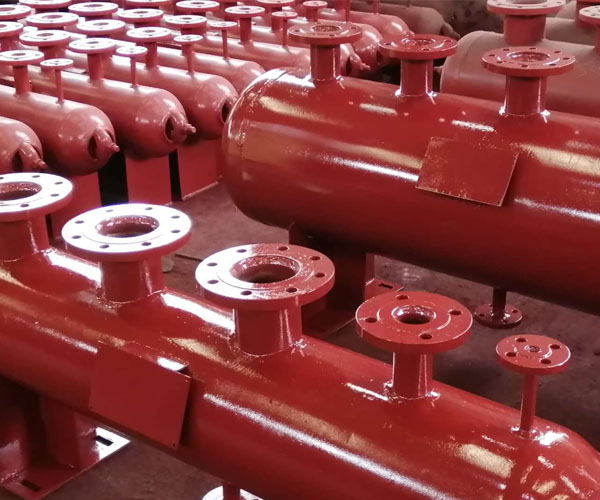
High heat exchange efficiency. The fusion rate at the contact is more than 95%, the contact thermal resistance is small, and the thermal conductivity is good. Low flow resistance. Heilongjiang Gas fired hot blast stove Since H-shaped finned tubes are similar to square structures, after being assembled into heat exchangers, the tubes are divided into many small channels by fins, which has a certain uniform effect on the air flow. The air flow is similar to longitudinal downstream flow, and the air flow resistance is relatively small. However, spiral finned tubes have strong air flow disturbance, high turbulence, and large air flow resistance due to the directivity of the fins. Less ash. The flue gas contains fly ash, which is easy to deposit on the windward side and leeward side of the pipe bundle. The H-shaped fin tube bundle has the characteristics of uniform flow and downstream flow, so it is not easy to cause serious local ash deposition, and the fly ash can be taken away with the air flow in time. Therefore, compared with spiral finned tube heat exchanger, H-type finned tube heat exchanger has less ash deposition. vertical Gas fired hot blast stove factory Small size and low weight. H-shaped finned tube has high area expansion rate, less ash deposition, and high heat transfer efficiency. When the heat transfer capacity is equal, the space occupied by the heat exchanger can be small. For reconstruction projects, the heat exchange area can be arranged as much as possible in the limited space to reduce the exhaust gas temperature, improve the waste heat recovery efficiency, or increase the maintenance space to facilitate maintenance.
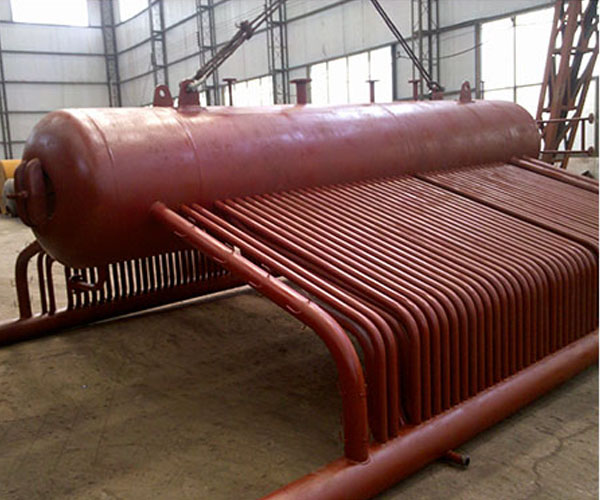
Waste heat boilers are widely used in high energy consumption industries. There are two common types of waste heat boilers: one is used to recover the exhaust gas emitted by ordinary boilers, such as fuel fired and gas-fired boilers, biomass fired boilers, etc. The temperature of the exhaust gas from ordinary boilers is about 600 ℃, which is not too high, Therefore, the requirements for waste heat recovery boiler are relatively low. Heilongjiang Gas fired hot blast stove The other is industrial waste heat recovery boiler, such as building materials industry, chemical industry, steel making industry, etc. The temperature of waste gas and waste heat in these industries is high, and the recovery and utilization are also quite valuable. vertical Gas fired hot blast stove factory Henan Yuji Boiler Vessel Manufacturing Co., Ltd., founded in 2005, is located at No. 8, Jizhong Road, Xiaoji Town, Xinxiang County, Henan Province. It is a comprehensive enterprise of boiler and pressure vessel, mainly engaged in the manufacturing of boilers and pressure vessels, with technological innovation as the core, integrating the design, manufacturing, sales, installation, transformation and maintenance of boilers and pressure vessels.