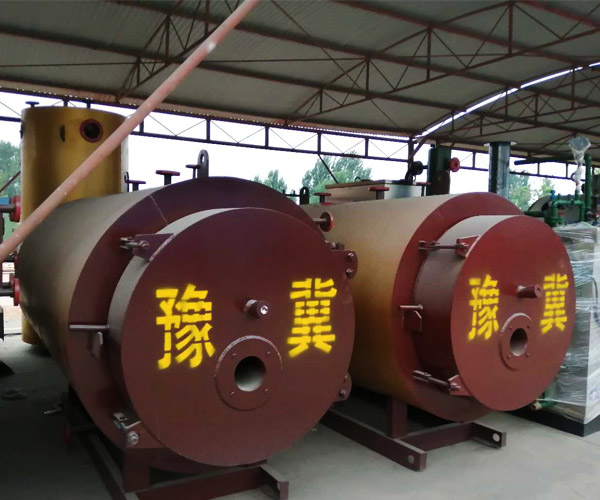
When using stainless steel storage tank, cracks appear on the head. If it is not handled in time, it will be dangerous, and how to handle this situation will be explained. Heilongjiang Waste heat boiler Firstly, the cracks in the stainless steel tank can were removed by polishing. After grinding, pits that do not need repair welding and do not affect the grading shall be formed within the allowable range. Otherwise, repair welding shall be carried out. The position of surface crack defect shall be determined by surface penetration defect detection, and the welding repair shall be completed. The horizontal gas tank shall be repaired, and the weld and surrounding materials shall be repaired. After that, argon tungsten arc welding shall be used for repair welding. small-scale Waste heat boiler factory Tungsten argon arc welding shall be adopted for welding repair. It is suitable for back welding or skip welding, small size multi-layer and multi pass non rotating welding to avoid overheating of the weld. Water cooling measures are adopted. The defects of stainless steel storage tanks shall be removed by grinding with angular grinding wheel with conical grinding rod. Note that the abrasive grains of the grinding wheel should be perpendicular to the crack length. If the defect is deep, crack stop holes shall be drilled at both ends of the defect to prevent the crack from expanding with the grinding process. According to the inspection, in the stainless steel storage tank with primary side inspection, there are cracks at the head welds, and these defective welds have different edge bite degrees. Do not panic when the stainless steel tank can has cracks. The oil tank works. The above measures can be taken to solve this problem.
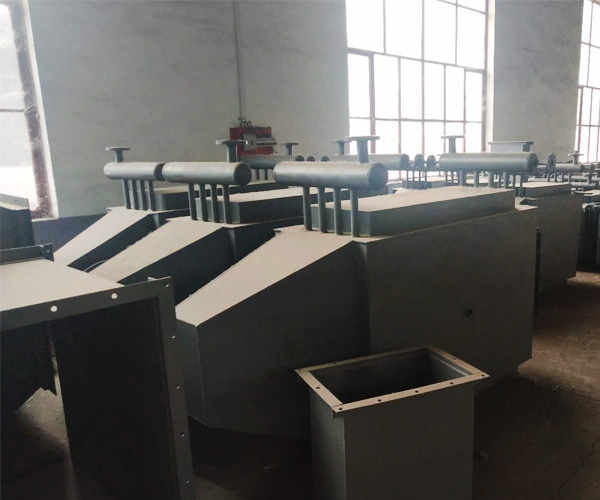
System oil drainage: circulate the heat transfer oil between 120 ± 5 to drain the heat transfer oil in the system (if you do not replace the oil, please find a clean container to store it properly). Prepare an appropriate amount of coke removal cleaning agent for the heat transfer oil system, drain the oil in the gas-fired heat transfer oil boiler system, and disconnect the cleaning system from the oil storage tank (close the valve), including the connection between the high-level tank and the oil storage tank. Heilongjiang Waste heat boiler Residual oil blowing steps: connect the air compressor at the pressure gauge or other places that can be connected, boost the system to 0.3-0.4MPa, and discharge it instantaneously; Repeat this process until the residual oil is blown out. The gas-fired heat transfer oil boiler, circulating pump, and other heat users form a cleaning circulating circuit for decoking and cleaning: add diluted cleaning agent to the system and fill it up to 1/2 of the water level of the high-level tank. Dosage of coke removal cleaning agent: 10~20%, the specific dosage shall be determined according to the scale thickness. Temperature: 90-95, time: 12-72 hours, which can be determined according to the scale thickness. Rinsing and cleaning: after cleaning, drain the residual liquid in the system and add clean water to rinse twice until the coke remover is free of foam and the water is clear. small-scale Waste heat boiler factory Temperature: 85-95, time: 5-8 hours Water blowing steps: after cleaning, connect the air compressor at the pressure gauge or other places that can be connected, use compressed air to boost the system to 0.3-0.4 MPa, and vent at each low point. Repeat this process until the water is blown out. Waste liquid treatment: the cleaning waste liquid generated in the cleaning process is discharged after being treated in the biochemical tank.
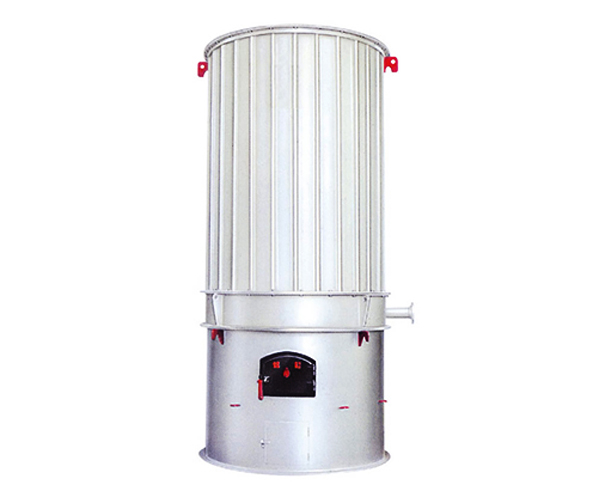
The existing industrial boiler flue gas waste heat recovery equipment mainly includes tubular heat exchanger and full heat pipe heat exchanger. Tube and tube heat exchanger can be composed of finned tube bundles. The advantage of finned tube is that it can withstand higher temperature, but has low heat transfer coefficient and large floor area. Heilongjiang Waste heat boiler The flue gas of industrial boilers contains sulfur and other acidic substances. In the low temperature zone (flue gas outlet section), the temperature may be lower than the dew point of the acidic substances. The acidic substances will dew on the pipe wall, corrode the shell of the fin tube. The fin tube heat exchanger has poor operating reliability and low service life. small-scale Waste heat boiler factory The total heat pipe heat exchanger of boiler flue gas waste heat recovery equipment is composed of heat pipe bundles. Its shell is made of multi-layer composite materials. The heat pipe structure is complex, the cost is relatively expensive, the service life is short, and the steel consumption is large. It is difficult for users to accept it, and it is difficult to promote its application in production. The composite heat pipe heater not only takes into account the heat exchange effect, but also takes into account the economic affordability of the investors in production, which is particularly suitable for the current situation in China's industrial production.
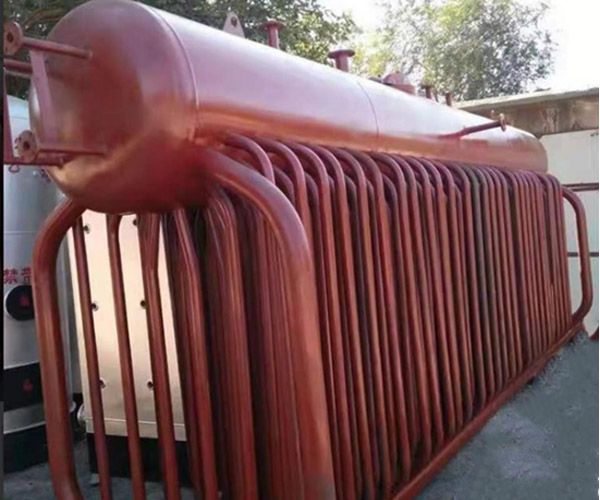
Enterprises that rely on coal for power generation are both traditional power enterprises and highly polluting enterprises. The industrial waste gas discharged by coal power generation enterprises has seriously polluted our living environment. Heilongjiang Waste heat boiler As a result, the country has become more and more strict in the control of this industry, and how to use waste heat recycling power generation has become a topic of concern for many enterprises. Waste heat boiler can meet this demand of enterprises, so its application in coal mine power generation enterprises is more and more. small-scale Waste heat boiler factory Installing a waste heat recovery boiler on the exhaust pipe of the coal mine gas generator set, using the waste heat discharged by the coal mine gas generator set to generate steam for power generation, can not only turn waste into treasure to realize the secondary utilization of energy, achieve the goal of combining coal mine gas control with energy conservation and emission reduction, but also reduce environmental pollution, kill two birds with one stone.
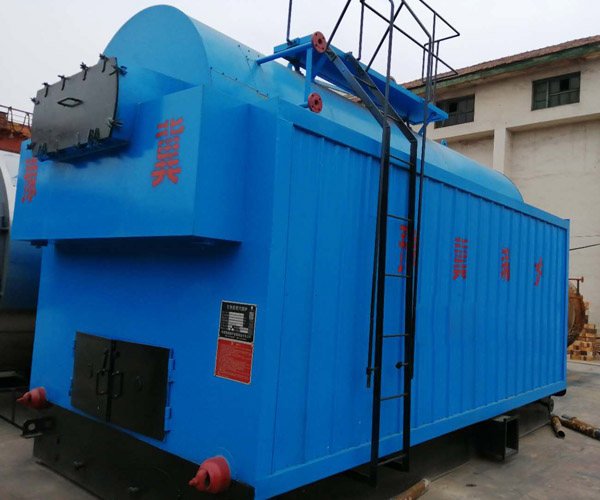
The main parts of the waste heat boiler can be divided into drum, pipe, header, membrane wall, tube panel, tube box, etc. These parts are the parts with specific process requirements in the waste heat boiler. Heilongjiang Waste heat boiler For example, the drum should go through metal flaw detection, heat treatment, hydrostatic test and other processes to improve the stability of the waste heat boiler. At the same time, because the header needs high sealing, manual welding is required, and the welding quality needs to be tested. It can be seen that due to the complexity of the working environment of the waste heat boiler, it has special requirements for its internal structural members. small-scale Waste heat boiler factory In the process of designing and manufacturing the waste heat boiler, the process designer should consider the advantages and disadvantages of various processes, and then select a reasonable process to complete the manufacturing of the waste heat boiler. For example, the serpentine parts in the waste heat boiler cannot be bent automatically by the machine, so they can only be bent manually.
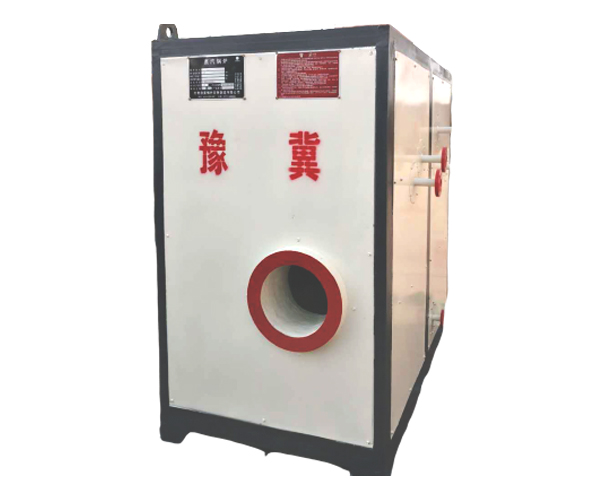
As is known to all, the boiler using sensible heat of various waste gases and waste heat after waste incineration as heat source is called waste heat boiler, also called waste heat boiler. Therefore, the country advocates vigorously developing waste heat utilization, energy conservation and emission reduction, which plays a positive role in protecting energy and improving the quality of human living environment. Heilongjiang Waste heat boiler In the design of waste heat boiler, how to reasonably divide the temperature range is the basis for reasonably arranging the heating surface of waste heat boiler and making maximum use of waste heat. Under the condition of a given exhaust gas temperature at the inlet of the waste heat boiler, there are two requirements for the exhaust gas temperature. One is to limit the exhaust gas temperature, which is required to be within a reasonable range; The other is that the exhaust gas temperature is not limited, requiring greater use of waste heat. small-scale Waste heat boiler factory In either case, for medium and low temperature waste heat utilization, the narrow point temperature difference directly affects the evaporation capacity of the waste heat boiler and the layout of the heating surface. Narrow point temperature difference, also known as node temperature difference, is a small temperature difference between evaporator outlet flue gas and heated saturated water vapor during heat exchange. With the change of narrow point temperature difference, the relative total heat exchange area, relative evaporation capacity and relative exhaust gas temperature of the waste heat boiler also change.