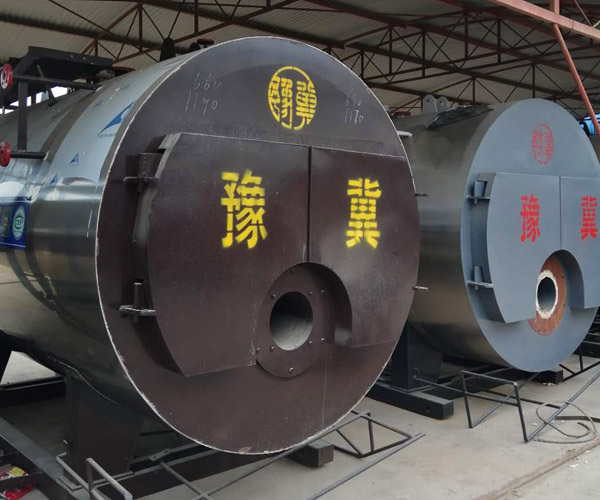
High heat exchange efficiency. The fusion rate at the contact is more than 95%, the contact thermal resistance is small, and the thermal conductivity is good. Low flow resistance. Jilin electric steam generator Since H-shaped finned tubes are similar to square structures, after being assembled into heat exchangers, the tubes are divided into many small channels by fins, which has a certain uniform effect on the air flow. The air flow is similar to longitudinal downstream flow, and the air flow resistance is relatively small. However, spiral finned tubes have strong air flow disturbance, high turbulence, and large air flow resistance due to the directivity of the fins. Less ash. The flue gas contains fly ash, which is easy to deposit on the windward side and leeward side of the pipe bundle. H-shaped finned tube bundle has the characteristics of flow equalization and downstream flow, so it is not easy to cause serious local ash deposition, and the fly ash can be taken away with the air flow in time. Therefore, compared with spiral finned tube heat exchanger, H-type finned tube heat exchanger has less ash deposition. vertical electric steam generator factory Small size and low weight. H-shaped finned tube has high area expansion rate, less ash deposition, and high heat transfer efficiency. When the heat transfer capacity is equal, the space occupied by the heat exchanger can be small. For reconstruction projects, the heat exchange area can be arranged as much as possible in the limited space to reduce the exhaust gas temperature, improve the waste heat recovery efficiency, or increase the maintenance space to facilitate maintenance.
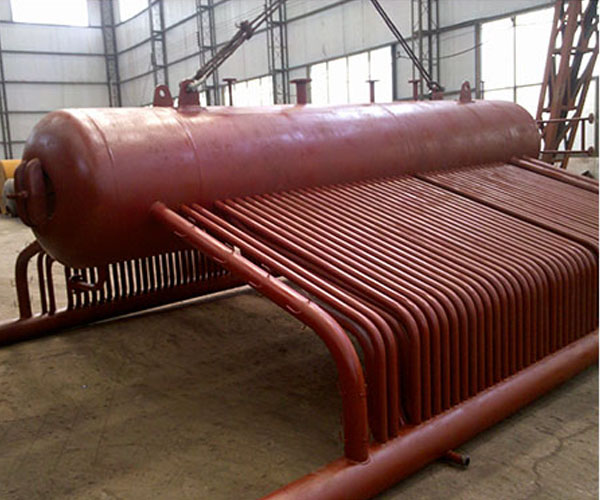
The fluctuation of waste heat boiler flue gas in flow, temperature, composition, dust content and other aspects is one of its characteristics. The nature of the fluctuation can be regular, periodic, or irregular, aperiodic; The characteristics of fluctuation can be gradual. Jilin electric steam generator It can also be impulsive; It can be a single parameter or a composite fluctuation of multiple parameters. The selection of waste heat boiler shall first analyze the whole cycle of the main process flow, and determine the flue gas characteristics of each time section in the cycle. vertical electric steam generator factory Therefore, corresponding measures shall be implemented one by one in the design of waste heat boiler. The prominent feature is often the main basis for the selection of waste heat boiler.
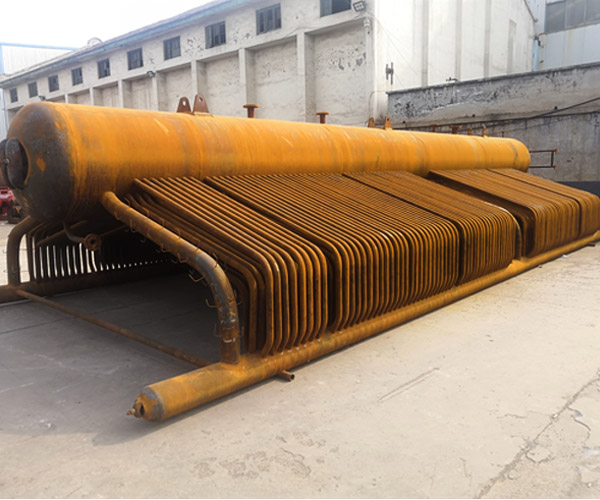
The starting of gas-fired boiler shall be carried out according to the operating procedures. The following is the accurate starting process of the analyzed gas-fired boiler: turn on the main power supply, start the gas-fired incinerator, and close the vent valve on the drum when it emits steam. Jilin electric steam generator Check the manhole, handhole flange and valve of the gas boiler. If any leakage is found, fasten them. If leakage occurs after fastening, shut down the boiler for maintenance. When the gas pressure of the gas boiler rises by 0.05~0.1MPA, make up water, blow down, check the experimental water supply system and blow down equipment, and flush the water level gauge together. When the gas boiler pressure rises to 0.1~0.15MPA, flush the pressure gauge trap; When the gas pressure of the gas-fired boiler rises to 0.3MPA, turn the "load high fire/low fire" knob to "high fire" to strengthen incineration. When the pressure of the boiler rises to 2/3 of the operating pressure, start pipe warming and air supply, slowly open the main steam valve to prevent water hammer. vertical electric steam generator factory When the drain valve emits steam, close it. After all the drain valves are closed, slowly open the main gas valve to fully open, and then reverse it for half a circle. Turn the "Control of gas incinerator" knob to the automatic gear.
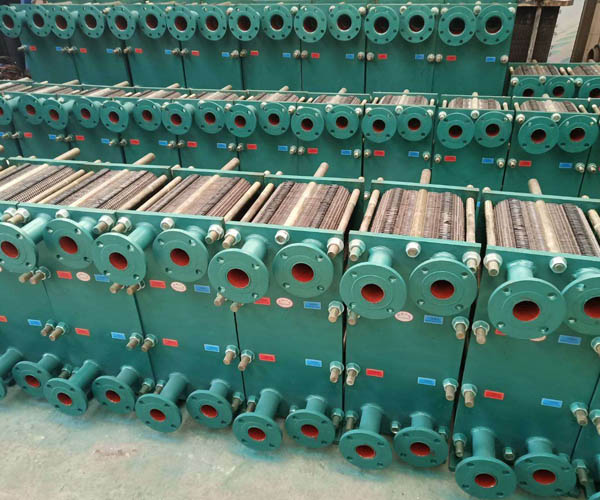
The waste heat recovery of flue gas can not only be used for heating or power generation to achieve energy-saving effect, but also can be beneficial to environmental protection and achieve dual effects of energy conservation and environmental protection. Jilin electric steam generator In general, the important equipment of waste heat power generation is waste heat boiler, which mainly uses heat or combustible substances in waste gas, waste liquid and other working medium as heat source, and produces steam mainly for power generation. There are many ways to recover waste heat from flue gas of waste heat boiler. Generally, comprehensive utilization of waste heat is followed by direct utilization and indirect utilization. vertical electric steam generator factory Generally speaking, if heat sources are needed in the process, the waste heat utilization is mainly comprehensive utilization. First, the heat source is recovered and fed back to the process for reuse. If there is any surplus, it can be used for power generation or as the heat source for central heating; If there is no surplus, it will be directly used instead of being used for power generation; If the process does not need more heat sources, then indirect use, mainly power generation or public heating.
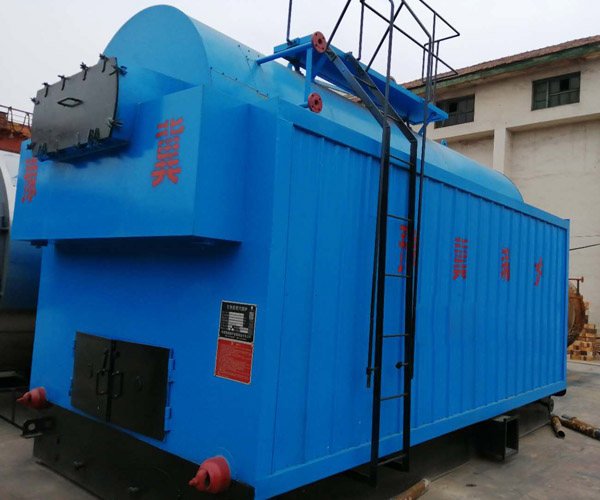
System oil drainage: circulate the heat transfer oil between 120 ± 5 to drain the heat transfer oil in the system (if you do not replace the oil, please find a clean container to store it properly). Prepare an appropriate amount of coke removal cleaning agent for the heat transfer oil system, drain the oil in the gas-fired heat transfer oil boiler system, and disconnect the cleaning system from the oil storage tank (close the valve), including the connection between the high-level tank and the oil storage tank. Jilin electric steam generator Residual oil blowing steps: connect the air compressor at the pressure gauge or other places that can be connected, boost the system to 0.3-0.4MPa, and discharge it instantaneously; Repeat this process until the residual oil is blown out. The gas-fired heat transfer oil boiler, circulating pump, and other heat users form a cleaning circulating circuit for decoking and cleaning: add diluted cleaning agent to the system and fill it up to 1/2 of the water level of the high-level tank. Dosage of coke removal cleaning agent: 10~20%, the specific dosage shall be determined according to the scale thickness. Temperature: 90-95, time: 12-72 hours, which can be determined according to the scale thickness. Rinsing and cleaning: after cleaning, drain the residual liquid in the system and add clean water to rinse twice until the coke remover is free of foam and the water is clear. vertical electric steam generator factory Temperature: 85-95, time: 5-8 hours Water blowing steps: after cleaning, connect the air compressor at the pressure gauge or other places that can be connected, use compressed air to boost the system to 0.3-0.4 MPa, and vent at each low point. Repeat this process until the water is blown out. Waste liquid treatment: the cleaning waste liquid generated in the cleaning process is discharged after being treated in the biochemical tank.
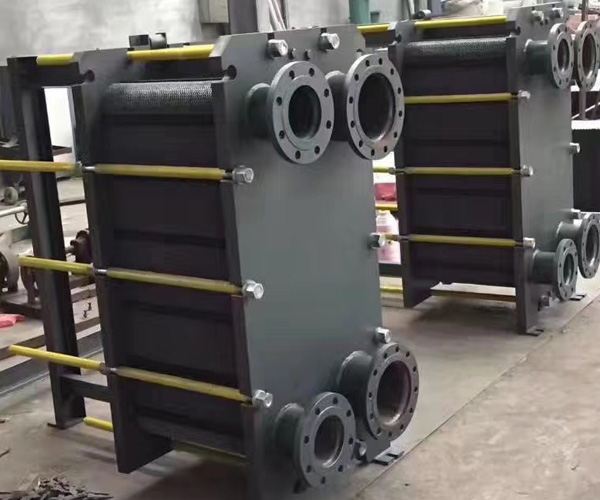
The waste heat boiler has advantages in the subdivided industry and is the leading enterprise in the industry. The company's main products are various types of waste heat boilers, industrial boilers, power station boilers, nuclear power equipment and power station auxiliaries. It is a research, development, design and manufacturing base for waste heat boilers with large scale and complete varieties in China. Jilin electric steam generator Waste heat boiler is a typical energy-saving and emission reduction equipment. Its heat source can come from high-temperature flue gas waste heat, chemical reaction waste heat, combustible waste gas waste heat, and even can use high-temperature product waste heat. At present, the company has more than 20 series and more than 100 varieties of waste heat boiler products, which are widely used in steel, building materials, power, nonferrous metals, coking, chemical and other industries. vertical electric steam generator factory In 2008, the company produced 272 sets of waste heat boilers of various types, with a total of 10268 steam tons, accounting for 34% of the comprehensive market share based on steam tons; According to the output value, the market share is 47%, ranking first in the waste heat boiler industry.