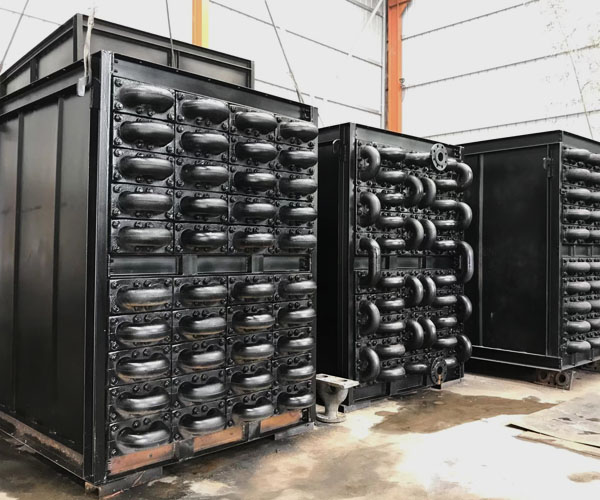
You will find that the characteristics of industrial boiler equipment are obvious. When designing industrial boilers, they should be regularly maintained. Vertical boilers have obvious characteristics Guangdong Full automatic fuel oil steam generator The combustion part adopts a double-layer grate combustion chamber, which has fast temperature rise and pressure rise, reasonable overall layout, good heat transfer, sufficient combustion, smoke suppression and dust removal for unburned gas after secondary combustion, and is one of the smaller steam and heating equipment. small-scale Full automatic fuel oil steam generator factory The characteristics of the whole industrial boiler are obvious, with high thermal efficiency and sufficient steam. The whole industrial boiler is equipped with excellent safety valve, pressure regulator, low water level and other multiple protection devices, which can effectively ensure the safe operation of the boiler. Moreover, industrial boiler equipment is compact in structure, small in floor area, elegant in shape and bright in color. Therefore, it plays an important role in many large factories and coal mining enterprises.
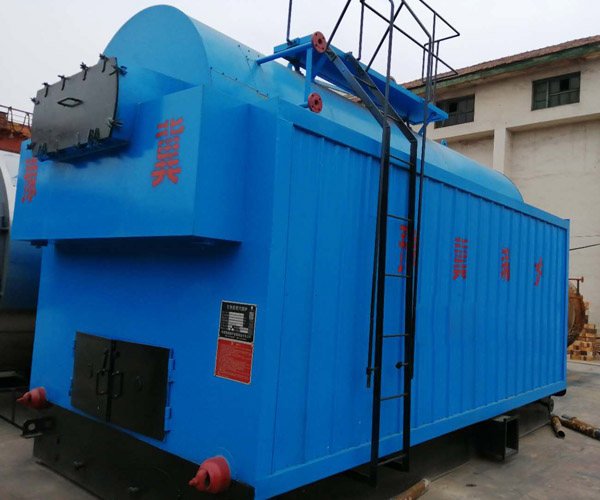
The boiler adopts the combustion equipment suitable for the combustion of biomass fuel - reciprocating grate. In the structural design of the boiler, the furnace space of the boiler is larger than that of the traditional boiler, and the reasonable arrangement of the secondary air is conducive to the full combustion of a large amount of volatile matter released instantaneously during the combustion of biomass fuel. The boiler can be equipped with oil (gas) ignition burner to realize ignition automation. Guangdong Full automatic fuel oil steam generator The feeding, combustion, slag removal, water supply and ignition of the boiler can be automatically controlled, and the operation is convenient. The boiler is equipped with an automatic ash cleaning device, which can remove the ash on the heating surface of the boiler in time to ensure the efficient and stable operation of the boiler. The tail of the boiler is equipped with an economizer, or an air preheater according to the user's needs. Compared with traditional boilers, the boiler has higher efficiency and lower exhaust gas temperature. High efficiency thermal insulation materials are used, the boiler surface temperature is low, and the heat dissipation loss can be ignored. small-scale Full automatic fuel oil steam generator factory All pressure parts are made of excellent boiler steel in strict accordance with Chinese national codes and standards. Each boiler shall be strictly inspected and tested before leaving the factory, including hydrostatic test and X-ray inspection. Manholes, inspection doors, fire observation holes, etc. are set to facilitate maintenance. The major characteristics of biomass boiler are: energy conservation, environmental protection, and easy installation and use.
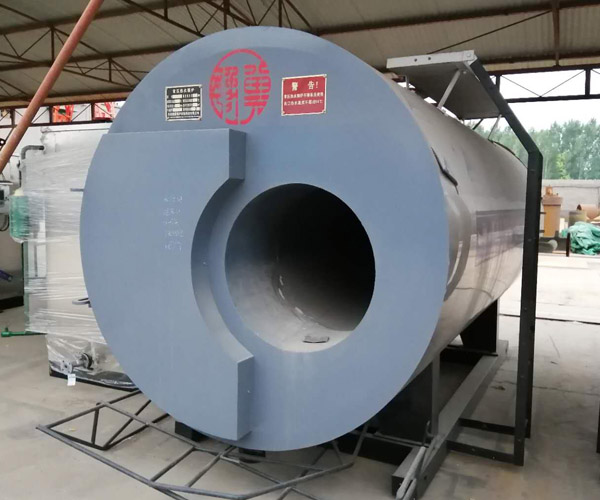
The furnace liner is the combustion chamber of the horizontal gas-fired heat transfer oil furnace. The burner nozzle is placed in the front of the furnace liner, and the high-temperature flue gas generated by combustion extends to the rear, leaving the furnace liner and returning to the space. Generally, the number of times of returning is not more than four, and the common one is the three return heat conduction oil furnace. Guangdong Full automatic fuel oil steam generator This type of heat transfer oil furnace can be divided into dry back type heat transfer oil furnace and full wet back type heat transfer oil furnace according to the structure of the flue gas reentry space at the rear of the furnace. The flue gas reentry space of the dry back heat conduction oil furnace is enclosed by refractory materials; The flue gas reentry space of the full wet back type heat conduction oil furnace is composed of a recuperative chamber immersed in water. In addition, there is a central regenerative heat conduction oil furnace: that is, the back wall of the furnace liner is sealed inside the boiler shell, and the flue gas is turned back to the front from the inner wall around the furnace liner after encountering. This type of heat transfer oil furnace can also be regarded as a full wet back heat transfer oil furnace. small-scale Full automatic fuel oil steam generator factory Although the dry back heat transfer oil furnace is simple in structure, the refractory material at the rear of the furnace liner is easily damaged, and the rear tube plate is often directly washed by high temperature flue gas. The temperature difference is large, so the dry back heat transfer oil furnace is obsolete. At present, few manufacturers produce it; Although the full wet back heat conduction oil furnace has a complex structure, it avoids the problem of flue gas sealing in the reentry space and is suitable for micro positive pressure combustion.
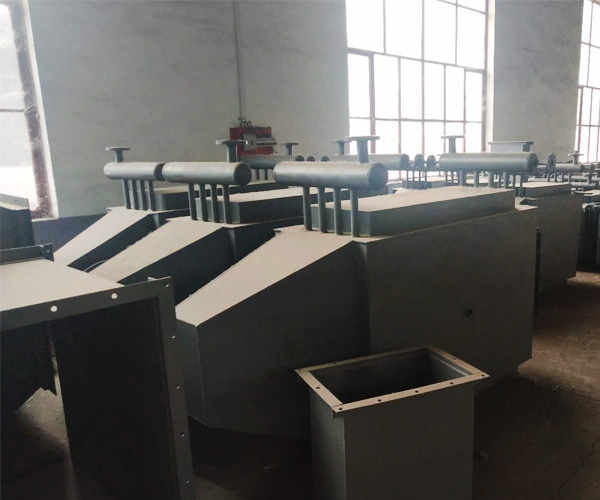
The manufacturer of the pneumatic water tank shall hold the pressure vessel manufacturing license or registration, and have a sound quality management system and system. Guangdong Full automatic fuel oil steam generator The purchased parts of the equipment must have the product certificate and pass the entrance inspection before use. The pneumatic water tank, water pump unit, electrical components and other components of the three-dimensional elastic filler manufacturer's equipment shall be assembled and used after passing the inspection. The equipment assembled on site can be used to inspect the performance of the whole machine on site. The production license issued by the relevant department shall be held. small-scale Full automatic fuel oil steam generator factory When selecting this product, requirements shall be put forward for the following items: equipment composition, equipment classification, equipment working pressure, equipment design flow, specification and quantity of air pressure tank, equipment data, and sanitary requirements. The overall structure of equipment, water pipe, gas pipe and electrical circuit shall be arranged reasonably, and the manufacturer of single hole mold aerator shall reserve space for device maintenance to facilitate operation. The pipeline of the equipment shall be equipped with a safety valve, and the opening pressure of the combined packing manufacturer shall not be greater than 1.1 times of the working pressure. The equipment shared by fire fighting and living (production) shall have a separate fire water outlet.
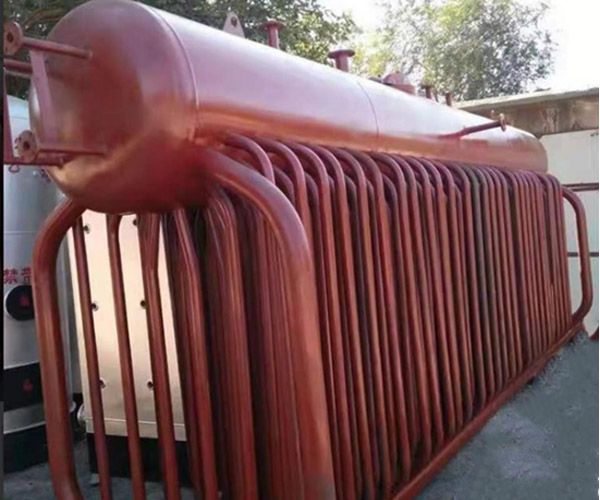
System oil drainage: circulate the heat transfer oil between 120 ± 5 to drain the heat transfer oil in the system (if you do not replace the oil, please find a clean container to store it properly). Prepare an appropriate amount of coke removal cleaning agent for the heat transfer oil system, drain the oil in the gas-fired heat transfer oil boiler system, and disconnect the cleaning system from the oil storage tank (close the valve), including the connection between the high-level tank and the oil storage tank. Guangdong Full automatic fuel oil steam generator Residual oil blowing steps: connect the air compressor at the pressure gauge or other places that can be connected, boost the system to 0.3-0.4MPa, and discharge it instantaneously; Repeat this process until the residual oil is blown out. The gas-fired heat transfer oil boiler, circulating pump, and other heat users form a cleaning circulating circuit for decoking and cleaning: add diluted cleaning agent to the system and fill it up to 1/2 of the water level of the high-level tank. Dosage of coke removal cleaning agent: 10~20%, the specific dosage shall be determined according to the scale thickness. Temperature: 90-95, time: 12-72 hours, which can be determined according to the scale thickness. Rinsing and cleaning: after cleaning, drain the residual liquid in the system and add clean water to rinse twice until the coke remover is free of foam and the water is clear. small-scale Full automatic fuel oil steam generator factory Temperature: 85-95, time: 5-8 hours Water blowing steps: after cleaning, connect the air compressor at the pressure gauge or other places that can be connected, use compressed air to boost the system to 0.3-0.4 MPa, and vent at each low point. Repeat this process until the water is blown out. Waste liquid treatment: the cleaning waste liquid generated in the cleaning process is discharged after being treated in the biochemical tank.