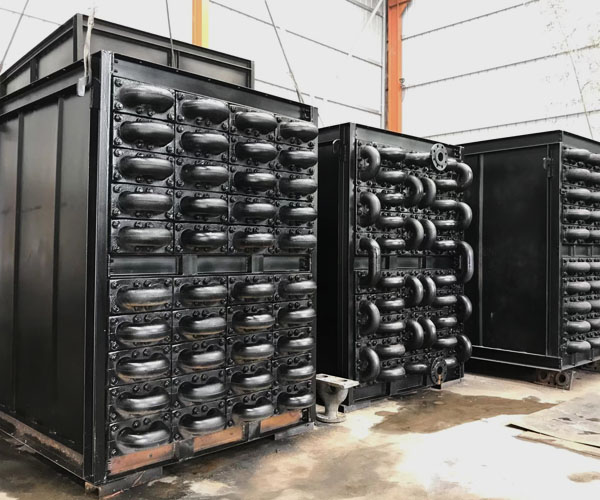
When using stainless steel storage tank, cracks appear on the head. If it is not handled in time, it will be dangerous, and how to handle this situation will be explained. Tianjin Waste heat boiler Firstly, the cracks in the stainless steel tank can were removed by polishing. After grinding, pits that do not need repair welding and do not affect the grading shall be formed within the allowable range. Otherwise, repair welding shall be carried out. The position of surface crack defect shall be determined by surface penetration defect detection, and the welding repair shall be completed. The horizontal gas tank shall be repaired, and the weld and surrounding materials shall be repaired. After that, argon tungsten arc welding shall be used for repair welding. vertical Waste heat boiler how much Tungsten argon arc welding shall be adopted for welding repair. It is suitable for back welding or skip welding, small size multi-layer and multi pass non rotating welding to avoid overheating of the weld. Water cooling measures are adopted. The defects of stainless steel storage tanks shall be removed by grinding with angular grinding wheel with conical grinding rod. Note that the abrasive grains of the grinding wheel should be perpendicular to the crack length. If the defect is deep, crack stop holes shall be drilled at both ends of the defect to prevent the crack from expanding with the grinding process. According to the inspection, in the stainless steel storage tank with primary side inspection, there are cracks at the head welds, and these defective welds have different edge bite degrees. Do not panic when the stainless steel tank can has cracks. The oil tank works. The above measures can be taken to solve this problem.
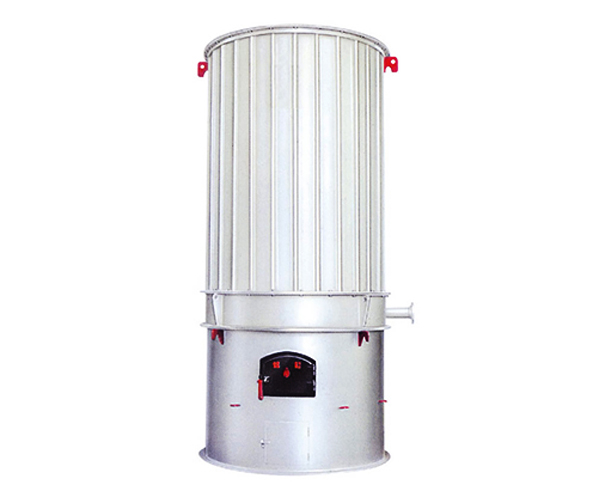
The starting of gas-fired boiler shall be carried out according to the operating procedures. The following is the accurate starting process of the analyzed gas-fired boiler: turn on the main power supply, start the gas-fired incinerator, and close the vent valve on the drum when it emits steam. Tianjin Waste heat boiler Check the manhole, handhole flange and valve of the gas boiler. If any leakage is found, fasten them. If leakage occurs after fastening, shut down the boiler for maintenance. When the gas pressure of the gas boiler rises by 0.05~0.1MPA, make up water, blow down, check the experimental water supply system and blow down equipment, and flush the water level gauge together. When the gas boiler pressure rises to 0.1~0.15MPA, flush the pressure gauge trap; When the gas pressure of the gas-fired boiler rises to 0.3MPA, turn the "load high fire/low fire" knob to "high fire" to strengthen incineration. When the pressure of the boiler rises to 2/3 of the operating pressure, start pipe warming and air supply, slowly open the main steam valve to prevent water hammer. vertical Waste heat boiler how much When the drain valve emits steam, close it. After all the drain valves are closed, slowly open the main gas valve to fully open, and then reverse it for half a circle. Turn the "Control of gas incinerator" knob to the automatic gear.
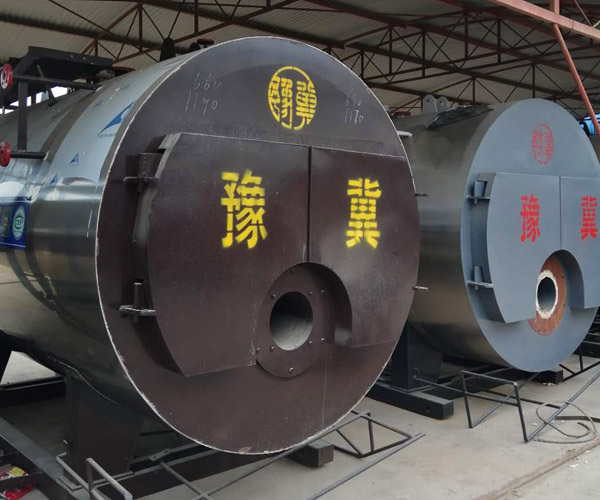
The existing industrial boiler flue gas waste heat recovery equipment mainly includes tubular heat exchanger and full heat pipe heat exchanger. Tube and tube heat exchanger can be composed of finned tube bundles. The advantage of finned tube is that it can withstand higher temperature, but has low heat transfer coefficient and large floor area. Tianjin Waste heat boiler The flue gas of industrial boilers contains sulfur and other acidic substances. In the low temperature zone (flue gas outlet section), the temperature may be lower than the dew point of the acidic substances. The acidic substances will dew on the pipe wall, corrode the shell of the fin tube. The fin tube heat exchanger has poor operating reliability and low service life. vertical Waste heat boiler how much The total heat pipe heat exchanger of boiler flue gas waste heat recovery equipment is composed of heat pipe bundles. Its shell is made of multi-layer composite materials. The heat pipe structure is complex, the cost is relatively expensive, the service life is short, and the steel consumption is large. It is difficult for users to accept it, and it is difficult to promote its application in production. The composite heat pipe heater not only takes into account the heat exchange effect, but also takes into account the economic affordability of the investors in production, which is particularly suitable for the current situation in China's industrial production.
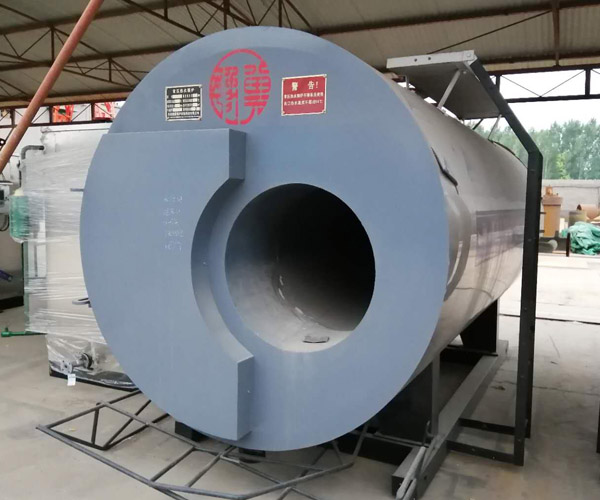
The main parts of the waste heat boiler can be divided into drum, pipe, header, membrane wall, tube panel, tube box, etc. These parts are the parts with specific process requirements in the waste heat boiler. Tianjin Waste heat boiler For example, the drum should go through metal flaw detection, heat treatment, hydrostatic test and other processes to improve the stability of the waste heat boiler. At the same time, because the header needs high sealing, manual welding is required, and the welding quality needs to be tested. It can be seen that due to the complexity of the working environment of the waste heat boiler, it has special requirements for its internal structural members. vertical Waste heat boiler how much In the process of designing and manufacturing the waste heat boiler, the process designer should consider the advantages and disadvantages of various processes, and then select a reasonable process to complete the manufacturing of the waste heat boiler. For example, the serpentine parts in the waste heat boiler cannot be bent automatically by the machine, so they can only be bent manually.