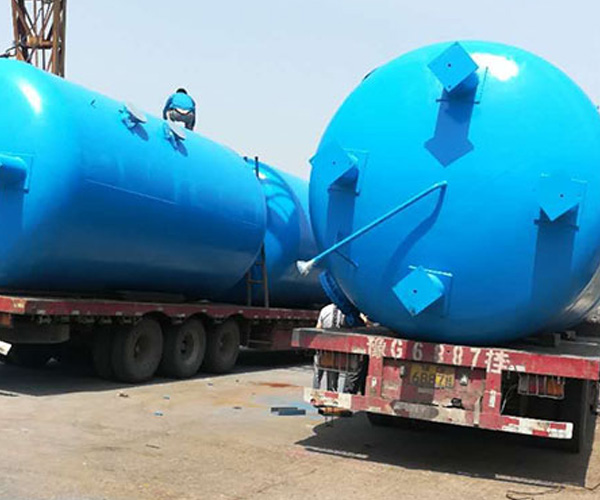
It can only be prevented by adding medicine to the pot. Sichuan electric steam generator Adding drugs to the boiler can further soften the water quality, making up that the softening water equipment cannot replace silicon, sulfur and heavy metal ions and anions, so that impurities such as suspended solids, water slag and scale in dissolved water have good looseness and fluidity, and then the impurities are discharged by sewage, thus preventing scale. The water treatment method is carried out in the pot, so it is called water treatment method in the pot. vertical electric steam generator manufactor Therefore, boiler water treatment actually includes water treatment of feed water and quantitative feeding treatment in the boiler. Water treatment should only be carried out without adding drugs. The boiler water index basically does not meet the specified requirements, and the boiler cannot operate under good water quality. This is also the main reason for the softened water device. The softened water is also qualified, and the boiler will also be polluted.
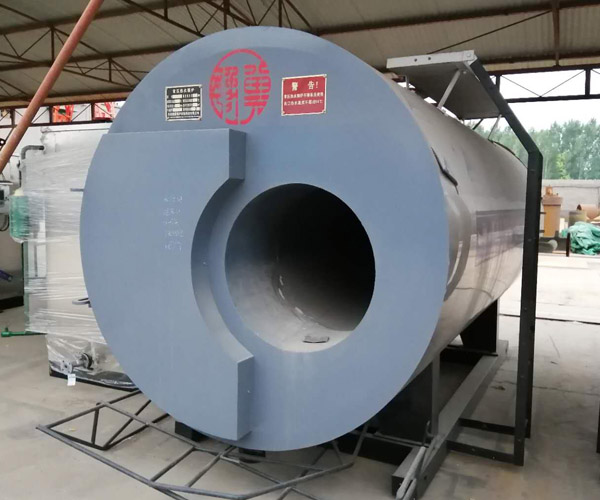
The furnace liner is the combustion chamber of the horizontal gas-fired heat transfer oil furnace. The burner nozzle is placed in the front of the furnace liner, and the high-temperature flue gas generated by combustion extends to the rear, leaving the furnace liner and returning to the space. Generally, the number of times of returning is not more than four, and the common one is the three return heat conduction oil furnace. Sichuan electric steam generator This type of heat transfer oil furnace can be divided into dry back type heat transfer oil furnace and full wet back type heat transfer oil furnace according to the structure of the flue gas reentry space at the rear of the furnace. The flue gas reentry space of the dry back heat conduction oil furnace is enclosed by refractory materials; The flue gas reentry space of the full wet back type heat conduction oil furnace is composed of a recuperative chamber immersed in water. In addition, there is a central regenerative heat conduction oil furnace: that is, the back wall of the furnace liner is sealed inside the boiler shell, and the flue gas is turned back to the front from the inner wall around the furnace liner after encountering. This type of heat transfer oil furnace can also be regarded as a full wet back heat transfer oil furnace. vertical electric steam generator manufactor Although the dry back heat transfer oil furnace is simple in structure, the refractory material at the rear of the furnace liner is easily damaged, and the rear tube plate is often directly washed by high temperature flue gas. The temperature difference is large, so the dry back heat transfer oil furnace is obsolete. At present, few manufacturers produce it; Although the full wet back heat conduction oil furnace has a complex structure, it avoids the problem of flue gas sealing in the reentry space and is suitable for micro positive pressure combustion.
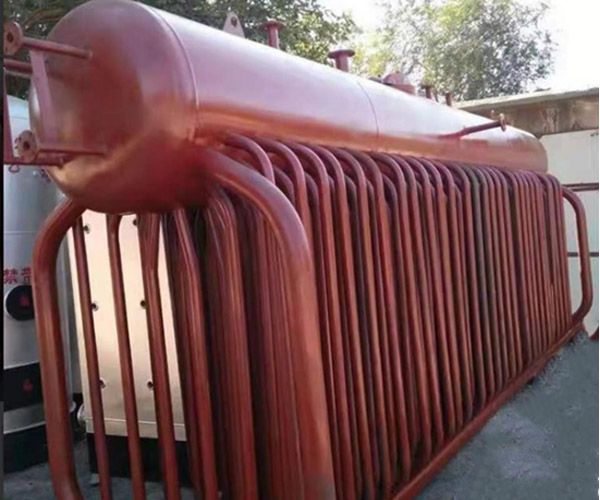
The waste heat recovery of flue gas can not only be used for heating or power generation to achieve energy-saving effect, but also can be beneficial to environmental protection and achieve dual effects of energy conservation and environmental protection. Sichuan electric steam generator In general, the important equipment of waste heat power generation is waste heat boiler, which mainly uses heat or combustible substances in waste gas, waste liquid and other working medium as heat source, and produces steam mainly for power generation. There are many ways to recover waste heat from flue gas of waste heat boiler. Generally, comprehensive utilization of waste heat is followed by direct utilization and indirect utilization. vertical electric steam generator manufactor Generally speaking, if heat sources are needed in the process, the waste heat utilization is mainly comprehensive utilization. First, the heat source is recovered and fed back to the process for reuse. If there is any surplus, it can be used for power generation or as the heat source for central heating; If there is no surplus, it will be directly used instead of being used for power generation; If the process does not need more heat sources, then indirect use, mainly power generation or public heating.
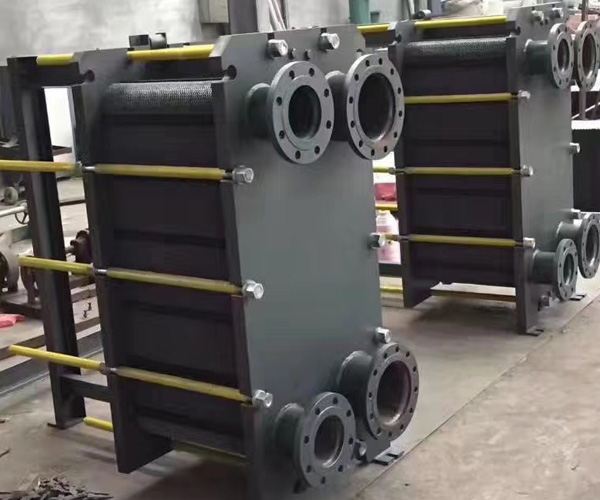
During the operation of the gas generator set, the full combustion of gas and air generates a large amount of heat energy. The heat energy is converted into mechanical energy through the crankshaft connecting rod mechanism, and the generator converts this mechanical energy into electrical energy. However, some of the heat energy is still taken away by the exhaust gas and discharged from the cylinder block, resulting in the exhaust gas emission temperature of 500-600 ℃. In order to avoid this part of heat loss, waste heat boiler is used. If the high-temperature waste gas is directly discharged without treatment, it will inevitably cause excessive temperature in the workshop, accelerate the aging of equipment, affect the service life of equipment, and lead to a large use of cooling circulating water for the unit. If the waste heat boiler is installed, it can not only solve the above problems, but also generate steam energy for production and domestic use in the mine, so as to realize the recycling and comprehensive utilization of resources.
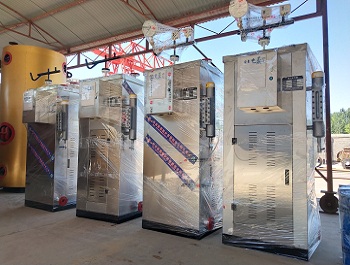
Most people may already know something about flue gas waste heat recovery, because they have already explained a lot about it. In order to let you know the relevant knowledge of flue gas waste heat recovery, the following is a brief introduction to the two methods commonly used for recovery. Sichuan electric steam generator Two methods are usually adopted for flue gas waste heat recovery: one is to preheat the workpiece; The other is to preheat air for combustion support. The flue gas preheating workpiece needs to occupy a large volume for heat exchange, which is often limited by the operation site (this method cannot be used for furnaces that are used intermittently). vertical electric steam generator manufactor Preheating air for combustion support is a good method. It is generally configured on the heating furnace, which can also strengthen combustion, speed up the temperature rise of the furnace, and improve the thermal performance of the furnace. This can not only meet the requirements of the process, but also achieve significant comprehensive energy-saving effect.