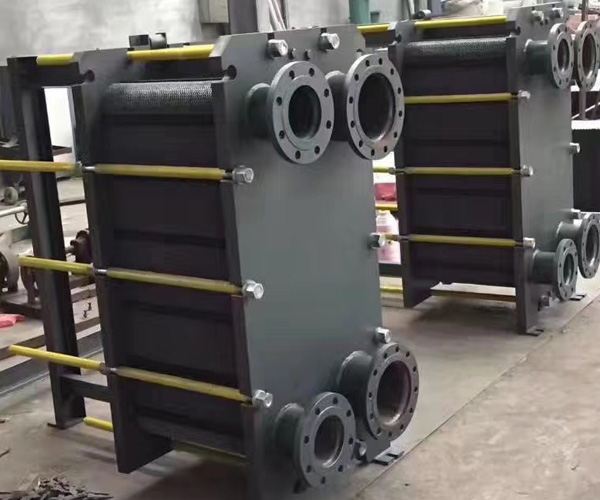
The starting of gas-fired boiler shall be carried out according to the operating procedures. The following is the accurate starting process of the analyzed gas-fired boiler: turn on the main power supply, start the gas-fired incinerator, and close the vent valve on the drum when it emits steam. Shanxi Steam generator Check the manhole, handhole flange and valve of the gas boiler. If any leakage is found, fasten them. If leakage occurs after fastening, shut down the boiler for maintenance. When the gas pressure of the gas boiler rises by 0.05~0.1MPA, make up water, blow down, check the experimental water supply system and blow down equipment, and flush the water level gauge together. When the gas boiler pressure rises to 0.1~0.15MPA, flush the pressure gauge trap; When the gas pressure of the gas-fired boiler rises to 0.3MPA, turn the "load high fire/low fire" knob to "high fire" to strengthen incineration. When the pressure of the boiler rises to 2/3 of the operating pressure, start pipe warming and air supply, slowly open the main steam valve to prevent water hammer. vertical Steam generator factory When the drain valve emits steam, close it. After all the drain valves are closed, slowly open the main gas valve to fully open, and then reverse it for half a circle. Turn the "Control of gas incinerator" knob to the automatic gear.
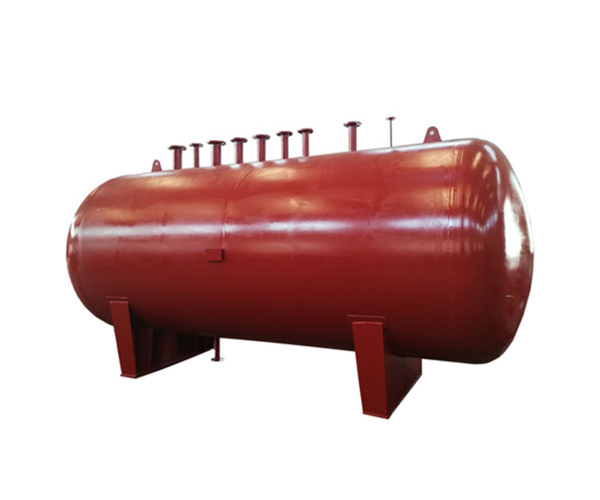
After the cold furnace of oil fired and gas fired boiler is ignited, the speed of temperature rise shall be controlled at 10 ℃/hour, mainly because the viscosity of oil temperature is large when it is cold, and the flow rate in the heating surface pipe of the whole equipment is relatively low. Shanxi Steam generator The oil film on the pipe wall is thick, so the heat transfer condition is poor when in use. If the heating speed of oil and gas fired boiler is too fast during use, it is easy to make the local oil film temperature too high. The equipment is in the stage of driving away the residual moisture and moisture contained in the heat conduction fluid in the system within the temperature range. vertical Steam generator factory In oil and gas fired boiler, when the steam exhaust volume at the vent pipe of the expander is relatively large, there will be water hammer at the bottom of the equipment. In this way, the vibration of the pipeline will accelerate, and when the swing amplitude of the pressure gauge pointer in each part of the equipment is large, the temperature rise will be stopped and the constant temperature state will be maintained.
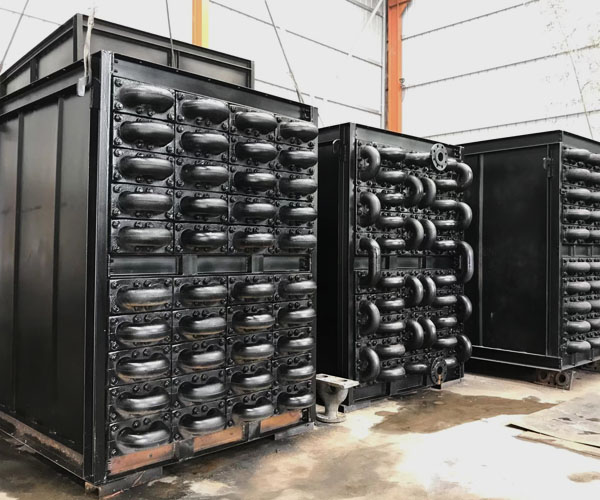
During the operation of the gas generator set, the full combustion of gas and air generates a large amount of heat energy. The heat energy is converted into mechanical energy through the crankshaft connecting rod mechanism, and the generator converts this mechanical energy into electrical energy. However, some of the heat energy is still taken away by the exhaust gas and discharged from the cylinder block, resulting in the exhaust gas emission temperature of 500-600 ℃. In order to avoid this part of heat loss, waste heat boiler is used. If the high-temperature waste gas is directly discharged without treatment, it will inevitably cause excessive temperature in the workshop, accelerate the aging of equipment, affect the service life of equipment, and lead to a large use of cooling circulating water for the unit. If the waste heat boiler is installed, it can not only solve the above problems, but also generate steam energy for production and domestic use in the mine, so as to realize the recycling and comprehensive utilization of resources.
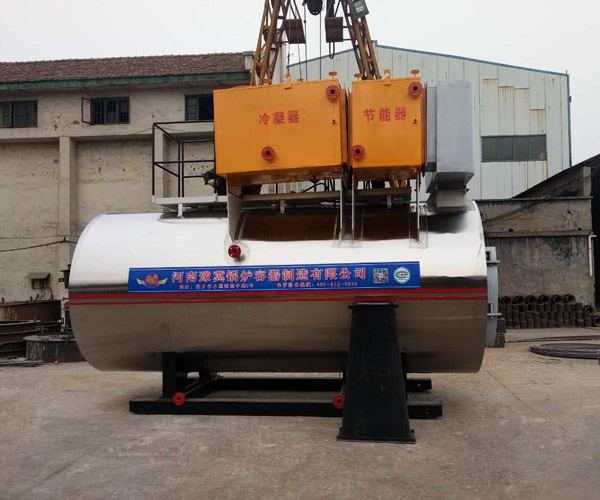
The main parts of the waste heat boiler can be divided into drum, pipe, header, membrane wall, tube panel, tube box, etc. These parts are the parts with specific process requirements in the waste heat boiler. Shanxi Steam generator For example, the drum should go through metal flaw detection, heat treatment, hydrostatic test and other processes to improve the stability of the waste heat boiler. At the same time, because the header needs high sealing, manual welding is required, and the welding quality needs to be tested. It can be seen that due to the complexity of the working environment of the waste heat boiler, it has special requirements for its internal structural members. vertical Steam generator factory In the process of designing and manufacturing the waste heat boiler, the process designer should consider the advantages and disadvantages of various processes, and then select a reasonable process to complete the manufacturing of the waste heat boiler. For example, the serpentine parts in the waste heat boiler cannot be bent automatically by the machine, so they can only be bent manually.
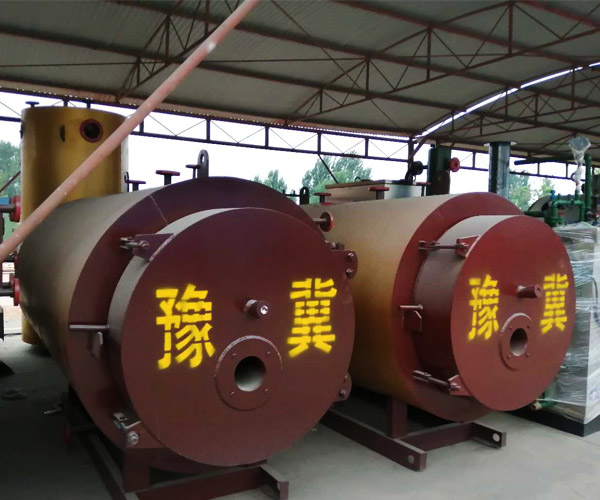
The furnace liner is the combustion chamber of the horizontal gas-fired heat transfer oil furnace. The burner nozzle is placed in the front of the furnace liner, and the high-temperature flue gas generated by combustion extends to the rear, leaving the furnace liner and returning to the space. Generally, the number of times of returning is not more than four, and the common one is the three return heat conduction oil furnace. Shanxi Steam generator This type of heat transfer oil furnace can be divided into dry back type heat transfer oil furnace and full wet back type heat transfer oil furnace according to the structure of the flue gas reentry space at the rear of the furnace. The flue gas reentry space of the dry back heat conduction oil furnace is enclosed by refractory materials; The flue gas reentry space of the full wet back type heat conduction oil furnace is composed of a recuperative chamber immersed in water. In addition, there is a central regenerative heat conduction oil furnace: that is, the back wall of the furnace liner is sealed inside the boiler shell, and the flue gas is turned back to the front from the inner wall around the furnace liner after encountering. This type of heat transfer oil furnace can also be regarded as a full wet back heat transfer oil furnace. vertical Steam generator factory Although the dry back heat transfer oil furnace is simple in structure, the refractory material at the rear of the furnace liner is easily damaged, and the rear tube plate is often directly washed by high temperature flue gas. The temperature difference is large, so the dry back heat transfer oil furnace is obsolete. At present, few manufacturers produce it; Although the full wet back heat conduction oil furnace has a complex structure, it avoids the problem of flue gas sealing in the reentry space and is suitable for micro positive pressure combustion.
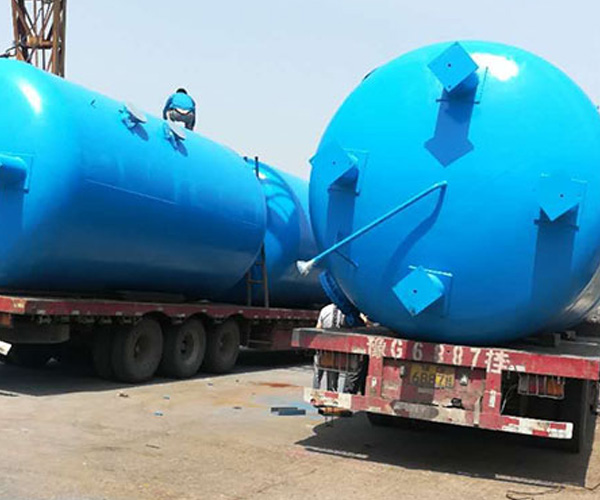
The waste heat boiler has advantages in the subdivided industry and is the leading enterprise in the industry. The company's main products are various types of waste heat boilers, industrial boilers, power station boilers, nuclear power equipment and power station auxiliaries. It is a research, development, design and manufacturing base for waste heat boilers with large scale and complete varieties in China. Shanxi Steam generator Waste heat boiler is a typical energy-saving and emission reduction equipment. Its heat source can come from high-temperature flue gas waste heat, chemical reaction waste heat, combustible waste gas waste heat, and even can use high-temperature product waste heat. At present, the company has more than 20 series and more than 100 varieties of waste heat boiler products, which are widely used in steel, building materials, power, nonferrous metals, coking, chemical and other industries. vertical Steam generator factory In 2008, the company produced 272 sets of waste heat boilers of various types, with a total of 10268 steam tons, accounting for 34% of the comprehensive market share based on steam tons; According to the output value, the market share is 47%, ranking first in the waste heat boiler industry.