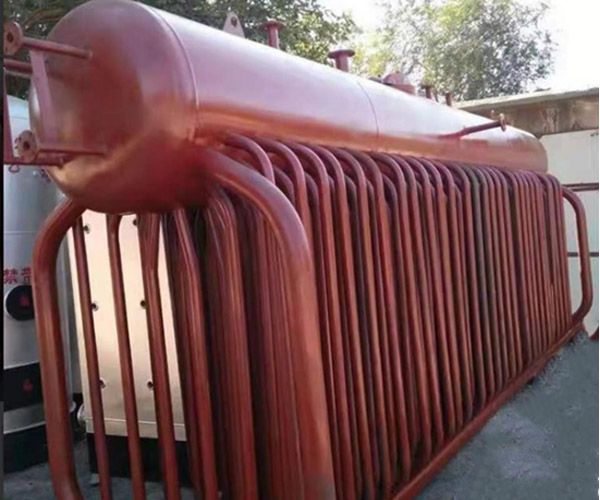
The main parts of the waste heat boiler can be divided into drum, pipe, header, membrane wall, tube panel, tube box, etc. These parts are the parts with specific process requirements in the waste heat boiler. Yunnan Fully automatic steam generator For example, the drum should go through metal flaw detection, heat treatment, hydrostatic test and other processes to improve the stability of the waste heat boiler. At the same time, because the header needs high sealing, manual welding is required, and the welding quality needs to be tested. It can be seen that due to the complexity of the working environment of the waste heat boiler, it has special requirements for its internal structural members. small-scale Fully automatic steam generator factory In the process of designing and manufacturing the waste heat boiler, the process designer should consider the advantages and disadvantages of various processes, and then select a reasonable process to complete the manufacturing of the waste heat boiler. For example, the serpentine parts in the waste heat boiler cannot be bent automatically by the machine, so they can only be bent manually.
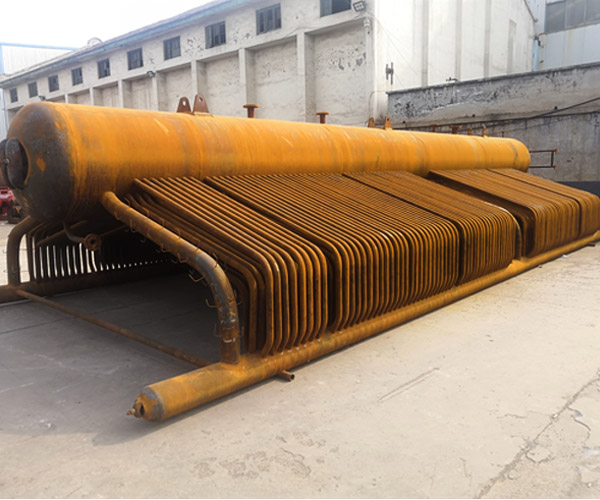
You will find that the characteristics of industrial boiler equipment are obvious. When designing industrial boilers, they should be regularly maintained. Vertical boilers have obvious characteristics Yunnan Fully automatic steam generator The combustion part adopts a double-layer grate combustion chamber, which has fast temperature rise and pressure rise, reasonable overall layout, good heat transfer, sufficient combustion, smoke suppression and dust removal for unburned gas after secondary combustion, and is one of the smaller steam and heating equipment. small-scale Fully automatic steam generator factory The characteristics of the whole industrial boiler are obvious, with high thermal efficiency and sufficient steam. The whole industrial boiler is equipped with excellent safety valve, pressure regulator, low water level and other multiple protection devices, which can effectively ensure the safe operation of the boiler. Moreover, industrial boiler equipment is compact in structure, small in floor area, elegant in shape and bright in color. Therefore, it plays an important role in many large factories and coal mining enterprises.
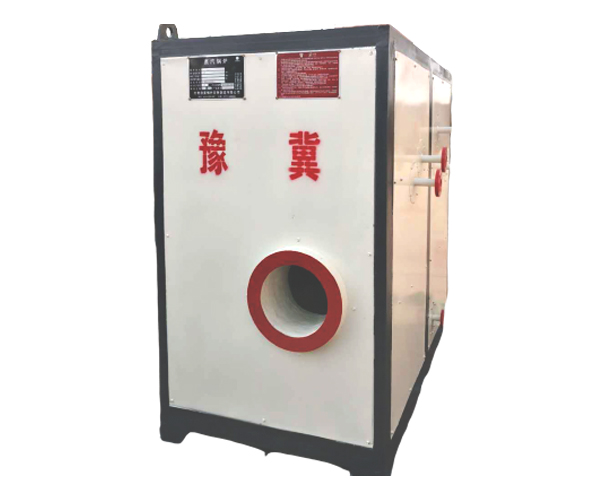
When using stainless steel storage tank, cracks appear on the head. If it is not handled in time, it will be dangerous, and how to handle this situation will be explained. Yunnan Fully automatic steam generator Firstly, the cracks in the stainless steel tank can were removed by polishing. After grinding, pits that do not need repair welding and do not affect the grading shall be formed within the allowable range. Otherwise, repair welding shall be carried out. The position of surface crack defect shall be determined by surface penetration defect detection, and the welding repair shall be completed. The horizontal gas tank shall be repaired, and the weld and surrounding materials shall be repaired. After that, argon tungsten arc welding shall be used for repair welding. small-scale Fully automatic steam generator factory Tungsten argon arc welding shall be adopted for welding repair. It is suitable for back welding or skip welding, small size multi-layer and multi pass non rotating welding to avoid overheating of the weld. Water cooling measures are adopted. The defects of stainless steel storage tanks shall be removed by grinding with angular grinding wheel with conical grinding rod. Note that the abrasive grains of the grinding wheel should be perpendicular to the crack length. If the defect is deep, crack stop holes shall be drilled at both ends of the defect to prevent the crack from expanding with the grinding process. According to the inspection, in the stainless steel storage tank with primary side inspection, there are cracks at the head welds, and these defective welds have different edge bite degrees. Do not panic when the stainless steel tank can has cracks. The oil tank works. The above measures can be taken to solve this problem.
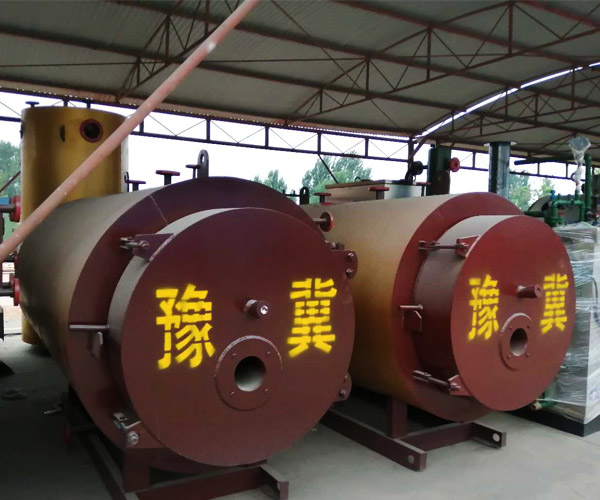
Energy saving. The waste heat boiler adopts new heat exchange fins and heat exchange elements, which enables full heat exchange. The boiler efficiency can be increased by 6~15%, and the condensate drainage structure can fully recover the latent heat in the flue gas. The energy-saving effect is remarkable. Yunnan Fully automatic steam generator Due to the special structure, the total pressure drop is small and the power consumption is small, that is, the smoke pressure drop is small and meets the system requirements. beautiful. Due to the use of efficient heat exchange elements and reasonable structural configuration, the waste heat boiler has the characteristics of compact structure, small size, beautiful appearance, etc. Durable. Heat exchange tubes of waste heat boiler facilities are made of stainless steel aluminum fins for corrosion prevention. small-scale Fully automatic steam generator factory The thermal stress, anti-corrosion performance and strength are fully considered when the equipment is manufactured, which can ensure the safety, reliability and stability of the equipment, with a service life of more than 25 years.
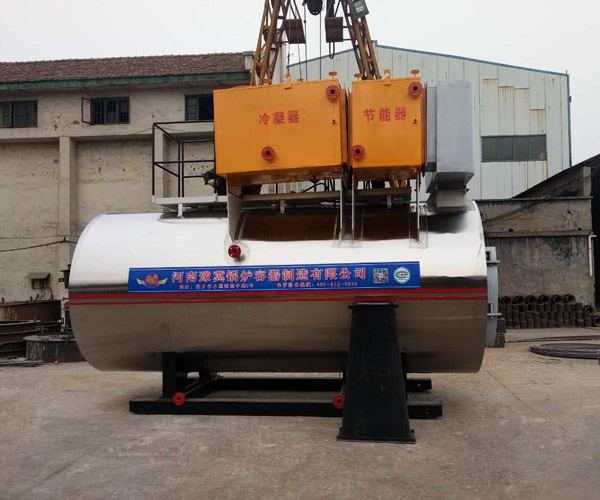
System oil drainage: drain the heat transfer oil in the system when the circulating heat transfer oil is between 120 ± 5 (if the oil is not replaced, please find a clean container for proper storage) Prepare an appropriate amount of coke removal cleaning agent for the heat transfer oil system, drain the oil in the gas-fired heat transfer oil boiler system, and disconnect the cleaning system from the oil storage tank (close the valve), including the connection between the high-level tank and the oil storage tank. Yunnan Fully automatic steam generator Residual oil blowing steps: connect the air compressor at the pressure gauge or other places that can be connected, boost the system to 0.3-0.4MPa, and discharge it instantaneously; Repeat this process until the residual oil is blown out. The gas-fired heat transfer oil boiler, circulating pump, and other heat users form a cleaning circulating circuit for decoking and cleaning: add diluted cleaning agent to the system and fill it up to 1/2 of the water level of the high-level tank. Dosage of coke removal cleaning agent: 10~20%, the specific dosage shall be determined according to the scale thickness. Temperature: 90-95, time: 12-72 hours, which can be determined according to the scale thickness. Rinsing and cleaning: after cleaning, drain the residual liquid in the system and add clean water to rinse twice until the coke remover is free of foam and the water is clear. small-scale Fully automatic steam generator factory Temperature: 85-95, time: 5-8 hours Water blowing steps: after cleaning, connect the air compressor at the pressure gauge or other places that can be connected, use compressed air to boost the system to 0.3-0.4 MPa, and vent at each low point. Repeat this process until the water is blown out. Waste liquid treatment: the cleaning waste liquid generated in the cleaning process is discharged after being treated in the biochemical tank.