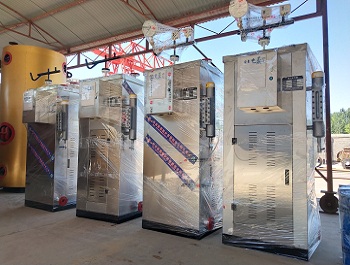
Economical and energy-saving: the new generation of biomass pellet fuel can save 30% - 60% of the operating cost compared with oil, gas and electric heating boilers. Convenient installation: this series of generators do not need to be inspected, and the tedious annual approval procedure can be avoided. Hebei electric steam generator At the same time, the machine is assembled for modules, and professional installation procedures are not required. High efficiency operation: adopt the design of multiple flue gas backflow, optimize oxygen enrichment for many times, cooperate with professional dust removal and energy saving equipment, the thermal efficiency reaches more than 90%, and can continuously produce steam. Low carbon and environmental protection: Through reasonable design, biomass fuel is semi gasified and burned, and smokeless combustion is achieved. Reliable security: It is equipped with pressure, water shortage, security valve and other protection devices to ensure stable operation and reliable security of the boiler. small-scale electric steam generator factory Simple operation: microcomputer intelligent one button operation, automatic feeding, automatic ignition, cycle start stop and fault alarm functions are used for simple operation. The labor intensity is greatly reduced, and the use of the boiler is more humanized. Convenient maintenance: the overall structure of the boiler is reasonable, and the installation is convenient. There is a cleaning port under each furnace. The main components have inspection ports for future maintenance and repair.
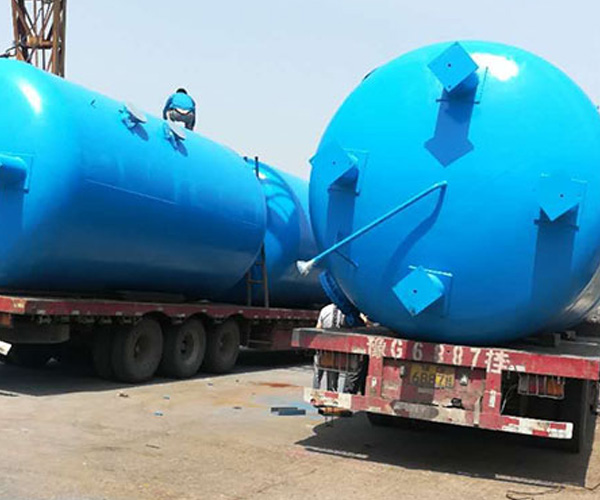
The waste heat boiler greatly improves the utilization rate of heat released by fuel combustion, so this kind of boiler saves energy; Fuel oil, gas and coal combustion generate high-temperature flue gas to release heat. The high-temperature flue gas first enters the furnace, then enters the waste heat recovery device of the front smoke box, then enters the pyrotechnic tube, and then enters the waste heat recovery device in the flue of the rear smoke box. The high-temperature flue gas turns into low-temperature flue gas and is discharged into the atmosphere through the chimney. Hebei electric steam generator Conditions conducive to quick startup of waste heat boiler: (1) The waste heat boiler adopts forced circulation, which has the priority of quick startup. (2) The flue gas baffle is hydraulically controlled, which can be used to adjust the sky in principle. The flue gas flow into the boiler is reduced. (3) The adjustable guide vane at the inlet of gas turbine can not only adjust the flue gas flow of gas turbine, but also increase or decrease the exhaust gas temperature of gas turbine through the selection of IGV temperature control mode. (4) The steam turbine bypass is designed for the rated evaporation capacity of the boiler. (5) The welded bends and headers of each heating module of the boiler are in the boiler. (6) Similar boilers in other gas turbine power plants can not be reduced when starting, and can be used to adjust the main steam pressure of the boiler. Outside the wall, contact with high-temperature smoke is avoided. small-scale electric steam generator factory Operating experience of gas turbine load, such as simultaneous startup of gas turbine and waste heat boiler (flue gas damper fully open). Under the possibility of quick startup of waste heat boiler, the water level of steam drum and deaerator will lose control after the flue gas baffle is opened.
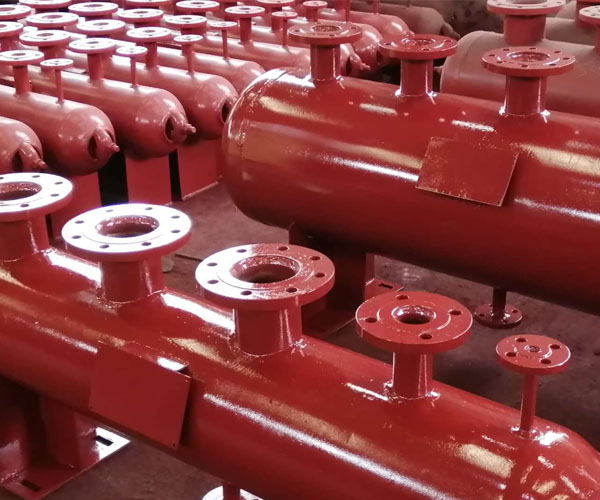
After the cold furnace of oil fired and gas fired boiler is ignited, the speed of temperature rise shall be controlled at 10 ℃/hour, mainly because the viscosity of oil temperature is large when it is cold, and the flow rate in the heating surface pipe of the whole equipment is relatively low. Hebei electric steam generator The oil film on the pipe wall is thick, so the heat transfer condition is poor when in use. If the heating speed of oil and gas fired boiler is too fast during use, it is easy to make the local oil film temperature too high. The equipment is in the stage of driving away the residual moisture and moisture contained in the heat conduction fluid in the system within the temperature range. small-scale electric steam generator factory In oil and gas fired boiler, when the steam exhaust volume at the vent pipe of the expander is relatively large, there will be water hammer at the bottom of the equipment. In this way, the vibration of the pipeline will accelerate, and when the swing amplitude of the pressure gauge pointer in each part of the equipment is large, the temperature rise will be stopped and the constant temperature state will be maintained.
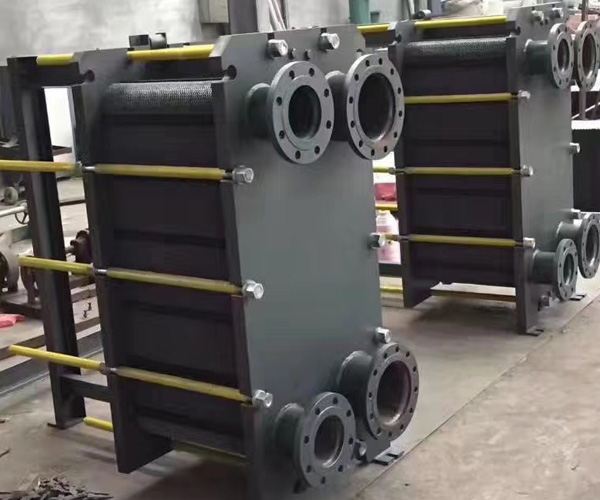
High heat exchange efficiency. The fusion rate at the contact is more than 95%, the contact thermal resistance is small, and the thermal conductivity is good. Low flow resistance. Hebei electric steam generator Since H-shaped finned tubes are similar to square structures, after being assembled into heat exchangers, the tubes are divided into many small channels by fins, which has a certain uniform effect on the air flow. The air flow is similar to longitudinal downstream flow, and the air flow resistance is relatively small. However, spiral finned tubes have strong air flow disturbance, high turbulence, and large air flow resistance due to the directivity of the fins. Less ash. The flue gas contains fly ash, which is easy to deposit on the windward side and leeward side of the pipe bundle. The H-shaped fin tube bundle has the characteristics of flow equalization and downstream flow, which is not easy to cause serious local ash deposition, and the fly ash can be taken away with the air flow in time. Therefore, compared with spiral finned tube heat exchanger, H-type finned tube heat exchanger has less ash deposition. small-scale electric steam generator factory Small size and low weight. H-shaped finned tube has high area expansion rate, less ash deposition, and high heat transfer efficiency. When the heat transfer capacity is equal, the space occupied by the heat exchanger can be small. For reconstruction projects, the heat exchange area can be arranged as much as possible in the limited space to reduce the exhaust gas temperature, improve the waste heat recovery efficiency, or increase the maintenance space to facilitate maintenance.