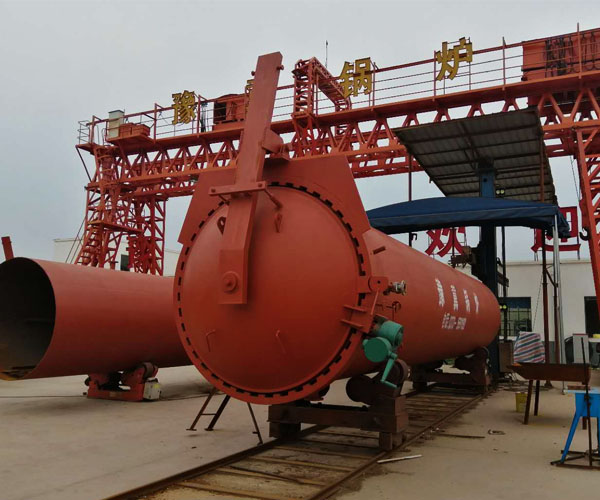
Diaphragm air pressure tank is an energy storage device composed of a steel shell and a rubber diaphragm liner. The rubber diaphragm completely separates the water chamber from the air chamber. When water with external pressure is filled into the liner of the diaphragm air pressure tank, the air sealed in the diaphragm air pressure tank will be compressed. Shanxi Fuel gas steam generator According to Boyle's gas law, the volume of gas becomes smaller after being compressed, and the pressure increases to store energy. The expansion of compressed gas can press the water in the rubber diaphragm out of the tank. Diaphragm pressure tank is widely used in central air conditioning, boiler, water heater, frequency conversion and constant pressure water supply equipment. It can buffer the pressure fluctuation of the system and eliminate water hammer to stabilize the pressure and unload the load. vertical Fuel gas steam generator factory When the water pressure in the system changes slightly, the automatic expansion and contraction of the diaphragm air pressure capsule will have a buffer effect on the change of water pressure, which can ensure the stability of the water pressure in the system, and the water pump will not be opened frequently due to the change of pressure.
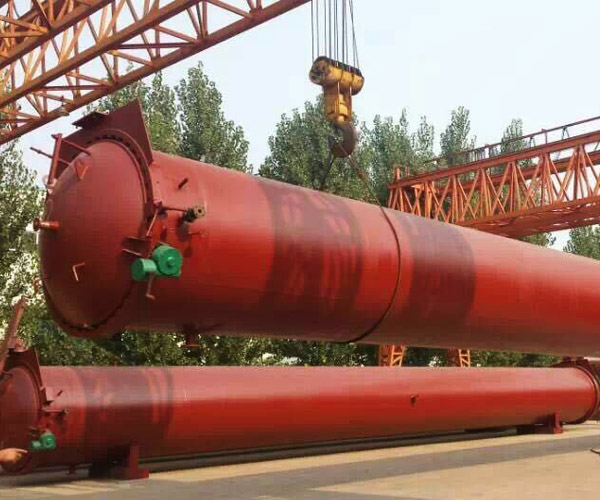
System oil drainage: drain the heat transfer oil in the system when the circulating heat transfer oil is between 120 ± 5 (if the oil is not replaced, please find a clean container for proper storage) Prepare an appropriate amount of coke removal cleaning agent for the heat transfer oil system, drain the oil in the gas-fired heat transfer oil boiler system, and disconnect the cleaning system from the oil storage tank (close the valve), including the connection between the high-level tank and the oil storage tank. Shanxi Fuel gas steam generator Residual oil blowing steps: connect the air compressor at the pressure gauge or other places that can be connected, boost the system to 0.3-0.4MPa, and discharge it instantaneously; Repeat this process until the residual oil is blown out. The gas-fired heat transfer oil boiler, circulating pump, and other heat users form a cleaning circulating circuit for decoking and cleaning: add diluted cleaning agent to the system and fill it up to 1/2 of the water level of the high-level tank. Dosage of coke removal cleaning agent: 10~20%, the specific dosage shall be determined according to the scale thickness. Temperature: 90-95, time: 12-72 hours, which can be determined according to the scale thickness. Rinsing and cleaning: after cleaning, drain the residual liquid in the system and add clean water to rinse twice until the coke remover is free of foam and the water is clear. vertical Fuel gas steam generator factory Temperature: 85-95, time: 5-8 hours Water blowing steps: after cleaning, connect the air compressor at the pressure gauge or other places that can be connected, use compressed air to boost the system to 0.3-0.4 MPa, and vent at each low point. Repeat this process until the water is blown out. Waste liquid treatment: the cleaning waste liquid generated in the cleaning process is discharged after being treated in the biochemical tank.
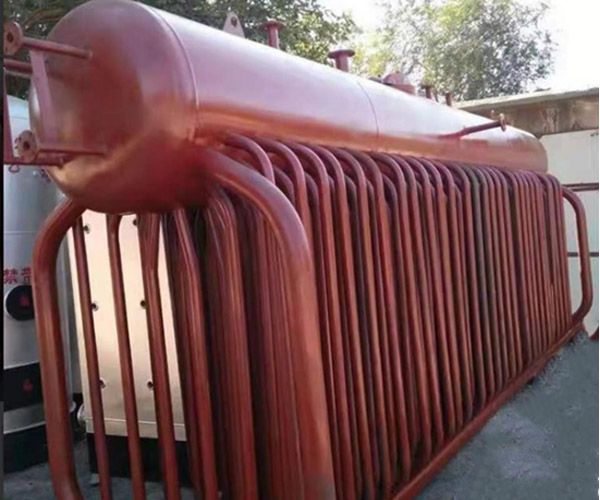
Waste heat boilers are widely used in high energy consumption industries. There are two common types of waste heat boilers: one is used to recover the exhaust gas emitted by ordinary boilers, such as fuel fired and gas-fired boilers, biomass fired boilers, etc. The temperature of the exhaust gas from ordinary boilers is about 600 ℃, which is not too high, Therefore, the requirements for waste heat recovery boiler are relatively low. Shanxi Fuel gas steam generator The other is industrial waste heat recovery boiler, such as building materials industry, chemical industry, steel making industry, etc. The temperature of waste gas and waste heat in these industries is high, and the recovery and utilization are also quite valuable. vertical Fuel gas steam generator factory Henan Yuji Boiler Vessel Manufacturing Co., Ltd., founded in 2005, is located at No. 8, Jizhong Road, Xiaoji Town, Xinxiang County, Henan Province. It is a comprehensive enterprise of boiler and pressure vessel, mainly engaged in the manufacturing of boilers and pressure vessels, with technological innovation as the core, integrating the design, manufacturing, sales, installation, transformation and maintenance of boilers and pressure vessels.
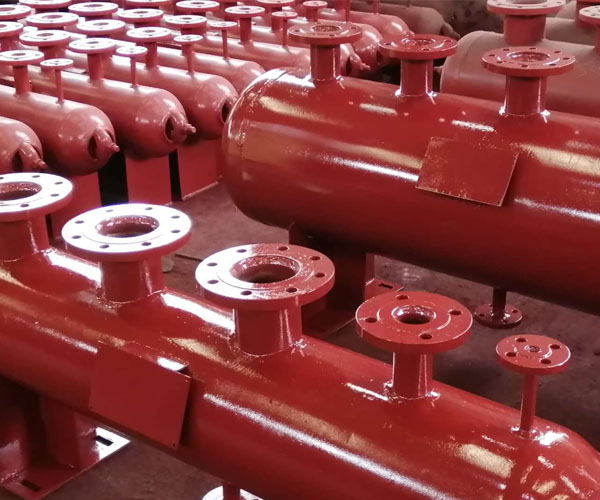
Economical and energy-saving: the new generation of biomass pellet fuel can save 30% - 60% of the operating cost compared with oil, gas and electric heating boilers. Convenient installation: this series of generators do not need to be inspected, and the tedious annual approval procedure can be avoided. Shanxi Fuel gas steam generator At the same time, the machine is assembled for modules, and professional installation procedures are not required. High efficiency operation: adopt the design of multiple flue gas backflow, optimize oxygen enrichment for many times, cooperate with professional dust removal and energy saving equipment, the thermal efficiency reaches more than 90%, and can continuously produce steam. Low carbon and environmental protection: Through reasonable design, biomass fuel is semi gasified and burned, and smokeless combustion is achieved. Reliable security: It is equipped with pressure, water shortage, security valve and other protection devices to ensure stable operation and reliable security of the boiler. vertical Fuel gas steam generator factory Simple operation: microcomputer intelligent one button operation, automatic feeding, automatic ignition, cycle start stop and fault alarm functions are used for simple operation. The labor intensity is greatly reduced, and the use of the boiler is more humanized. Convenient maintenance: the overall structure of the boiler is reasonable, and the installation is convenient. There is a cleaning port under each furnace. The main components have inspection ports for future maintenance and repair.
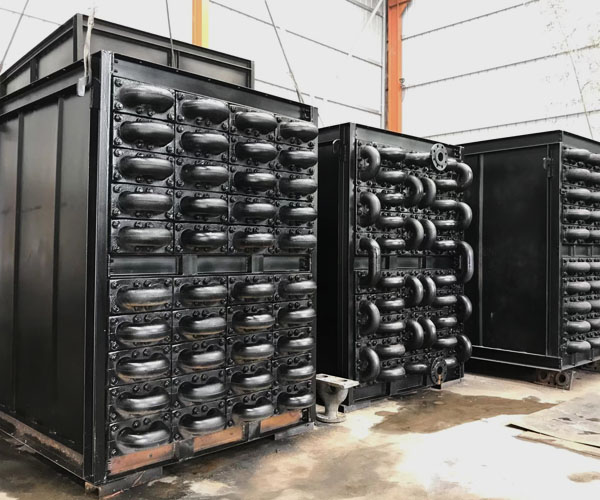
As a large equipment, the maintenance of gas-fired hot blast stove is one of the things that must be done. Shanxi Fuel gas steam generator Regular maintenance can not only keep the hot blast stove clean, but also improve the service life of the hot blast stove. Therefore, it is the top priority in the use of hot blast stove. Today's editor will tell you how to maintain the hot blast stove regularly. In many manufacturers that use hot blast stoves, in order to better develop the enterprise, it is necessary to increase the number of hot blast stoves and improve the performance of hot blast stoves. vertical Fuel gas steam generator factory When enterprises purchase hot blast stove equipment, they must understand their own needs and the products of hot blast stove manufacturers in the market. Therefore, the small edition of gas-fired hot blast stove tells us the problems to be considered in the selection of hot blast stove.
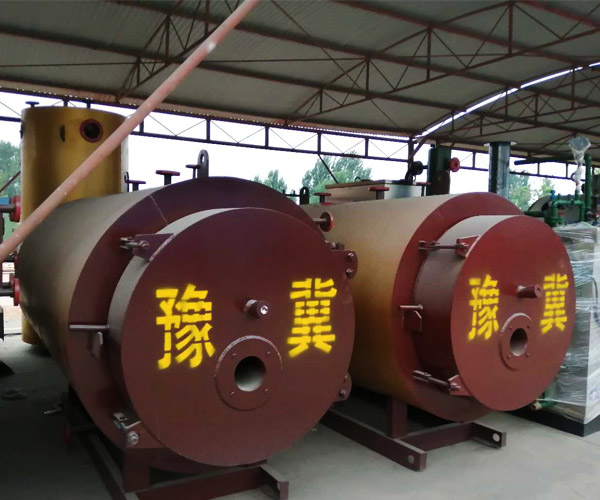
When the boiler is shut down, the temperature of the heat transfer oil can be reduced to below 70 ℃ before the shutdown of the hot oil pump. In case of sudden power failure, extinguish the fire immediately, and then implement the operating procedures. Otherwise, the furnace tube will be burned out and the loss will be large. According to the type of heat transfer oil boiler, heat transfer oil shall be reasonably selected to prevent overheating. Shanxi Fuel gas steam generator When purchasing unqualified heat transfer oil, do not save money or mix heat transfer oil indiscriminately. Otherwise, the consequences will be very serious. Prevent the oxidation of heat transfer oil. The strict heat transfer oil is more than 50 degrees in contact with the air, which will make the heat transfer oil crack. Its speed is amazing, and the consequences are relatively serious. After normal operation, the test crew needs to close the exhaust valve on the auxiliary exhaust pipe. After 6 months of use, the heat transfer oil must be sampled and tested according to the instructions. If problems are found, the heat transfer oil must be replaced immediately. vertical Fuel gas steam generator factory However, it should be noted that different types of heat transfer oil should not be mixed. The circulation speed of the heat transfer oil should not be less than 1.5m/s. Due to the excessive temperature difference between some entrances and exits, the original design requirements were destroyed, the heat transfer oil could not maintain the original circulation state, the boundary layer became thicker, and the thermal resistance became larger, making the furnace wall exceed the oil film temperature, leading to carbon deposition, cracking, polymerization, coking, and even burning through the furnace tube.