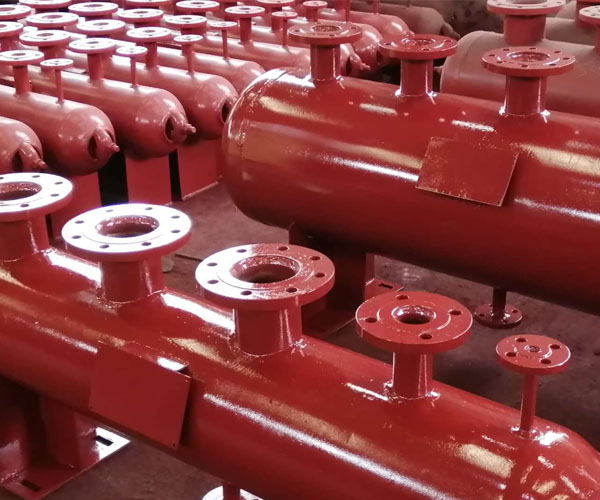
Waste heat boilers are widely used in high energy consumption industries. There are two common types of waste heat boilers: one is used to recover the exhaust gas emitted by ordinary boilers, such as fuel fired and gas-fired boilers, biomass fired boilers, etc. The temperature of the exhaust gas from ordinary boilers is about 600 ℃, which is not too high, Therefore, the requirements for waste heat recovery boiler are relatively low. Beijing electric steam generator The other is industrial waste heat recovery boiler, such as building materials industry, chemical industry, steel making industry, etc. The temperature of waste gas and waste heat in these industries is high, and the recovery and utilization is also very valuable. small-scale electric steam generator manufactor Henan Yuji Boiler Vessel Manufacturing Co., Ltd., founded in 2005, is located at No. 8, Jizhong Road, Xiaoji Town, Xinxiang County, Henan Province. It is a comprehensive enterprise of boiler and pressure vessel, mainly engaged in the manufacturing of boilers and pressure vessels, with technological innovation as the core, integrating the design, manufacturing, sales, installation, transformation and maintenance of boilers and pressure vessels.
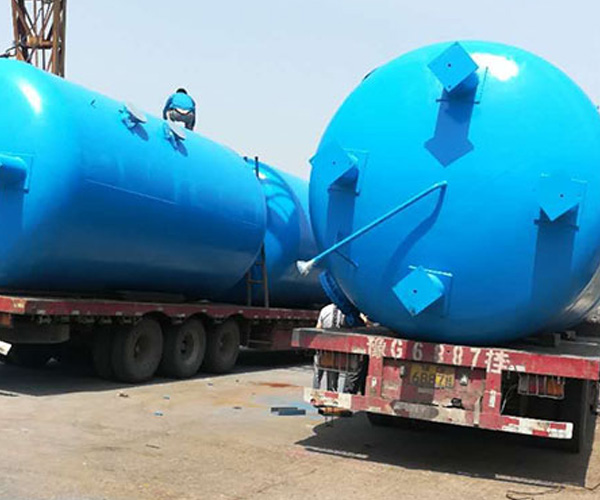
Waste heat boiler is a kind of industrial equipment. Although the equipment is simple to operate, it also needs special attention in practical application. Beijing electric steam generator So what should we pay attention to when it runs? Generally, when using waste heat boiler, we need to pay attention to prevent misfire. Due to the excessive output of the burner, the flame will disengage from the burner, resulting in incomplete combustion. A large amount of mixed gas in the furnace may cause explosion, and backfire should also be prevented. Due to the low output, the flame will retract into the burner, resulting in unstable flame flameout small-scale electric steam generator manufactor If the combustible gas continues to enter the limit, it may cause explosion. After ignition, pay attention to adjust the combustion gas flow, stabilize the burner pressure, so that the flame can burn stably. In order to reduce the smoke from the chimney and pollute the environment, smoke suppression and dust removal devices should be installed.
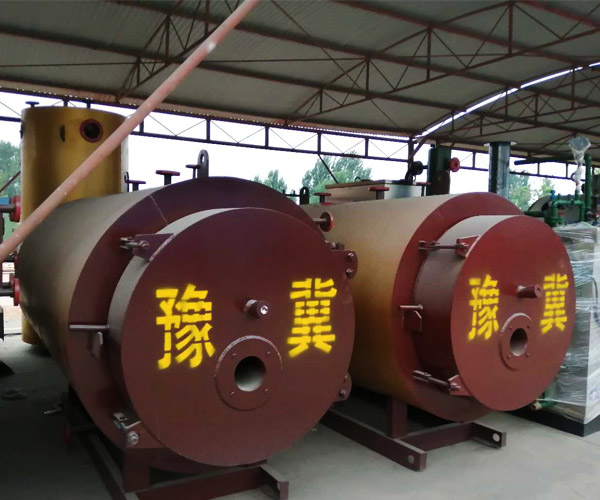
Economical and energy-saving: the new generation of biomass pellet fuel can save 30% - 60% of the operating cost compared with oil, gas and electric heating boilers. Convenient installation: this series of generators do not need to be inspected, and the tedious annual approval procedure can be avoided. Beijing electric steam generator At the same time, the machine is assembled for modules, and professional installation procedures are not required. High efficiency operation: adopt the design of multiple flue gas backflow, optimize oxygen enrichment for many times, cooperate with professional dust removal and energy saving equipment, the thermal efficiency reaches more than 90%, and can continuously produce steam. Low carbon and environmental protection: Through reasonable design, biomass fuel is semi gasified and burned, and smokeless combustion is achieved. Reliable security: It is equipped with pressure, water shortage, security valve and other protection devices to ensure stable operation and reliable security of the boiler. small-scale electric steam generator manufactor Simple operation: microcomputer intelligent one button operation, automatic feeding, automatic ignition, cycle start stop and fault alarm functions are used for simple operation. The labor intensity is greatly reduced, and the use of the boiler is more humanized. Convenient maintenance: the overall structure of the boiler is reasonable, and the installation is convenient. There is a cleaning port under each furnace. The main components have inspection ports for future maintenance and repair.
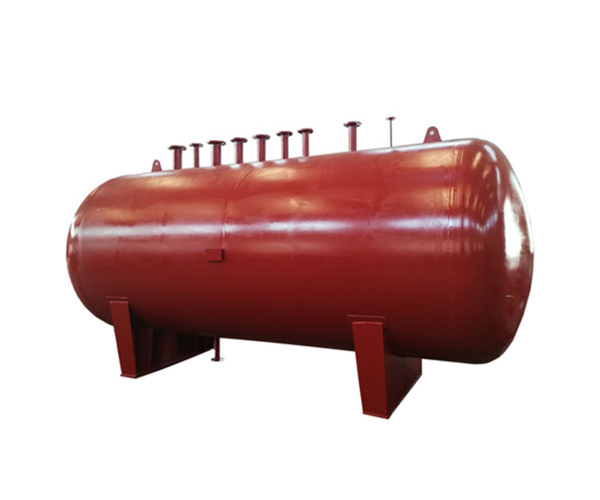
Oil gas boilers have obvious characteristics. The main fuel is oil or gas. According to their functions, they can be divided into steam boilers and hot water boilers. Most of them are designed with large furnaces, with thermal efficiency of more than 98%. At the same time, they also have the characteristics of fully automatic and safe operation. Beijing electric steam generator Generally speaking, oil and gas boilers adopt excellent boiler body design. WNS horizontal boiler adopts wet back three return structure, which can reduce the exhaust gas temperature and make the boiler thermal efficiency reach more than 90%. Therefore, the combustion efficiency is relatively high, greatly extending its service life. small-scale electric steam generator manufactor In addition, in the design of oil and gas boiler, there are often hinged front and rear smoke boxes. The maintenance method is simple. Most of them are insulated with light aluminum silicate fiber to reduce heat loss. The external use of all stainless steel plate skin improves the appearance quality. In addition, the oil and gas boiler is equipped with an excellent combustion machine, which greatly improves its stability. The combustion machine has an automatic purging function, It can also prevent deflagration during ignition.
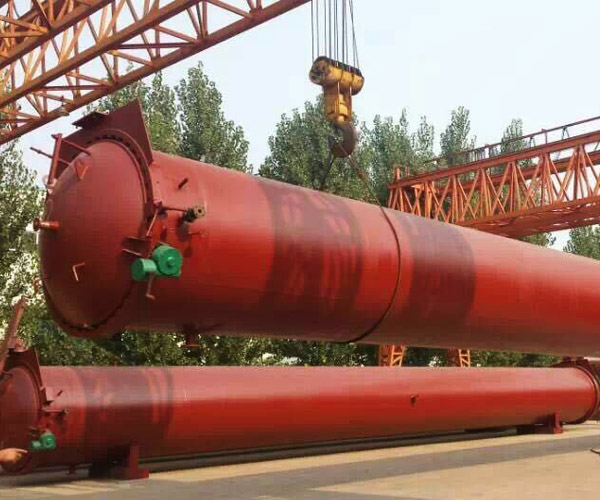
System oil drainage: drain the heat transfer oil in the system when the circulating heat transfer oil is between 120 ± 5 (if the oil is not replaced, please find a clean container for proper storage) Prepare an appropriate amount of coke removal cleaning agent for the heat transfer oil system, drain the oil in the gas-fired heat transfer oil boiler system, and disconnect the cleaning system from the oil storage tank (close the valve), including the connection between the high-level tank and the oil storage tank. Beijing electric steam generator Residual oil blowing steps: connect the air compressor at the pressure gauge or other places that can be connected, boost the system to 0.3-0.4MPa, and discharge it instantaneously; Repeat this process until the residual oil is blown out. The gas-fired heat transfer oil boiler, circulating pump, and other heat users form a cleaning circulating circuit for decoking and cleaning: add diluted cleaning agent to the system and fill it up to 1/2 of the water level of the high-level tank. Dosage of coke removal cleaning agent: 10~20%, the specific dosage shall be determined according to the scale thickness. Temperature: 90-95, time: 12-72 hours, which can be determined according to the scale thickness. Rinsing and cleaning: after cleaning, drain the residual liquid in the system and add clean water to rinse twice until the coke remover is free of foam and the water is clear. small-scale electric steam generator manufactor Temperature: 85-95, time: 5-8 hours Water blowing steps: after cleaning, connect the air compressor at the pressure gauge or other places that can be connected, use compressed air to boost the system to 0.3-0.4 MPa, and vent at each low point. Repeat this process until the water is blown out. Waste liquid treatment: the cleaning waste liquid generated in the cleaning process is discharged after being treated in the biochemical tank.