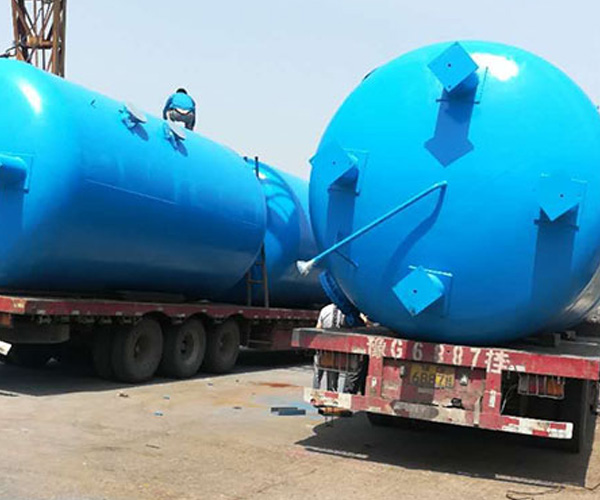
The flue gas waste heat recovery device also has the following characteristics: 1. Energy saving. It uses new heat exchange fins and heat exchange elements to make heat exchange more fully, and the exhaust gas temperature can be reduced to 40 ℃~80 ℃; The boiler efficiency can be increased by 6~15%, and the condensate drainage structure can fully recover the latent heat in the flue gas, with remarkable energy-saving effect. Gansu electric steam generator Due to the special structure, the total pressure drop is small and the power consumption is small, that is, the smoke pressure drop is small and meets the system requirements. 2. Beautiful. Due to the use of efficient heat exchange elements and reasonable structural configuration, this product has the characteristics of compact structure, small size, beautiful appearance, etc. small-scale electric steam generator factory Durable. The heat exchange tube of the flue gas waste heat recovery device is made of stainless steel aluminum fins for efficient anti-corrosion. The thermal stress, anti-corrosion performance and strength are fully considered when the equipment is manufactured, which can ensure the safety, reliability and stability of the equipment, with a service life of more than 25 years.
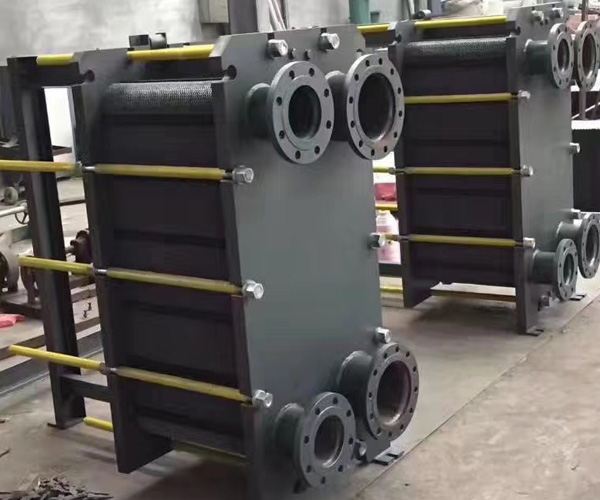
The main parts of the waste heat boiler can be divided into drum, pipe, header, membrane wall, tube panel, tube box, etc. These parts are the parts with specific process requirements in the waste heat boiler. Gansu electric steam generator For example, the drum should go through metal flaw detection, heat treatment, hydrostatic test and other processes to improve the stability of the waste heat boiler. At the same time, because the header needs high sealing, manual welding is required, and the welding quality needs to be tested. It can be seen that due to the complexity of the working environment of the waste heat boiler, it has special requirements for its internal structural members. small-scale electric steam generator factory In the process of designing and manufacturing the waste heat boiler, the process designer should consider the advantages and disadvantages of various processes, and then select a reasonable process to complete the manufacturing of the waste heat boiler. For example, the serpentine parts in the waste heat boiler cannot be bent automatically by the machine, so they can only be bent manually.
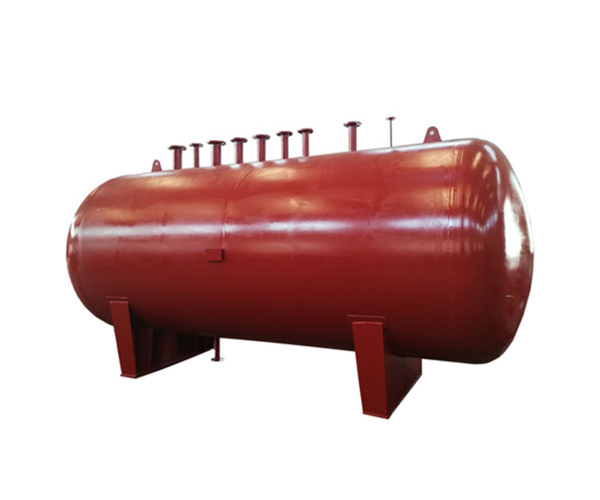
The furnace liner is the combustion chamber of the horizontal gas-fired heat transfer oil furnace. The burner nozzle is placed in the front of the furnace liner, and the high-temperature flue gas generated by combustion extends to the rear, leaving the furnace liner and returning to the space. Generally, the number of times of returning is not more than four, and the common one is the three return heat conduction oil furnace. Gansu electric steam generator This type of heat transfer oil furnace can be divided into dry back type heat transfer oil furnace and full wet back type heat transfer oil furnace according to the structure of the flue gas reentry space at the rear of the furnace. The flue gas reentry space of the dry back heat conduction oil furnace is enclosed by refractory materials; The flue gas reentry space of the full wet back type heat conduction oil furnace is composed of a recuperative chamber immersed in water. In addition, there is a central regenerative heat conduction oil furnace: that is, the back wall of the furnace liner is sealed inside the boiler shell, and the flue gas is turned back to the front from the inner wall around the furnace liner after encountering. This type of heat transfer oil furnace can also be regarded as a full wet back heat transfer oil furnace. small-scale electric steam generator factory Although the dry back heat transfer oil furnace is simple in structure, the refractory material at the rear of the furnace liner is easily damaged, and the rear tube plate is often directly washed by high temperature flue gas. The temperature difference is large, so the dry back heat transfer oil furnace is obsolete. At present, few manufacturers produce it; Although the full wet back heat conduction oil furnace has a complex structure, it avoids the problem of flue gas sealing in the reentry space and is suitable for micro positive pressure combustion.
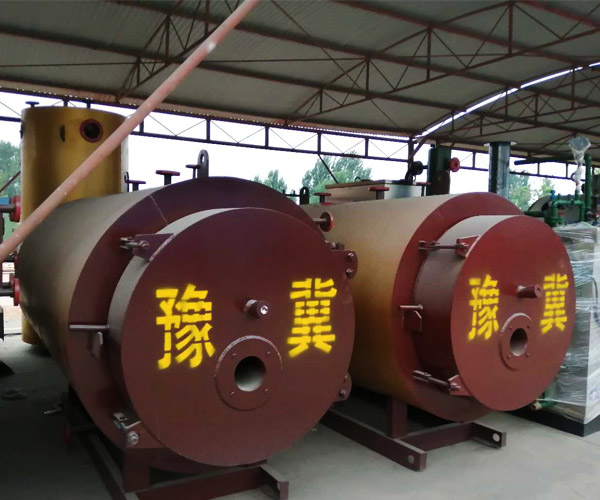
The steam used in the steam generator of the hotel laundry is usually 0.4~0.6MPa saturated steam. The working temperature of steam is not very high. Gansu electric steam generator The steam boiler of the hotel requires high steam efficiency due to operating costs, so it can save operating costs. The area of the hotel is relatively limited, so the steam boiler with small floor area must be selected. In order to control the investment cost and heat loss of the steam pipe, the steam boiler is usually placed on the side of the laundry room. small-scale electric steam generator factory The steam equipment in the hotel laundry room can only be turned on when washing, not when washing. Therefore, the steam generator is required to start steam production quickly. Laundry equipment is sometimes opened a lot and sometimes less, so the steam boiler is required to adjust the steam volume within the specified range.