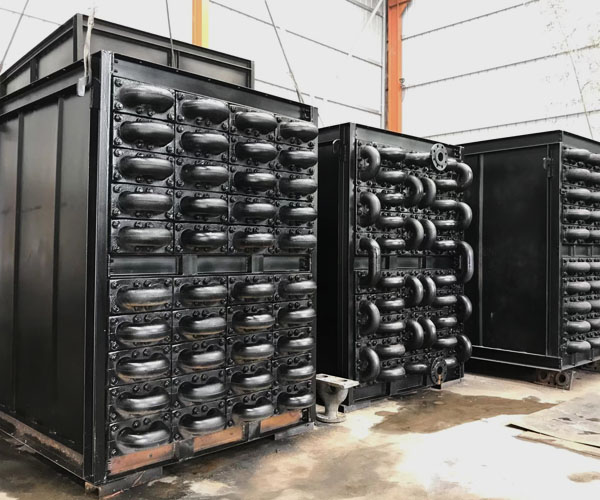
The main parts of the waste heat boiler can be divided into drum, pipe, header, membrane wall, tube panel, tube box, etc. These parts are the parts with specific process requirements in the waste heat boiler. Guangdong Natural gas steam generator For example, the drum should go through metal flaw detection, heat treatment, hydrostatic test and other processes to improve the stability of the waste heat boiler. At the same time, because the header needs high sealing, manual welding is required, and the welding quality needs to be tested. It can be seen that due to the complexity of the working environment of the waste heat boiler, it has special requirements for its internal structural members. small-scale Natural gas steam generator manufactor In the process of designing and manufacturing the waste heat boiler, the process designer should consider the advantages and disadvantages of various processes, and then select a reasonable process to complete the manufacturing of the waste heat boiler. For example, the serpentine parts in the waste heat boiler cannot be bent automatically by the machine, so they can only be bent manually.
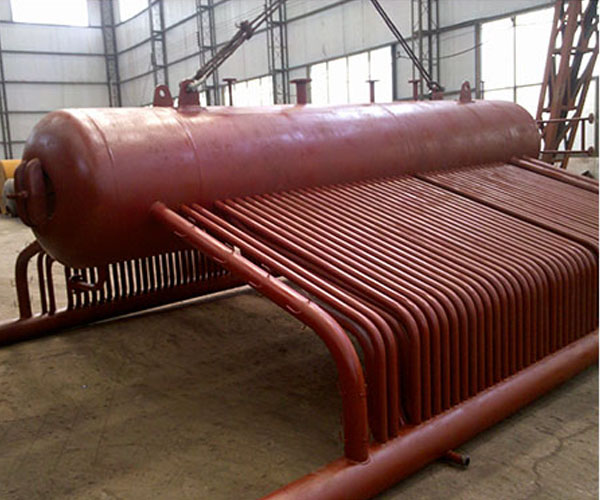
Oil gas boilers have obvious characteristics. The main fuel is oil or gas. According to their functions, they can be divided into steam boilers and hot water boilers. Most of them are designed with large furnaces, with thermal efficiency of more than 98%. At the same time, they also have the characteristics of fully automatic and safe operation. Guangdong Natural gas steam generator Generally speaking, oil and gas boilers adopt excellent boiler body design. WNS horizontal boiler adopts wet back three return structure, which can reduce the exhaust gas temperature and make the boiler thermal efficiency reach more than 90%. Therefore, the combustion efficiency is relatively high, greatly extending its service life. small-scale Natural gas steam generator manufactor In addition, in the design of oil and gas boiler, there are often hinged front and rear smoke boxes. The maintenance method is simple. Most of them are insulated with light aluminum silicate fiber to reduce heat loss. The external use of all stainless steel plate skin improves the appearance quality. In addition, the oil and gas boiler is equipped with an excellent combustion machine, which greatly improves its stability. The combustion machine has an automatic purging function, It can also prevent deflagration during ignition.
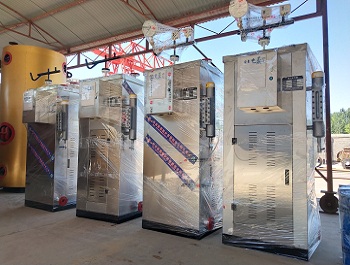
The waste heat recovery of flue gas can not only be used for heating or power generation to achieve energy-saving effect, but also can be beneficial to environmental protection and achieve dual effects of energy conservation and environmental protection. Guangdong Natural gas steam generator In general, the important equipment of waste heat power generation is waste heat boiler, which mainly uses heat or combustible substances in waste gas, waste liquid and other working medium as heat source, and produces steam mainly for power generation. There are many ways to recover waste heat from flue gas of waste heat boiler. Generally, comprehensive utilization of waste heat is followed by direct utilization and indirect utilization. small-scale Natural gas steam generator manufactor Generally speaking, if heat sources are needed in the process, the waste heat utilization is mainly comprehensive utilization. First, the heat source is recovered and fed back to the process for reuse. If there is any surplus, it can be used for power generation or as the heat source for central heating; If there is no surplus, it will be directly used instead of being used for power generation; If the process does not need more heat sources, then indirect use, mainly power generation or public heating.
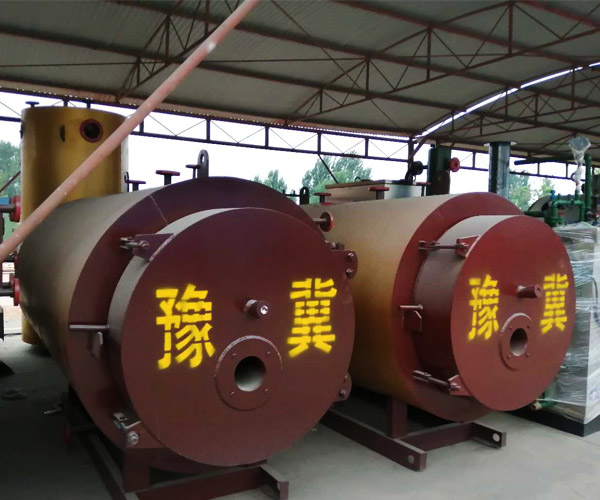
The fluctuation of waste heat boiler flue gas in flow, temperature, composition, dust content and other aspects is one of its characteristics. The nature of the fluctuation can be regular, periodic, or irregular, aperiodic; The characteristics of fluctuation can be gradual. Guangdong Natural gas steam generator It can also be impulsive; It can be a single parameter or a composite fluctuation of multiple parameters. The selection of waste heat boiler shall first analyze the whole cycle of the main process flow, and determine the flue gas characteristics of each time section in the cycle. small-scale Natural gas steam generator manufactor Therefore, corresponding measures shall be implemented one by one in the design of waste heat boiler. The prominent feature is often the main basis for the selection of waste heat boiler.
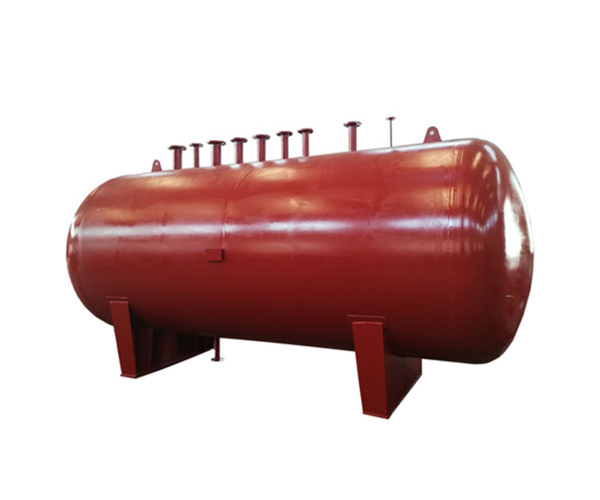
System oil drainage: drain the heat transfer oil in the system when the circulating heat transfer oil is between 120 ± 5 (if the oil is not replaced, please find a clean container for proper storage) Prepare an appropriate amount of coke removal cleaning agent for the heat transfer oil system, drain the oil in the gas-fired heat transfer oil boiler system, and disconnect the cleaning system from the oil storage tank (close the valve), including the connection between the high-level tank and the oil storage tank. Guangdong Natural gas steam generator Residual oil blowing steps: connect the air compressor at the pressure gauge or other places that can be connected, boost the system to 0.3-0.4MPa, and discharge it instantaneously; Repeat this process until the residual oil is blown out. The gas-fired heat transfer oil boiler, circulating pump, and other heat users form a cleaning circulating circuit for decoking and cleaning: add diluted cleaning agent to the system and fill it up to 1/2 of the water level of the high-level tank. Dosage of coke removal cleaning agent: 10~20%, the specific dosage shall be determined according to the scale thickness. Temperature: 90-95, time: 12-72 hours, which can be determined according to the scale thickness. Rinsing and cleaning: after cleaning, drain the residual liquid in the system and add clean water to rinse twice until the coke remover is free of foam and the water is clear. small-scale Natural gas steam generator manufactor Temperature: 85-95, time: 5-8 hours Water blowing steps: after cleaning, connect the air compressor at the pressure gauge or other places that can be connected, use compressed air to boost the system to 0.3-0.4 MPa, and vent at each low point. Repeat this process until the water is blown out. Waste liquid treatment: the cleaning waste liquid generated in the cleaning process is discharged after being treated in the biochemical tank.