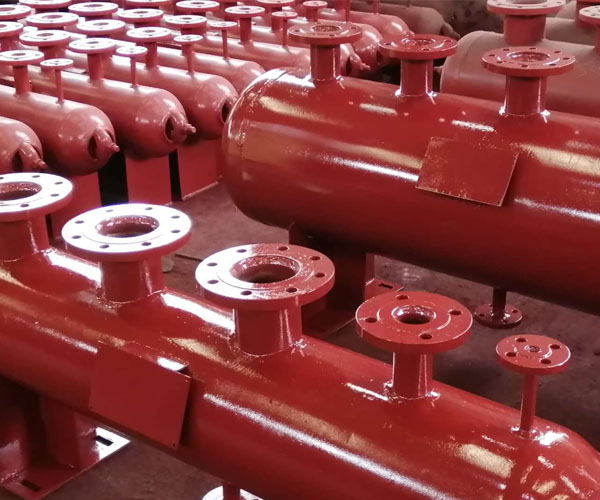
In daily life, pressure vessels are divided into those in contact with fire sources and those not in contact with fire sources. In fact, pressure vessels also need anti-corrosion in daily life. For the anti-corrosion of pressure vessels, we need to do the following. Gansu Fuel gas steam generator First, check the structure of its equipment components, safety valves, bursting discs, emergency vent valves and other collective Yixing pressure tanks to see if there is any corrosion. Once corrosion occurs, measures should be taken in a timely manner. Anti rust paint should be painted before the equipment is used. After use, it should be cleaned in a timely manner to ensure the cleanliness of the equipment. vertical Fuel gas steam generator manufactor Secondly, it is necessary to protect the safety device of the pressure vessel. The safety device is an important device of the pressure vessel. Good protection should be carried out. Good maintenance should be carried out before and after use. It is necessary to apply lubricating oil and antirust paint.
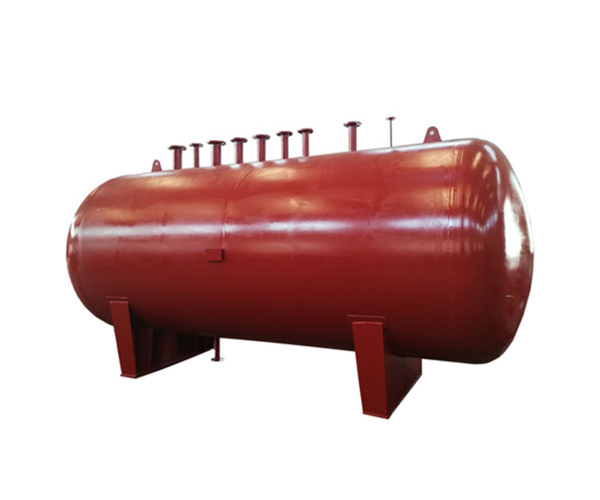
The steam used in the steam generator of the hotel laundry is usually 0.4~0.6MPa saturated steam. The working temperature of steam is not very high. Gansu Fuel gas steam generator The steam boiler of the hotel requires high steam efficiency due to operating costs, so it can save operating costs. The area of the hotel is relatively limited, so the steam boiler with small floor area must be selected. In order to control the investment cost and heat loss of the steam pipe, the steam boiler is usually placed on the side of the laundry room. vertical Fuel gas steam generator manufactor The steam equipment in the hotel laundry room can only be turned on when washing, not when washing. Therefore, the steam generator is required to start steam production quickly. Laundry equipment is sometimes opened a lot and sometimes less, so the steam boiler is required to adjust the steam volume within the specified range.
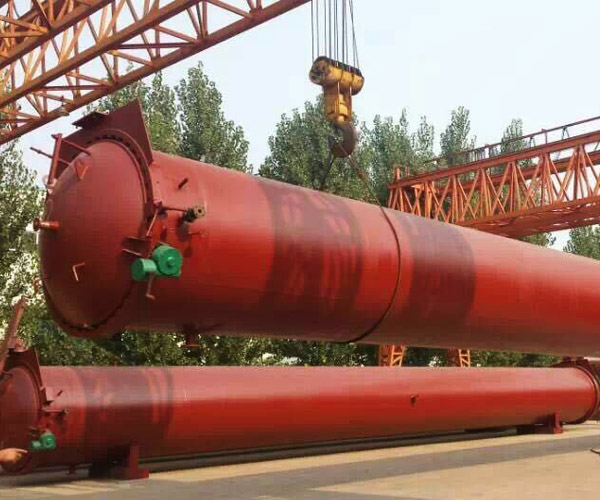
System oil drainage: drain the heat transfer oil in the system when the circulating heat transfer oil is between 120 ± 5 (if the oil is not replaced, please find a clean container for proper storage) Prepare an appropriate amount of coke removal cleaning agent for the heat transfer oil system, drain the oil in the gas-fired heat transfer oil boiler system, and disconnect the cleaning system from the oil storage tank (close the valve), including the connection between the high-level tank and the oil storage tank. Gansu Fuel gas steam generator Residual oil blowing steps: connect the air compressor at the pressure gauge or other places that can be connected, boost the system to 0.3-0.4MPa, and discharge it instantaneously; Repeat this process until the residual oil is blown out. The gas-fired heat transfer oil boiler, circulating pump, and other heat users form a cleaning circulating circuit for decoking and cleaning: add diluted cleaning agent to the system and fill it up to 1/2 of the water level of the high-level tank. Dosage of coke removal cleaning agent: 10~20%, the specific dosage shall be determined according to the scale thickness. Temperature: 90-95, time: 12-72 hours, which can be determined according to the scale thickness. Rinsing and cleaning: after cleaning, drain the residual liquid in the system and add clean water to rinse twice until the coke remover is free of foam and the water is clear. vertical Fuel gas steam generator manufactor Temperature: 85-95, time: 5-8 hours Water blowing steps: after cleaning, connect the air compressor at the pressure gauge or other places that can be connected, use compressed air to boost the system to 0.3-0.4 MPa, and vent at each low point. Repeat this process until the water is blown out. Waste liquid treatment: the cleaning waste liquid generated in the cleaning process is discharged after being treated in the biochemical tank.
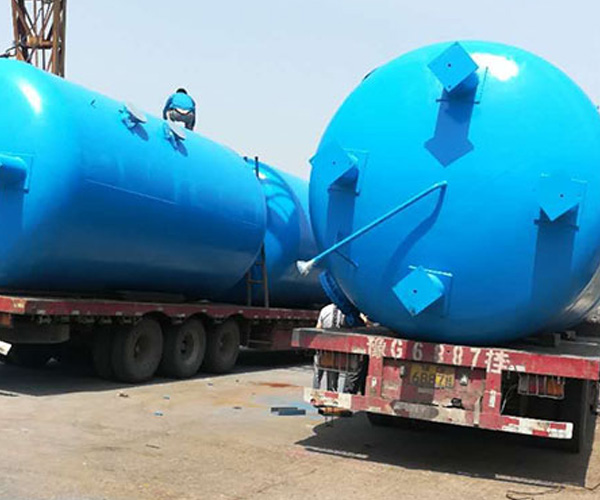
Most people may already know something about flue gas waste heat recovery, because they have already explained a lot about it. In order to let you know the relevant knowledge of flue gas waste heat recovery, the following is a brief introduction to the two methods commonly used for recovery. Gansu Fuel gas steam generator Two methods are usually adopted for flue gas waste heat recovery: one is to preheat the workpiece; The other is to preheat air for combustion support. The flue gas preheating workpiece needs to occupy a large volume for heat exchange, which is often limited by the operation site (this method cannot be used for furnaces that are used intermittently). vertical Fuel gas steam generator manufactor Preheating air for combustion support is a good method. It is generally configured on the heating furnace, which can also strengthen combustion, speed up the temperature rise of the furnace, and improve the thermal performance of the furnace. This can not only meet the requirements of the process, but also achieve significant comprehensive energy-saving effect.
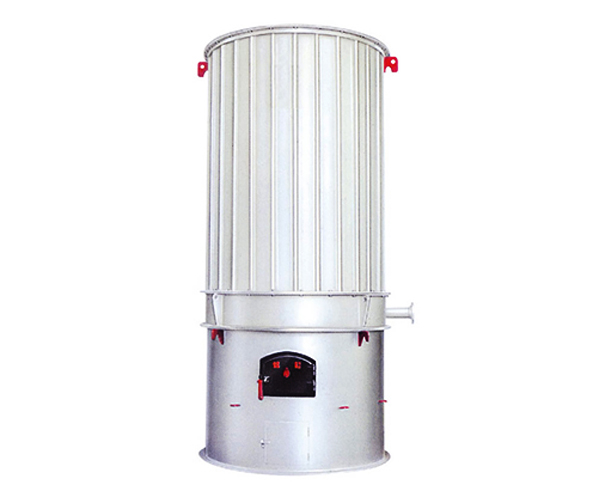
Economical and energy-saving: the new generation of biomass pellet fuel can save 30% - 60% of the operating cost compared with oil, gas and electric heating boilers. Convenient installation: this series of generators do not need to be inspected, and the tedious annual approval procedure can be avoided. Gansu Fuel gas steam generator At the same time, the machine is assembled for modules, and professional installation procedures are not required. High efficiency operation: adopt the design of multiple flue gas backflow, optimize oxygen enrichment for many times, cooperate with professional dust removal and energy saving equipment, the thermal efficiency reaches more than 90%, and can continuously produce steam. Low carbon and environmental protection: Through reasonable design, biomass fuel is semi gasified and burned, and smokeless combustion is achieved. Reliable security: It is equipped with pressure, water shortage, security valve and other protection devices to ensure stable operation and reliable security of the boiler. vertical Fuel gas steam generator manufactor Simple operation: microcomputer intelligent one button operation, automatic feeding, automatic ignition, cycle start stop and fault alarm functions are used for simple operation. The labor intensity is greatly reduced, and the use of the boiler is more humanized. Convenient maintenance: the overall structure of the boiler is reasonable, and the installation is convenient. There is a cleaning port under each furnace. The main components have inspection ports for future maintenance and repair.
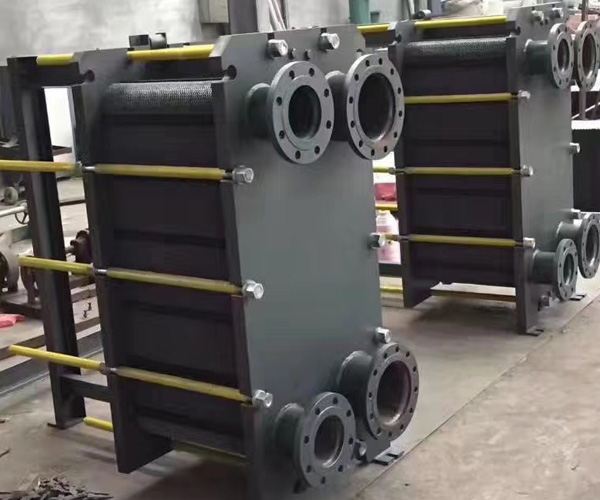
The furnace liner is the combustion chamber of the horizontal gas-fired heat transfer oil furnace. The burner nozzle is placed in the front of the furnace liner, and the high-temperature flue gas generated by combustion extends to the rear, leaving the furnace liner and returning to the space. Generally, the number of times of returning is not more than four, and the common one is the three return heat conduction oil furnace. Gansu Fuel gas steam generator This type of heat transfer oil furnace can be divided into dry back type heat transfer oil furnace and full wet back type heat transfer oil furnace according to the structure of the flue gas reentry space at the rear of the furnace. The flue gas reentry space of the dry back heat conduction oil furnace is enclosed by refractory materials; The flue gas reentry space of the full wet back type heat conduction oil furnace is composed of a recuperative chamber immersed in water. In addition, there is a central regenerative heat conduction oil furnace: that is, the back wall of the furnace liner is sealed inside the boiler shell, and the flue gas is turned back to the front from the inner wall around the furnace liner after encountering. This type of heat transfer oil furnace can also be regarded as a full wet back heat transfer oil furnace. vertical Fuel gas steam generator manufactor Although the dry back heat transfer oil furnace is simple in structure, the refractory material at the rear of the furnace liner is easily damaged, and the rear tube plate is often directly washed by high temperature flue gas. The temperature difference is large, so the dry back heat transfer oil furnace is obsolete. At present, few manufacturers produce it; Although the full wet back heat conduction oil furnace has a complex structure, it avoids the problem of flue gas sealing in the reentry space and is suitable for micro positive pressure combustion.