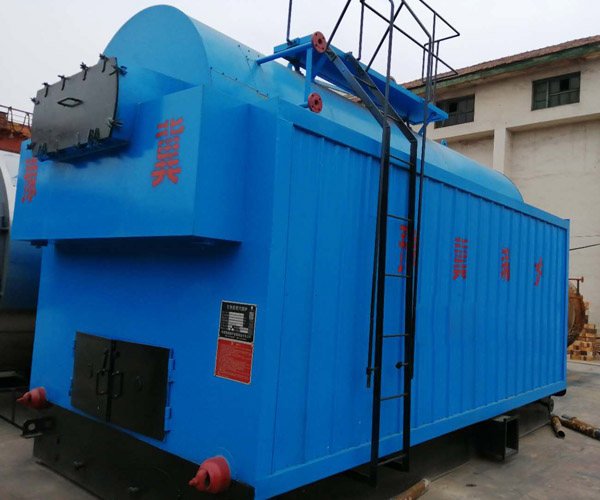
Enterprises that rely on coal for power generation are both traditional power enterprises and highly polluting enterprises. The industrial waste gas discharged by coal power generation enterprises has seriously polluted our living environment. Gansu Waste heat boiler As a result, the country has become more and more strict in the control of this industry, and how to use waste heat recycling power generation has become a topic of concern for many enterprises. Waste heat boiler can meet this demand of enterprises, so its application in coal mine power generation enterprises is more and more. vertical Waste heat boiler factory Installing a waste heat recovery boiler on the exhaust pipe of the coal mine gas generator set, using the waste heat discharged by the coal mine gas generator set to generate steam for power generation, can not only turn waste into treasure to realize the secondary utilization of energy, achieve the goal of combining coal mine gas control with energy conservation and emission reduction, but also reduce environmental pollution, kill two birds with one stone.
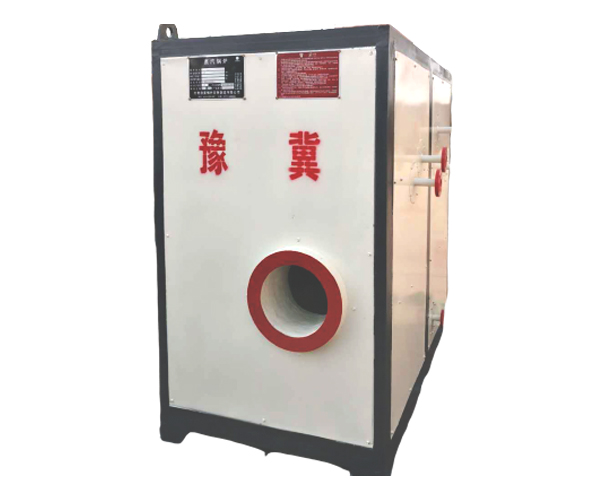
When the boiler is shut down, the temperature of the heat transfer oil can be reduced to below 70 ℃ before the shutdown of the hot oil pump. In case of sudden power failure, extinguish the fire immediately, and then implement the operating procedures. Otherwise, the furnace tube will be burned out and the loss will be large. According to the type of heat transfer oil boiler, heat transfer oil shall be reasonably selected to prevent overheating. Gansu Waste heat boiler When purchasing unqualified heat transfer oil, do not save money or mix heat transfer oil indiscriminately. Otherwise, the consequences will be very serious. Prevent the oxidation of heat transfer oil. The strict heat transfer oil is more than 50 degrees in contact with the air, which will make the heat transfer oil crack. Its speed is amazing, and the consequences are relatively serious. After normal operation, the test crew needs to close the exhaust valve on the auxiliary exhaust pipe. After 6 months of use, the heat transfer oil must be sampled and tested according to the instructions. If problems are found, the heat transfer oil must be replaced immediately. vertical Waste heat boiler factory However, it should be noted that different types of heat transfer oil should not be mixed. The circulation speed of the heat transfer oil should not be less than 1.5m/s. Due to the excessive temperature difference between some entrances and exits, the original design requirements were destroyed, the heat transfer oil could not maintain the original circulation state, the boundary layer became thicker, and the thermal resistance became larger, making the furnace wall exceed the oil film temperature, leading to carbon deposition, cracking, polymerization, coking, and even burning through the furnace tube.
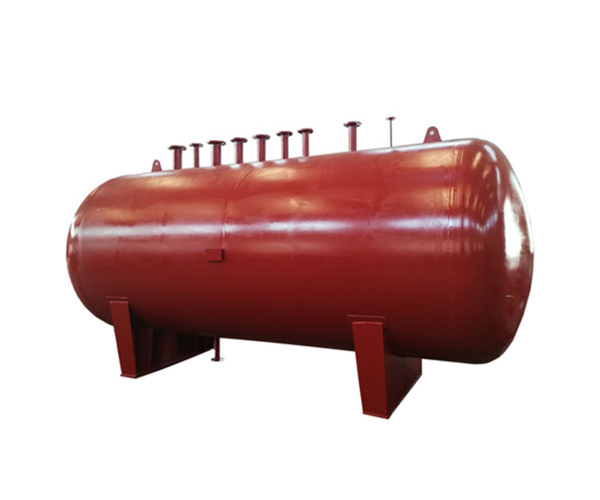
System oil drainage: drain the heat transfer oil in the system when the circulating heat transfer oil is between 120 ± 5 (if the oil is not replaced, please find a clean container for proper storage) Prepare an appropriate amount of coke removal cleaning agent for the heat transfer oil system, drain the oil in the gas-fired heat transfer oil boiler system, and disconnect the cleaning system from the oil storage tank (close the valve), including the connection between the high-level tank and the oil storage tank. Gansu Waste heat boiler Residual oil blowing steps: connect the air compressor at the pressure gauge or other places that can be connected, boost the system to 0.3-0.4MPa, and discharge it instantaneously; Repeat this process until the residual oil is blown out. The gas-fired heat transfer oil boiler, circulating pump, and other heat users form a cleaning circulating circuit for decoking and cleaning: add diluted cleaning agent to the system and fill it up to 1/2 of the water level of the high-level tank. Dosage of coke removal cleaning agent: 10~20%, the specific dosage shall be determined according to the scale thickness. Temperature: 90-95, time: 12-72 hours, which can be determined according to the scale thickness. Rinsing and cleaning: after cleaning, drain the residual liquid in the system and add clean water to rinse twice until the coke remover is free of foam and the water is clear. vertical Waste heat boiler factory Temperature: 85-95, time: 5-8 hours Water blowing steps: after cleaning, connect the air compressor at the pressure gauge or other places that can be connected, use compressed air to boost the system to 0.3-0.4 MPa, and vent at each low point. Repeat this process until the water is blown out. Waste liquid treatment: the cleaning waste liquid generated in the cleaning process is discharged after being treated in the biochemical tank.
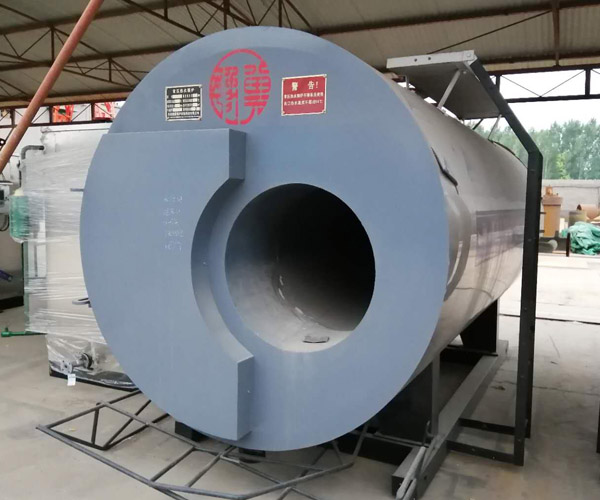
The manufacturer of the pneumatic water tank shall hold the pressure vessel manufacturing license or registration, and have a sound quality management system and system. Gansu Waste heat boiler The purchased parts of the equipment must have the product certificate and pass the entrance inspection before use. The pneumatic water tank, water pump unit, electrical components and other components of the three-dimensional elastic filler manufacturer's equipment shall be assembled and used after passing the inspection. The equipment assembled on site can be used to inspect the performance of the whole machine on site. The production license issued by the relevant department shall be held. vertical Waste heat boiler factory When selecting this product, requirements shall be put forward for the following items: equipment composition, equipment classification, equipment working pressure, equipment design flow, specification and quantity of air pressure tank, equipment data, and sanitary requirements. The overall structure of equipment, water pipe, gas pipe and electrical circuit shall be arranged reasonably, and the manufacturer of single hole mold aerator shall reserve space for device maintenance to facilitate operation. The pipeline of the equipment shall be equipped with a safety valve, and the opening pressure of the combined packing manufacturer shall not be greater than 1.1 times of the working pressure. The equipment shared by fire fighting and living (production) shall have a separate fire water outlet.
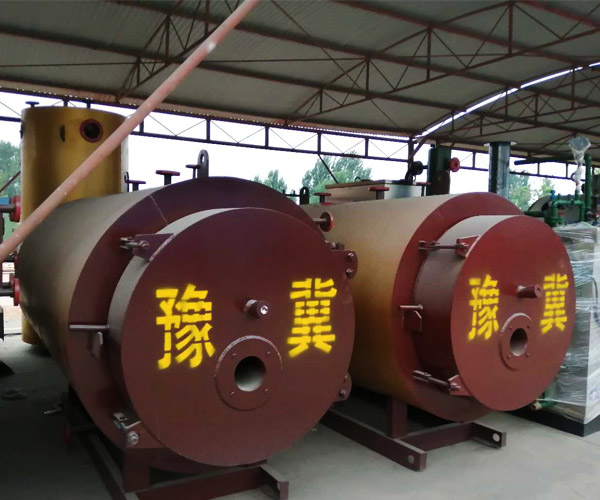
Most people may already know something about flue gas waste heat recovery, because they have already explained a lot about it. In order to let you know the relevant knowledge of flue gas waste heat recovery, the following is a brief introduction to the two methods commonly used for recovery. Gansu Waste heat boiler Two methods are usually adopted for flue gas waste heat recovery: one is to preheat the workpiece; The other is to preheat air for combustion support. The flue gas preheating workpiece needs to occupy a large volume for heat exchange, which is often limited by the operation site (this method cannot be used for furnaces that are used intermittently). vertical Waste heat boiler factory Preheating air for combustion support is a good method. It is generally configured on the heating furnace, which can also strengthen combustion, speed up the temperature rise of the furnace, and improve the thermal performance of the furnace. This can not only meet the requirements of the process, but also achieve significant comprehensive energy-saving effect.