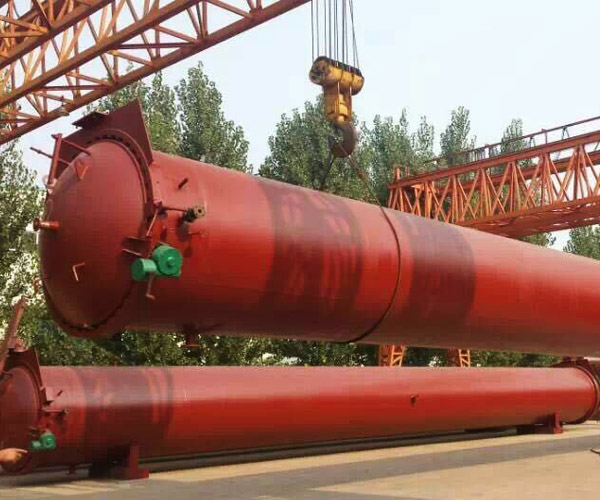
The furnace liner is the combustion chamber of the horizontal gas-fired heat transfer oil furnace. The burner nozzle is placed in the front of the furnace liner, and the high-temperature flue gas generated by combustion extends to the rear, leaving the furnace liner and returning to the space. Generally, the number of times of returning is not more than four, and the common one is the three return heat conduction oil furnace. Kunming Electrically heated steam generator This type of heat transfer oil furnace can be divided into dry back type heat transfer oil furnace and full wet back type heat transfer oil furnace according to the structure of the flue gas reentry space at the rear of the furnace. The flue gas reentry space of the dry back heat conduction oil furnace is enclosed by refractory materials; The flue gas reentry space of the full wet back type heat conduction oil furnace is composed of a recuperative chamber immersed in water. In addition, there is a central regenerative heat conduction oil furnace: that is, the back wall of the furnace liner is sealed inside the boiler shell, and the flue gas is turned back to the front from the inner wall around the furnace liner after encountering. This type of heat transfer oil furnace can also be regarded as a full wet back heat transfer oil furnace. small-scale Electrically heated steam generator factory Although the dry back heat transfer oil furnace is simple in structure, the refractory material at the rear of the furnace liner is easily damaged, and the rear tube plate is often directly washed by high temperature flue gas. The temperature difference is large, so the dry back heat transfer oil furnace is obsolete. At present, few manufacturers produce it; Although the full wet back heat conduction oil furnace has a complex structure, it avoids the problem of flue gas sealing in the reentry space and is suitable for micro positive pressure combustion.
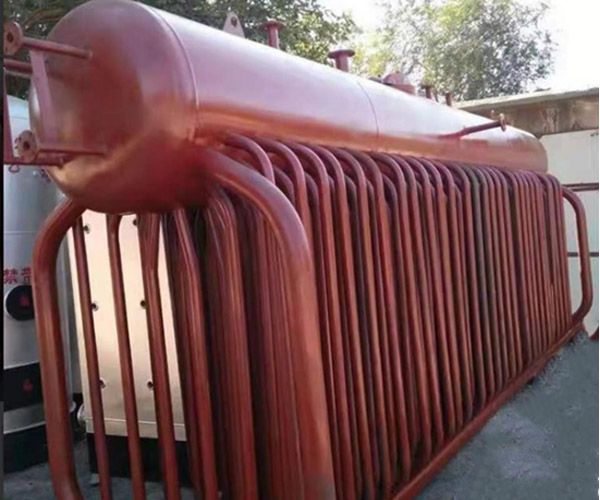
The hardness of water is mainly formed and expressed by calcium and magnesium, so cation exchange resin (water softener) is generally used to replace Ca2+and Mg2+(the main component forming scale) in the water. With the increase of Ca2+and Mg2+in the resin, the efficiency of the resin to remove Ca2+and Mg2+gradually decreases. Kunming Electrically heated steam generator When the resin absorbs a certain amount of calcium and magnesium ions, it must be regenerated. The regeneration process is to wash the resin layer with salt water in the salt tank to replace the hardness ions on the resin. With the regeneration waste liquid discharged out of the tank, the resin will resume its softening and exchange function. small-scale Electrically heated steam generator factory Since the hardness of water is mainly formed by calcium and magnesium and represents that the hardness of water is mainly formed by calcium and magnesium and represents the principle of sodium ion exchange and softening treatment, the principle is to pass raw water through sodium type cation exchange resin, so that the hardness components Ca2+and Mg2+in the water can exchange with the Na+in the resin, thereby adsorbing Ca2+ Mg2+, Soften the water.
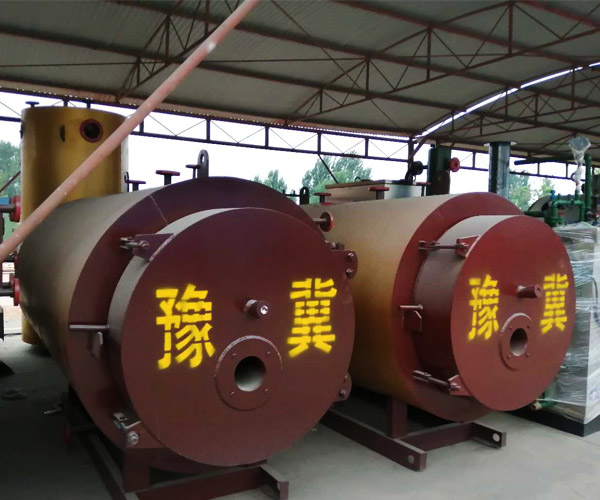
Biomass boilers can be roughly divided into two categories according to their uses: one is biomass thermal energy boiler, and the other is biomass electric energy boiler. Kunming Electrically heated steam generator In fact, the principle of the two is basically the same. Both obtain energy by burning biomass fuel, which is just one way to directly obtain heat energy. The second way is to convert heat energy into electric energy. Among the two boilers, one is widely used and has mature technology. If we continue to subdivide, one kind of boiler - biomass heat energy boiler mainly has the following two types: one is small biomass heat energy boiler. small-scale Electrically heated steam generator factory The boiler uses solidified or gasified biomass fuel to provide heat energy in the form of hot water. Its advantages are small size, simple structure and low price; Class II: medium-sized biomass heat energy boiler. Such boilers mainly use solidified biomass fuel to provide hot water or steam. Its advantages are relatively mature technology, small energy loss and strong heat supply capacity.
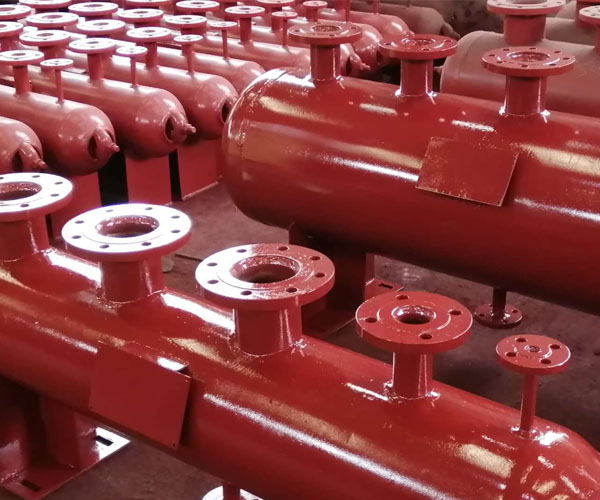
The existing industrial boiler flue gas waste heat recovery equipment mainly includes tubular heat exchanger and full heat pipe heat exchanger. Tube and tube heat exchanger can be composed of finned tube bundles. The advantage of finned tube is that it can withstand higher temperature, but has low heat transfer coefficient and large floor area. Kunming Electrically heated steam generator The flue gas of industrial boilers contains sulfur and other acidic substances. In the low temperature zone (flue gas outlet section), the temperature may be lower than the dew point of the acidic substances. The acidic substances will dew on the pipe wall, corrode the shell of the fin tube. The fin tube heat exchanger has poor operating reliability and low service life. small-scale Electrically heated steam generator factory The total heat pipe heat exchanger of boiler flue gas waste heat recovery equipment is composed of heat pipe bundles. Its shell is made of multi-layer composite materials. The heat pipe structure is complex, the cost is relatively expensive, the service life is short, and the steel consumption is large. It is difficult for users to accept it, and it is difficult to promote its application in production. The composite heat pipe heater not only takes into account the heat exchange effect, but also takes into account the economic affordability of the investors in production, which is particularly suitable for the current situation in China's industrial production.