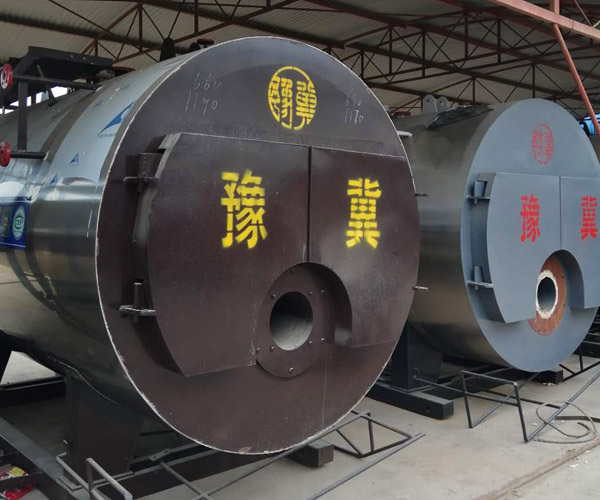
Effectively prevent and reduce low temperature corrosion of air preheater. Low temperature corrosion is caused by sulfur dioxide generated by combustion of sulfur in fuel. Beijing Automatic electric steam generator Under the action of catalyst, sulfur dioxide is further oxidized to sulfur trioxide. Sulfur trioxide and water vapor in the flue gas generate sulfuric acid vapor, which greatly increases the dew point of the flue gas, condenses the sulfuric acid vapor on the flue gas side of the preheater tube wall, causing sulfuric acid corrosion of the preheater. The content of sulfur trioxide has a great impact on the corrosion rate of the preheater. The content of sulfur trioxide is not only related to the sulfur content in the fuel, but also related to the oxygen content in the flue gas. small-scale Automatic electric steam generator factory Low oxygen combustion can significantly reduce the oxygen content in flue gas, greatly reduce the amount of sulfur dioxide oxidized to sulfur trioxide, reduce the dew point of flue gas, and effectively reduce the corrosion of preheater. Low oxygen combustion reduces the amount of flue gas. It can not only reduce the exhaust gas temperature, improve the boiler efficiency, but also reduce the power consumption of the forced draft fan and the wear of the heating surface.
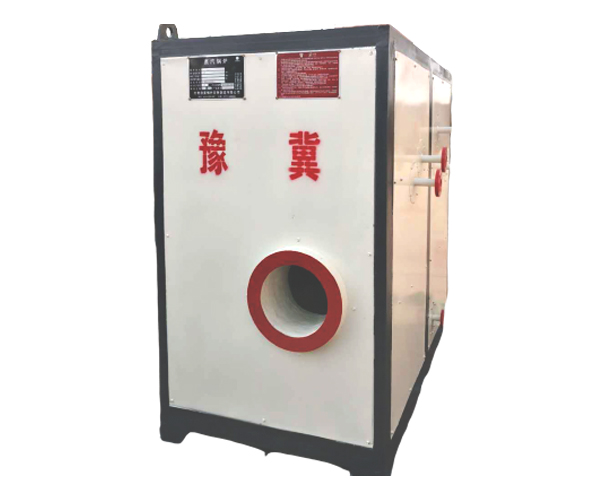
After the cold furnace of oil fired and gas fired boiler is ignited, the speed of temperature rise shall be controlled at 10 ℃/hour, mainly because the viscosity of oil temperature is large when it is cold, and the flow rate in the heating surface pipe of the whole equipment is relatively low. Beijing Automatic electric steam generator The oil film on the pipe wall is thick, so the heat transfer condition is poor when in use. If the heating speed of oil and gas fired boiler is too fast during use, it is easy to make the local oil film temperature too high. The equipment is in the stage of driving away the residual moisture and moisture contained in the heat conduction fluid in the system within the temperature range. small-scale Automatic electric steam generator factory In oil and gas fired boiler, when the steam exhaust volume at the vent pipe of the expander is relatively large, there will be water hammer at the bottom of the equipment. In this way, the vibration of the pipeline will accelerate, and when the swing amplitude of the pressure gauge pointer in each part of the equipment is large, the temperature rise will be stopped and the constant temperature state will be maintained.
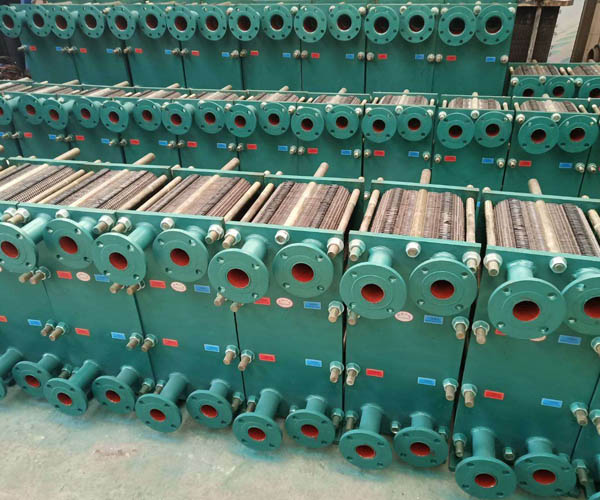
Biomass boilers can be roughly divided into two categories according to their uses: one is biomass thermal energy boiler, and the other is biomass electric energy boiler. Beijing Automatic electric steam generator In fact, the principle of the two is basically the same. Both obtain energy by burning biomass fuel, which is just one way to directly obtain heat energy. The second way is to convert heat energy into electric energy. Among the two boilers, one is widely used and has mature technology. If we continue to subdivide, one kind of boiler - biomass heat energy boiler mainly has the following two types: one is small biomass heat energy boiler. small-scale Automatic electric steam generator factory The boiler uses solidified or gasified biomass fuel to provide heat energy in the form of hot water. Its advantages are small size, simple structure and low price; Class II: medium-sized biomass heat energy boiler. Such boilers mainly use solidified biomass fuel to provide hot water or steam. Its advantages are relatively mature technology, small energy loss and strong heat supply capacity.
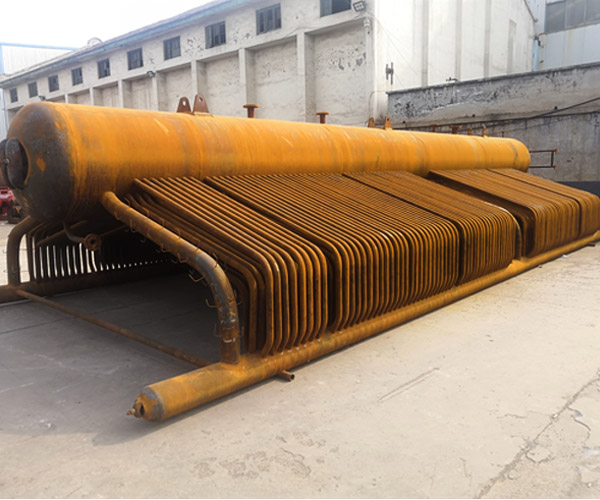
The waste heat boiler for hazardous waste incineration is an important part of the hazardous waste rotary kiln incineration system. The heat source is the high-temperature waste gas containing strongly coking and cohesive ash after hazardous waste incineration. Beijing Automatic electric steam generator Generally, this type of waste heat boiler adopts single flue or multi flue layout, and convection heating surface is arranged in the flue. During operation, strongly coking cohesive ash is easy to adhere to the convection heating surface, leading to flue blockage, affecting the safe and normal operation of the waste heat boiler. According to the characteristics of hazardous waste rotary kiln incineration system, a kind of waste heat boiler with special structure suitable for the system was developed, which successfully solved the problems of ash deposition, wear, air leakage, corrosion, etc. small-scale Automatic electric steam generator factory The water circulation mode of the waste heat boiler is natural circulation. The working medium directly enters the drum, then is led out from the drum, flows into each membrane water wall through the downcomer, is heated here, then led back to the drum through the steam conduit, and is separated by the steam water separator, and then led out of the drum saturated steam with rated parameters.
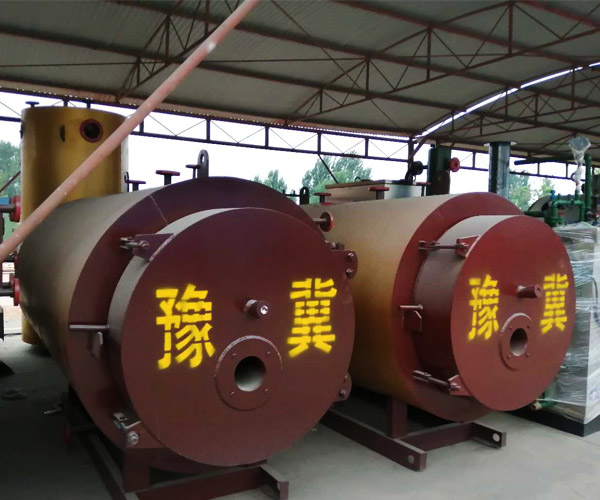
The waste heat recovery of flue gas can not only be used for heating or power generation to achieve energy-saving effect, but also can be beneficial to environmental protection and achieve dual effects of energy conservation and environmental protection. Beijing Automatic electric steam generator In general, the important equipment of waste heat power generation is waste heat boiler, which mainly uses heat or combustible substances in waste gas, waste liquid and other working medium as heat source, and produces steam mainly for power generation. There are many ways to recover waste heat from flue gas of waste heat boiler. Generally, comprehensive utilization of waste heat is followed by direct utilization and indirect utilization. small-scale Automatic electric steam generator factory Generally speaking, if heat sources are needed in the process, the waste heat utilization is mainly comprehensive utilization. First, the heat source is recovered and fed back to the process for reuse. If there is any surplus, it can be used for power generation or as the heat source for central heating; If there is no surplus, it will be directly used instead of being used for power generation; If the process does not need more heat sources, then indirect use, mainly power generation or public heating.