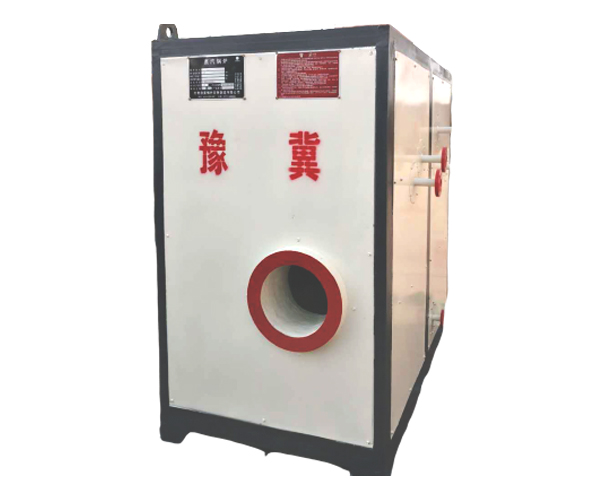
The furnace liner is the combustion chamber of the horizontal gas-fired heat transfer oil furnace. The burner nozzle is placed in the front of the furnace liner, and the high-temperature flue gas generated by combustion extends to the rear, leaving the furnace liner and returning to the space. Generally, the number of times of returning is not more than four, and the common one is the three return heat conduction oil furnace. Henan Horizontal fuel gas steam generator This type of heat transfer oil furnace can be divided into dry back type heat transfer oil furnace and full wet back type heat transfer oil furnace according to the structure of the flue gas reentry space at the rear of the furnace. The flue gas reentry space of the dry back heat conduction oil furnace is enclosed by refractory materials; The flue gas reentry space of the full wet back type heat conduction oil furnace is composed of a recuperative chamber immersed in water. In addition, there is a central regenerative heat conduction oil furnace: that is, the back wall of the furnace liner is sealed inside the boiler shell, and the flue gas is turned back to the front from the inner wall around the furnace liner after encountering. This type of heat transfer oil furnace can also be regarded as a full wet back heat transfer oil furnace. vertical Horizontal fuel gas steam generator manufactor Although the dry back heat transfer oil furnace is simple in structure, the refractory material at the rear of the furnace liner is easily damaged, and the rear tube plate is often directly washed by high temperature flue gas. The temperature difference is large, so the dry back heat transfer oil furnace is obsolete. At present, few manufacturers produce it; Although the full wet back heat conduction oil furnace has a complex structure, it avoids the problem of flue gas sealing in the reentry space and is suitable for micro positive pressure combustion.
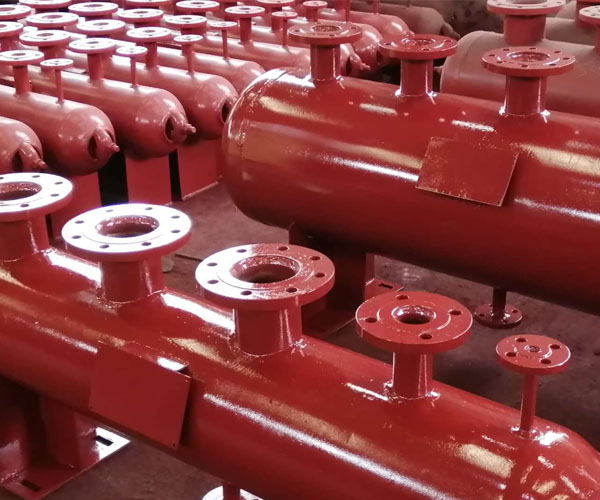
The boiler adopts the combustion equipment suitable for the combustion of biomass fuel - reciprocating grate. In the structural design of the boiler, the furnace space of the boiler is larger than that of the traditional boiler, and the reasonable arrangement of the secondary air is conducive to the full combustion of a large amount of volatile matter released instantaneously during the combustion of biomass fuel. The boiler can be equipped with oil (gas) ignition burner to realize ignition automation. Henan Horizontal fuel gas steam generator The feeding, combustion, slag removal, water supply and ignition of the boiler can be automatically controlled, and the operation is convenient. The boiler is equipped with an automatic ash cleaning device, which can remove the ash on the heating surface of the boiler in time to ensure the efficient and stable operation of the boiler. The tail of the boiler is equipped with an economizer, or an air preheater according to the user's needs. Compared with the traditional boiler, the boiler has higher efficiency and lower exhaust gas temperature. High efficiency thermal insulation materials are used, the boiler surface temperature is low, and the heat dissipation loss can be ignored. vertical Horizontal fuel gas steam generator manufactor All pressure parts are made of excellent boiler steel in strict accordance with Chinese national codes and standards. Each boiler shall be strictly inspected and tested before leaving the factory, including hydrostatic test and X-ray inspection. Manholes, inspection doors, fire observation holes, etc. are set to facilitate maintenance. The major characteristics of biomass boiler are: energy conservation, environmental protection, and easy installation and use.
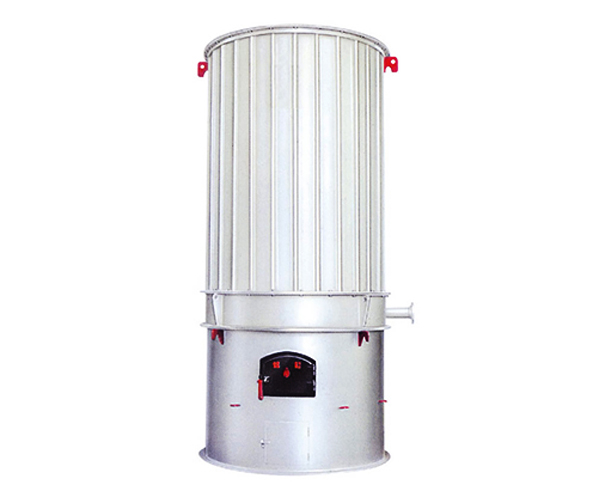
When using stainless steel storage tank, cracks appear on the head. If it is not handled in time, it will be dangerous, and how to handle this situation will be explained. Henan Horizontal fuel gas steam generator Firstly, the cracks in the stainless steel tank can were removed by polishing. After grinding, pits that do not need repair welding and do not affect the grading shall be formed within the allowable range. Otherwise, repair welding shall be carried out. The position of surface crack defect shall be determined by surface penetration defect detection, and the welding repair shall be completed. The horizontal gas tank shall be repaired, and the weld and surrounding materials shall be repaired. After that, argon tungsten arc welding shall be used for repair welding. vertical Horizontal fuel gas steam generator manufactor Tungsten argon arc welding shall be adopted for welding repair. It is suitable for back welding or skip welding, small size multi-layer and multi pass non rotating welding to avoid overheating of the weld. Water cooling measures are adopted. The defects of stainless steel storage tanks shall be removed by grinding with angular grinding wheel with conical grinding rod. Note that the abrasive grains of the grinding wheel should be perpendicular to the crack length. If the defect is deep, crack stop holes shall be drilled at both ends of the defect to prevent the crack from expanding with the grinding process. According to the inspection, in the stainless steel storage tank with primary side inspection, there are cracks at the head welds, and these defective welds have different edge bite degrees. Do not panic when the stainless steel tank can has cracks. The oil tank works. The above measures can be taken to solve this problem.
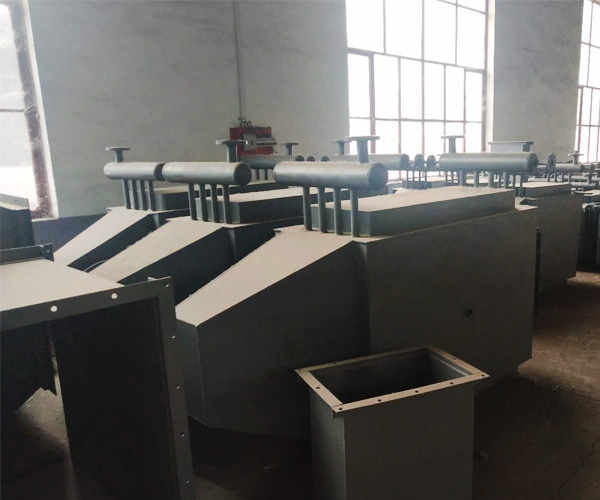
In the chemical industry, the electric heating heat conduction oil furnace is used for distillation, evaporation, polymerization, condensation, steel gate, fatliquoring, monotony, melting, dehydrogenation, forced heat preservation, and the heating of equipment composed of pesticides, intermediates, antioxidants, surfactants, spices, etc. Henan Horizontal fuel gas steam generator In the plastic and rubber industries, the electric heating heat conduction oil furnace should be used for heating and insulation of hot pressing, hot rolling, kneading, kneading, internal mixing, vulcanization molding, jet injection molding machine, slurry mixer, conveyor belt dryer, screw kneading machine and mold. In metallurgy, machining and casting industries, electric heating heat conduction oil furnaces are used to heat metal degreasing tanks, dewar tanks, electric gate valves, cleaning tanks, electroplating tanks, aluminum plate oxidation tanks, electrode manufacturing, shower heat treatment equipment, phosphate treatment equipment, baking machine rooms, sand core drying, varnish spraying and monotonous equipment. vertical Horizontal fuel gas steam generator manufactor In the food industry, the electric heating heat conduction oil furnace should be used for bread baking equipment, biscuit food baking equipment, candy production equipment, grain monotone equipment, cooking oil pressing and refining equipment, distillation pot, autoclave, conveyor belt dryer electric heater equipment.
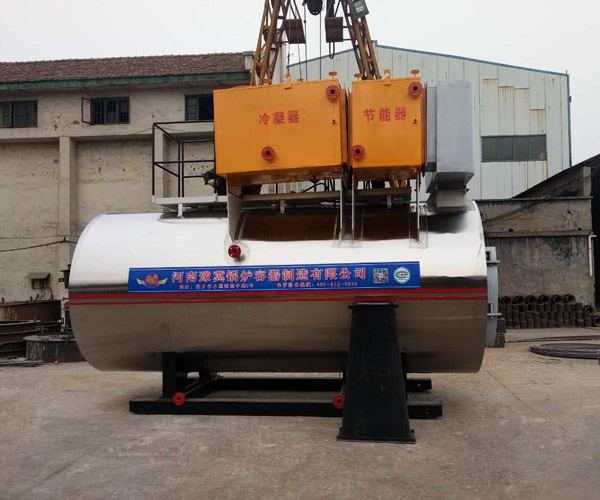
The starting of gas-fired boiler shall be carried out according to the operating procedures. The following is the accurate starting process of the analyzed gas-fired boiler: turn on the main power supply, start the gas-fired incinerator, and close the vent valve on the drum when it emits steam. Henan Horizontal fuel gas steam generator Check the manhole, handhole flange and valve of the gas boiler. If any leakage is found, fasten them. If leakage occurs after fastening, shut down the boiler for maintenance. When the gas pressure of the gas boiler rises by 0.05~0.1MPA, make up water, blow down, check the experimental water supply system and blow down equipment, and flush the water level gauge together. When the gas boiler pressure rises to 0.1~0.15MPA, flush the pressure gauge trap; When the gas pressure of the gas-fired boiler rises to 0.3MPA, turn the "load high fire/low fire" knob to "high fire" to strengthen incineration. When the pressure of the boiler rises to 2/3 of the operating pressure, start pipe warming and air supply, slowly open the main steam valve to prevent water hammer. vertical Horizontal fuel gas steam generator manufactor When the drain valve emits steam, close it. After all the drain valves are closed, slowly open the main gas valve to fully open, and then reverse it for half a circle. Turn the "Control of gas incinerator" knob to the automatic gear.