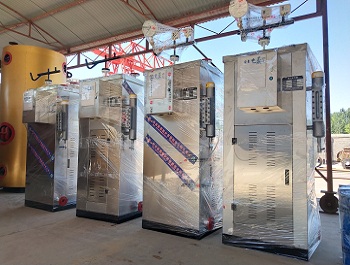
The waste heat boiler greatly improves the utilization rate of heat released by fuel combustion, so this kind of boiler saves energy; Fuel oil, gas and coal combustion generate high-temperature flue gas to release heat. The high-temperature flue gas first enters the furnace, then enters the waste heat recovery device of the front smoke box, then enters the pyrotechnic tube, and then enters the waste heat recovery device in the flue of the rear smoke box. The high-temperature flue gas turns into low-temperature flue gas and is discharged into the atmosphere through the chimney. Hunan electric steam generator Conditions conducive to quick startup of waste heat boiler: (1) The waste heat boiler adopts forced circulation, which has the priority of quick startup. (2) The flue gas baffle is hydraulically controlled, which can be used to adjust the sky in principle. The flue gas flow into the boiler is reduced. (3) The adjustable guide vane at the inlet of gas turbine can not only adjust the flue gas flow of gas turbine, but also increase or decrease the exhaust gas temperature of gas turbine through the selection of IGV temperature control mode. (4) The steam turbine bypass is designed for the rated evaporation capacity of the boiler. (5) The welded bends and headers of each heating module of the boiler are in the boiler. (6) Similar boilers in other gas turbine power plants can not be reduced when starting, and can be used to adjust the main steam pressure of the boiler. Outside the wall, contact with high-temperature smoke is avoided. vertical electric steam generator factory Operating experience of gas turbine load, such as simultaneous startup of gas turbine and waste heat boiler (flue gas damper fully open). Under the possibility of quick startup of waste heat boiler, the water level of steam drum and deaerator will lose control after the flue gas baffle is opened.
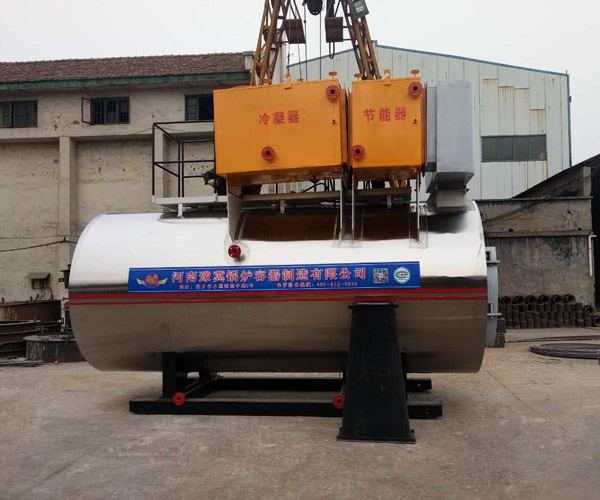
Stainless steel for pressure vessels and its welding characteristics. The so-called stainless steel refers to the addition of a certain amount of chromium in the steel to keep the steel in a passive state and free from rust. Hunan electric steam generator For this purpose, the chromium content must be more than 12%. In order to improve the passivity of steel, it is often necessary to add nickel, molybdenum and other elements that can passivate steel into stainless steel. Stainless steel is generally referred to as stainless steel and acid resistant steel. Stainless steel companies do not have certain acid resistance, and acid resistant steel generally has a good stainless property. vertical electric steam generator factory According to its steel structure, stainless steel can be divided into four categories, namely, austenitic stainless steel, ferritic stainless steel, martensitic stainless steel, and austenitic ferritic duplex stainless steel.
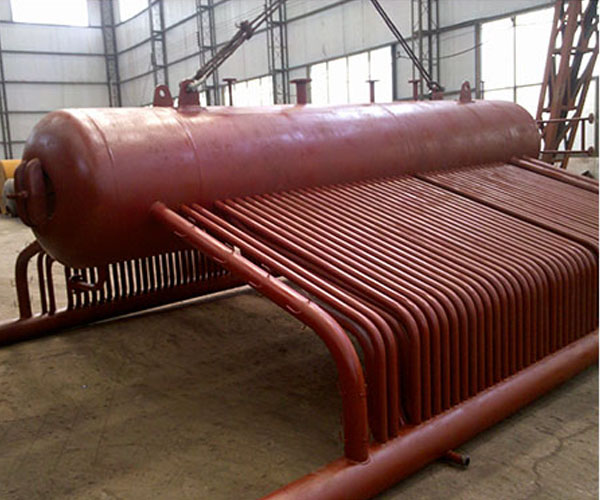
The produced waste heat boiler for hazardous waste incineration is a natural circulation water tube boiler, which adopts a single drum vertical layout and a full membrane water wall structure. Hunan electric steam generator The surrounding, top and three middle membrane water-cooled walls form a tight series of heat exchange flues. The convection heating surface is no longer arranged inside the heat exchange flue, and radiation heat exchange is adopted, so as to ensure the smooth flow of high-temperature flue gas containing strong coking adhesive ash in the heat exchange flue. Full automatic shock soot blower is arranged on the membrane water wall, and inspection holes and observation holes are reserved. vertical electric steam generator factory The bottom of the boiler is composed of membrane water walls on both sides to form a water-cooled ash bucket, and the lower part is connected with a closed spiral ash extractor. The settled soot in the waste heat boiler and the ash removed by the soot blower are discharged out of the boiler by the ash extractor. The furnace wall is of pipe laying structure, and the outside is covered with corrugated steel plate.
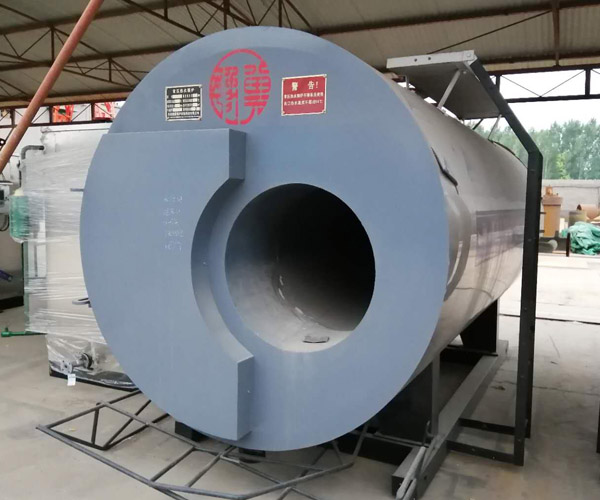
The fluctuation of waste heat boiler flue gas in flow, temperature, composition, dust content and other aspects is one of its characteristics. The nature of the fluctuation can be regular, periodic, or irregular, aperiodic; The characteristics of fluctuation can be gradual. Hunan electric steam generator It can also be impulsive; It can be a single parameter or a composite fluctuation of multiple parameters. The selection of waste heat boiler shall first analyze the whole cycle of the main process flow, and determine the flue gas characteristics of each time section in the cycle. vertical electric steam generator factory Therefore, corresponding measures shall be implemented one by one in the design of waste heat boiler. The prominent feature is often the main basis for the selection of waste heat boiler.
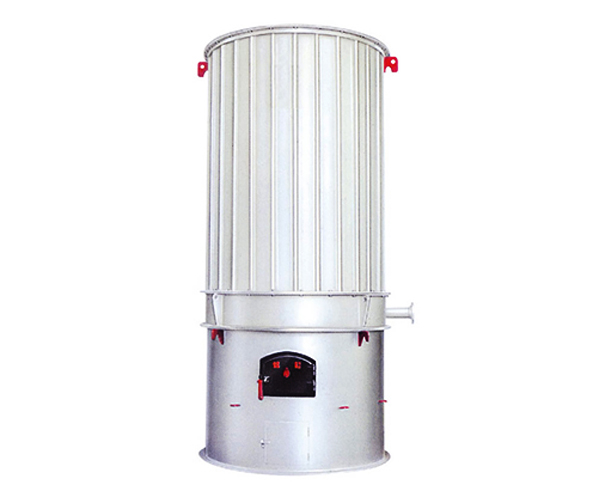
The existing industrial boiler flue gas waste heat recovery equipment mainly includes tubular heat exchanger and full heat pipe heat exchanger. Tube and tube heat exchanger can be composed of finned tube bundles. The advantage of finned tube is that it can withstand higher temperature, but has low heat transfer coefficient and large floor area. Hunan electric steam generator The flue gas of industrial boilers contains sulfur and other acidic substances. In the low temperature zone (flue gas outlet section), the temperature may be lower than the dew point of the acidic substances. The acidic substances will dew on the pipe wall, corrode the shell of the fin tube. The fin tube heat exchanger has poor operating reliability and low service life. vertical electric steam generator factory The total heat pipe heat exchanger of boiler flue gas waste heat recovery equipment is composed of heat pipe bundles. Its shell is made of multi-layer composite materials. The heat pipe structure is complex, the cost is relatively expensive, the service life is short, and the steel consumption is large. It is difficult for users to accept it, and it is difficult to promote its application in production. The composite heat pipe heater not only takes into account the heat exchange effect, but also takes into account the economic affordability of the investors in production, which is particularly suitable for the current situation in China's industrial production.
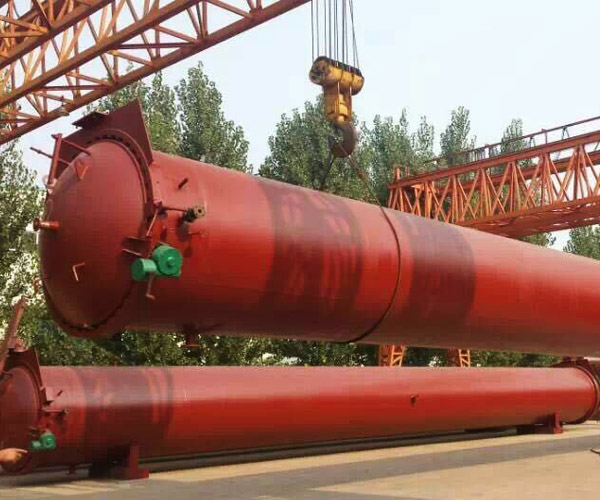
System oil drainage: circulate the heat transfer oil between 120 ± 5 to drain the heat transfer oil in the system (if you do not replace the oil, please find a clean container to store it properly). Prepare an appropriate amount of coke removal cleaning agent for the heat transfer oil system, drain the oil in the gas-fired heat transfer oil boiler system, and disconnect the cleaning system from the oil storage tank (close the valve), including the connection between the high-level tank and the oil storage tank. Hunan electric steam generator Residual oil blowing steps: connect the air compressor at the pressure gauge or other places that can be connected, boost the system to 0.3-0.4MPa, and discharge it instantaneously; Repeat this process until the residual oil is blown out. The gas-fired heat transfer oil boiler, circulating pump, and other heat users form a cleaning circulating circuit for decoking and cleaning: add diluted cleaning agent to the system and fill it up to 1/2 of the water level of the high-level tank. Dosage of coke removal cleaning agent: 10~20%, the specific dosage shall be determined according to the scale thickness. Temperature: 90-95, time: 12-72 hours, which can be determined according to the scale thickness. Rinsing and cleaning: after cleaning, drain the residual liquid in the system and add clean water to rinse twice until the coke remover is free of foam and the water is clear. vertical electric steam generator factory Temperature: 85-95, time: 5-8 hours Water blowing steps: after cleaning, connect the air compressor at the pressure gauge or other places that can be connected, use compressed air to boost the system to 0.3-0.4 MPa, and vent at each low point. Repeat this process until the water is blown out. Waste liquid treatment: the cleaning waste liquid generated in the cleaning process is discharged after being treated in the biochemical tank.