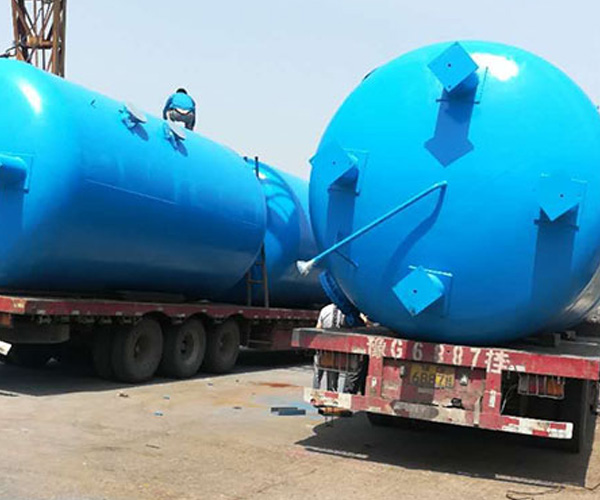
In the chemical industry, the electric heating heat conduction oil furnace is used for distillation, evaporation, polymerization, condensation, steel gate, fatliquoring, monotony, melting, dehydrogenation, forced heat preservation, and the heating of equipment composed of pesticides, intermediates, antioxidants, surfactants, spices, etc. Anhui Horizontal fuel gas steam generator In the plastic and rubber industries, the electric heating heat conduction oil furnace should be used for heating and insulation of hot pressing, hot rolling, kneading, kneading, internal mixing, vulcanization molding, jet injection molding machine, slurry mixer, conveyor belt dryer, screw kneading machine and mold. In metallurgy, machining and casting industries, electric heating heat conduction oil furnaces are used to heat metal degreasing tanks, dewar tanks, electric gate valves, cleaning tanks, electroplating tanks, aluminum plate oxidation tanks, electrode manufacturing, shower heat treatment equipment, phosphate treatment equipment, baking machine rooms, sand core drying, varnish spraying and monotonous equipment. small-scale Horizontal fuel gas steam generator factory In the food industry, the electric heating heat conduction oil furnace should be used for bread baking equipment, biscuit food baking equipment, candy production equipment, grain monotone equipment, cooking oil pressing and refining equipment, distillation pot, autoclave, conveyor belt dryer electric heater equipment.
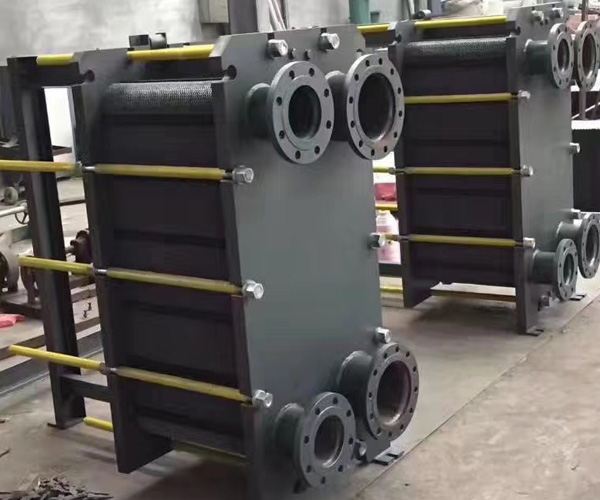
In daily life, pressure vessels are divided into those in contact with fire sources and those not in contact with fire sources. In fact, pressure vessels also need anti-corrosion in daily life. For the anti-corrosion of pressure vessels, we need to do the following. Anhui Horizontal fuel gas steam generator First, check the structure of its equipment components, safety valves, bursting discs, emergency vent valves and other collective Yixing pressure tanks to see if there is any corrosion. Once corrosion occurs, measures should be taken in a timely manner. Anti rust paint should be painted before the equipment is used. After use, it should be cleaned in a timely manner to ensure the cleanliness of the equipment. small-scale Horizontal fuel gas steam generator factory Secondly, it is necessary to protect the safety device of the pressure vessel. The safety device is an important device of the pressure vessel. Good protection should be carried out. Good maintenance should be carried out before and after use. It is necessary to apply lubricating oil and antirust paint.
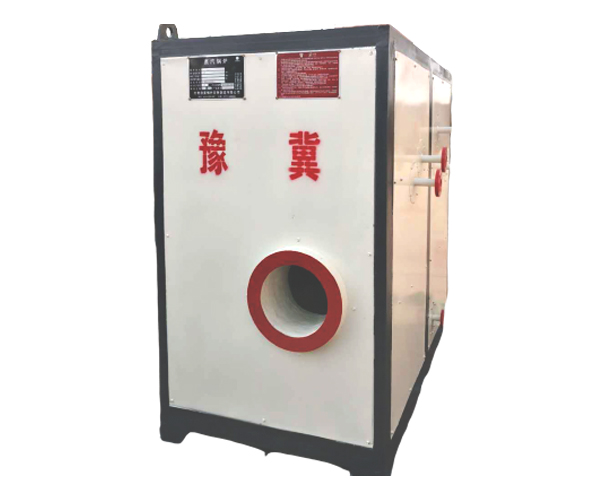
To understand the advantages and disadvantages of hot blast stove and hot water stove, we should start from the working principles of the two boilers. The hot water boiler can increase the indoor temperature by burning hot water, circulating hot water, heat dissipation, etc. General purpose (radiators, floor heating pipes, water heating air conditioners are generally used for heating in families, enterprises and institutions). Anhui Horizontal fuel gas steam generator The hot blast stove can increase the indoor temperature by heating the air. Generally, a hot channel wind belt is required. It is generally used for workshop, breeding, planting and special heating or drying. Most areas in northern China are cold, such as the three northeastern provinces, Inner Mongolia, Xinjiang and other cities. The colder temperature is more than minus 40 degrees Celsius. There are hot water boilers and steam boilers for heating. Its disadvantage is that it is afraid of circulatory system failure or power failure. small-scale Horizontal fuel gas steam generator factory Once the power failure exceeds two to three hours, if the insulation is not good, the pipeline will freeze. The heating of hot blast furnace is not frozen, and the temperature can be set. It can save 40% energy than hot water heating and 50% energy than steam boiler heating. This comparison is practical. The hot blast stove does not need to apply for a use certificate, the steam boiler and pressure hot water boiler need to apply for a use certificate, and the functional department also needs to carry out annual inspection every year, but also has to bear the cost.
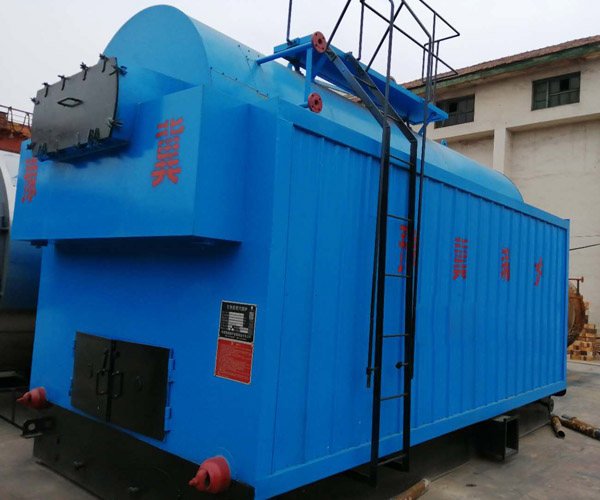
The waste heat boiler for hazardous waste incineration is an important part of the hazardous waste rotary kiln incineration system. The heat source is the high-temperature waste gas containing strongly coking and cohesive ash after hazardous waste incineration. Anhui Horizontal fuel gas steam generator Generally, this type of waste heat boiler adopts single flue or multi flue layout, and convection heating surface is arranged in the flue. During operation, strongly coking cohesive ash is easy to adhere to the convection heating surface, leading to flue blockage, affecting the safe and normal operation of the waste heat boiler. According to the characteristics of hazardous waste rotary kiln incineration system, a kind of waste heat boiler with special structure suitable for the system was developed, which successfully solved the problems of ash deposition, wear, air leakage, corrosion, etc. small-scale Horizontal fuel gas steam generator factory The water circulation mode of the waste heat boiler is natural circulation. The working medium directly enters the drum, then is led out from the drum, flows into each membrane water wall through the downcomer, is heated here, then led back to the drum through the steam conduit, and is separated by the steam water separator, and then led out of the drum saturated steam with rated parameters.
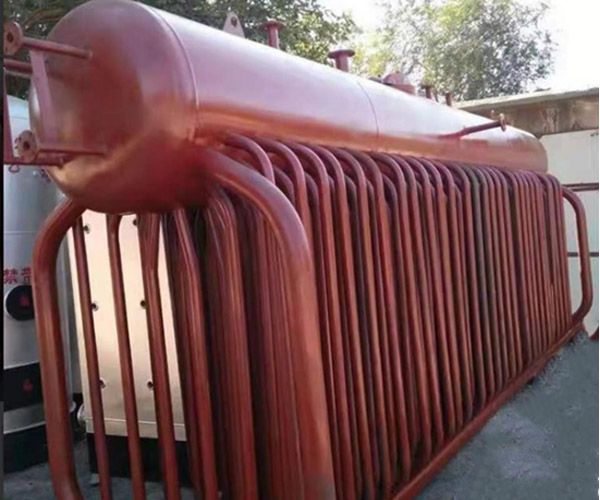
Most people may already know something about flue gas waste heat recovery, because they have already explained a lot about it. In order to let you know the relevant knowledge of flue gas waste heat recovery, the following is a brief introduction to the two methods commonly used for recovery. Anhui Horizontal fuel gas steam generator Two methods are usually adopted for flue gas waste heat recovery: one is to preheat the workpiece; The other is to preheat air for combustion support. The flue gas preheating workpiece needs to occupy a large volume for heat exchange, which is often limited by the operation site (this method cannot be used for intermittent furnaces). small-scale Horizontal fuel gas steam generator factory Preheating air for combustion support is a good method. It is generally configured on the heating furnace, which can also strengthen combustion, speed up the temperature rise of the furnace, and improve the thermal performance of the furnace. This can not only meet the requirements of the process, but also achieve significant comprehensive energy-saving effect.
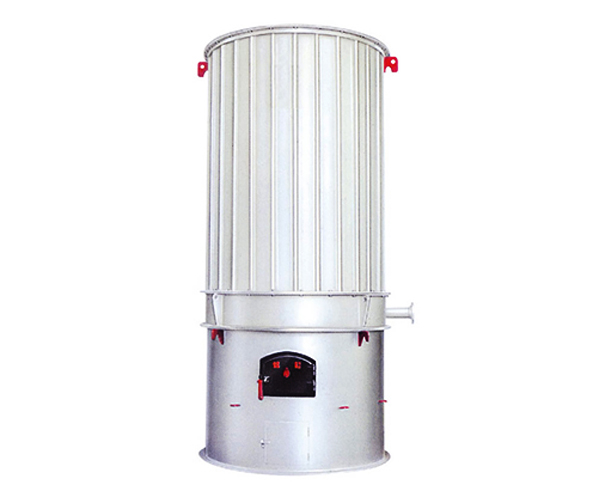
High heat exchange efficiency. The fusion rate at the contact is more than 95%, the contact thermal resistance is small, and the thermal conductivity is good. Low flow resistance. Anhui Horizontal fuel gas steam generator Since H-shaped finned tubes are similar to square structures, after being assembled into heat exchangers, the tubes are divided into many small channels by fins, which has a certain uniform effect on the air flow. The air flow is similar to longitudinal downstream flow, and the air flow resistance is relatively small. However, spiral finned tubes have strong air flow disturbance, high turbulence, and large air flow resistance due to the directivity of the fins. Less ash. The flue gas contains fly ash, which is easy to deposit on the windward side and leeward side of the pipe bundle. The H-shaped fin tube bundle has the characteristics of flow equalization and downstream flow, which is not easy to cause serious local ash deposition, and the fly ash can be taken away with the air flow in time. Therefore, compared with spiral finned tube heat exchanger, H-type finned tube heat exchanger has less ash deposition. small-scale Horizontal fuel gas steam generator factory Small size and low weight. H-shaped finned tube has high area expansion rate, less ash deposition, and high heat transfer efficiency. When the heat transfer capacity is equal, the space occupied by the heat exchanger can be small. For reconstruction projects, the heat exchange area can be arranged as much as possible in the limited space to reduce the exhaust gas temperature, improve the waste heat recovery efficiency, or increase the maintenance space to facilitate maintenance.