As a large equipment, the maintenance of gas-fired hot blast stove is one of the things that must be done. Anhui Waste heat boiler Regular maintenance can not only keep the hot blast stove clean, but also improve the service life of the hot blast stove. Therefore, it is the top priority in the use of hot blast stove. Today's editor will tell you how to maintain the hot blast stove regularly. In many manufacturers that use hot blast stoves, in order to better develop the enterprise, it is necessary to increase the number of hot blast stoves and improve the performance of hot blast stoves. small-scale Waste heat boiler factory When enterprises purchase hot blast stove equipment, they must understand their own needs and the products of hot blast stove manufacturers in the market. Therefore, the small edition of gas-fired hot blast stove tells us the problems to be considered in the selection of hot blast stove.
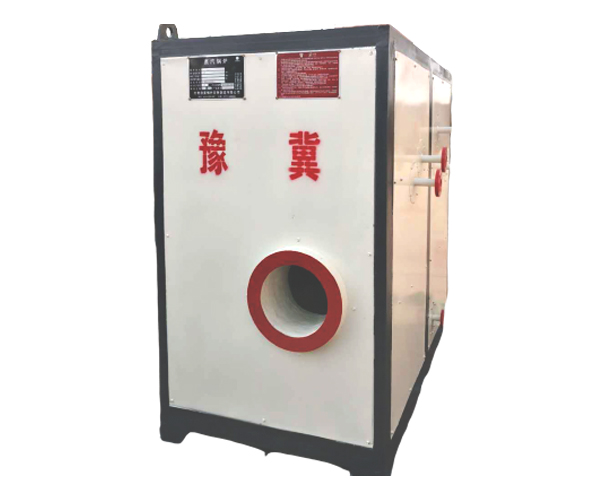
In the chemical industry, the electric heating heat conduction oil furnace is used for distillation, evaporation, polymerization, condensation, steel gate, fatliquoring, monotony, melting, dehydrogenation, forced heat preservation, and the heating of equipment composed of pesticides, intermediates, antioxidants, surfactants, spices, etc. Anhui Waste heat boiler In the plastic and rubber industries, the electric heating heat conduction oil furnace should be used for heating and insulation of hot pressing, hot rolling, kneading, kneading, internal mixing, vulcanization molding, jet injection molding machine, slurry mixer, conveyor belt dryer, screw kneading machine and mold. In metallurgy, machining and casting industries, electric heating heat conduction oil furnaces are used to heat metal degreasing tanks, dewar tanks, electric gate valves, cleaning tanks, electroplating tanks, aluminum plate oxidation tanks, electrode manufacturing, shower heat treatment equipment, phosphate treatment equipment, baking machine rooms, sand core drying, varnish spraying and monotonous equipment. small-scale Waste heat boiler factory In the food industry, the electric heating heat conduction oil furnace should be used for bread baking equipment, biscuit food baking equipment, candy production equipment, grain monotone equipment, cooking oil pressing and refining equipment, distillation pot, autoclave, conveyor belt dryer electric heater equipment.
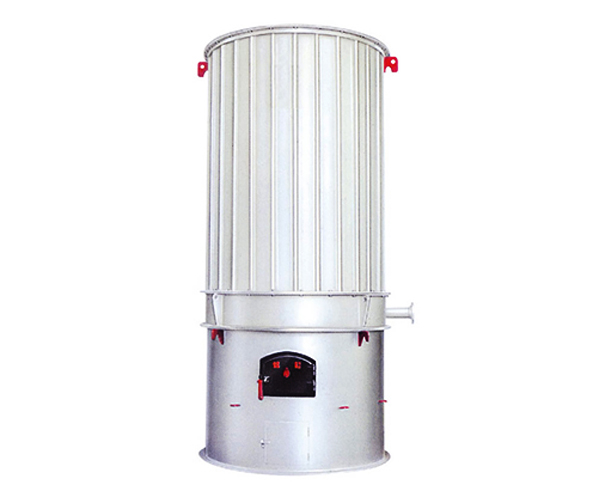
The existing industrial boiler flue gas waste heat recovery equipment mainly includes tubular heat exchanger and full heat pipe heat exchanger. Tube and tube heat exchanger can be composed of finned tube bundles. The advantage of finned tube is that it can withstand higher temperature, but has low heat transfer coefficient and large floor area. Anhui Waste heat boiler The flue gas of industrial boilers contains sulfur and other acidic substances. In the low temperature zone (flue gas outlet section), the temperature may be lower than the dew point of the acidic substances. The acidic substances will dew on the pipe wall, corrode the shell of the fin tube. The fin tube heat exchanger has poor operating reliability and low service life. small-scale Waste heat boiler factory The total heat pipe heat exchanger of boiler flue gas waste heat recovery equipment is composed of heat pipe bundles. Its shell is made of multi-layer composite materials. The heat pipe structure is complex, the cost is relatively expensive, the service life is short, and the steel consumption is large. It is difficult for users to accept it, and it is difficult to promote its application in production. The composite heat pipe heater not only takes into account the heat exchange effect, but also takes into account the economic affordability of the investors in production, which is particularly suitable for the current situation in China's industrial production.
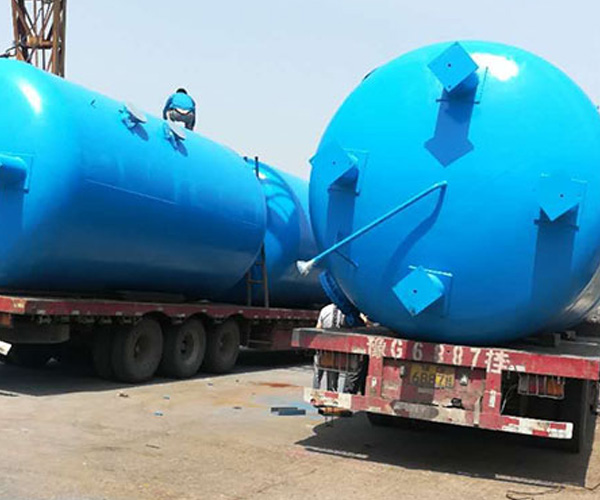
Most people may already know something about flue gas waste heat recovery, because they have already explained a lot about it. In order to let you know the relevant knowledge of flue gas waste heat recovery, the following is a brief introduction to the two methods commonly used for recovery. Anhui Waste heat boiler Two methods are usually adopted for flue gas waste heat recovery: one is to preheat the workpiece; The other is to preheat air for combustion support. The flue gas preheating workpiece needs to occupy a large volume for heat exchange, which is often limited by the operation site (this method cannot be used for furnaces that are used intermittently). small-scale Waste heat boiler factory Preheating air for combustion support is a good method. It is generally configured on the heating furnace, which can also strengthen combustion, speed up the temperature rise of the furnace, and improve the thermal performance of the furnace. This can not only meet the requirements of the process, but also achieve significant comprehensive energy-saving effect.
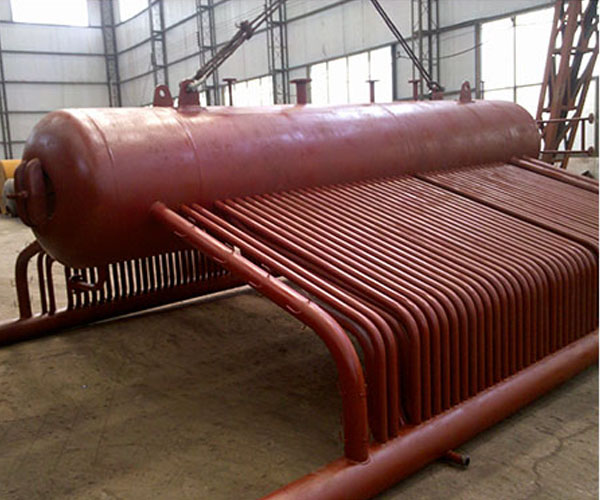
The steam generator pressure controller is used to control the generator, because it has no water level display, no board control, and its heating control is mainly controlled by the floating water level controller. Anhui Waste heat boiler When the water level is moderate, the floating point is connected to the control voltage to operate and heat the AC contactor. The generator has a simple structure and is currently used in the market. The common non heating fault of this generator is mainly found in the float level controller. First check the external wiring of the float level controller, connect the upper and lower control lines, and then remove the float level controller to see if it is flexible. small-scale Waste heat boiler factory You can use the manual to use the meter to determine whether the upper control point and the lower control point can be connected. Check the equipment and check for water. The float can fill the fuel tank, replace the float, and eliminate faults.