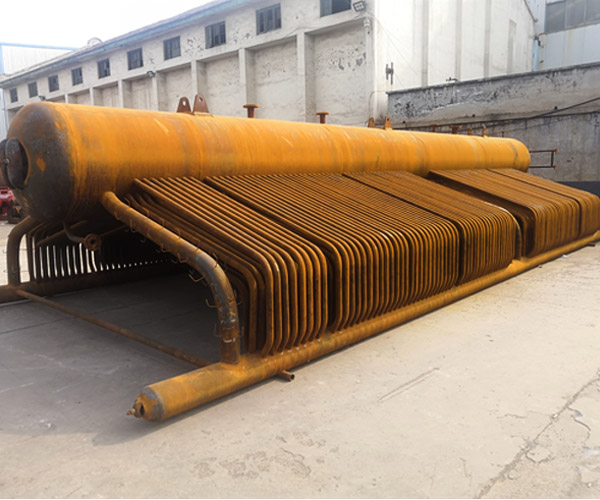
Effectively prevent and reduce low temperature corrosion of air preheater. Low temperature corrosion is caused by sulfur dioxide generated by combustion of sulfur in fuel. Anhui Electric steam generator Under the action of catalyst, sulfur dioxide is further oxidized to sulfur trioxide. Sulfur trioxide and water vapor in the flue gas generate sulfuric acid vapor, which greatly increases the dew point of the flue gas, condenses the sulfuric acid vapor on the flue gas side of the preheater tube wall, causing sulfuric acid corrosion of the preheater. The content of sulfur trioxide has a great impact on the corrosion rate of the preheater. The content of sulfur trioxide is not only related to the sulfur content in the fuel, but also related to the oxygen content in the flue gas. small-scale Electric steam generator manufactor Low oxygen combustion can significantly reduce the oxygen content in flue gas, greatly reduce the amount of sulfur dioxide oxidized to sulfur trioxide, reduce the dew point of flue gas, and effectively reduce the corrosion of preheater. Low oxygen combustion reduces the amount of flue gas. It can not only reduce the exhaust gas temperature, improve the boiler efficiency, but also reduce the power consumption of the forced draft fan and the wear of the heating surface.
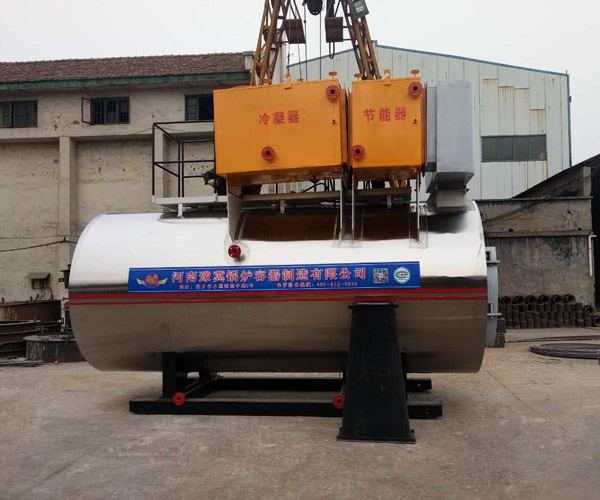
Most people may already know something about flue gas waste heat recovery, because they have already explained a lot about it. In order to let you know the relevant knowledge of flue gas waste heat recovery, the following is a brief introduction to the two methods commonly used for recovery. Anhui Electric steam generator Two methods are usually adopted for flue gas waste heat recovery: one is to preheat the workpiece; The other is to preheat air for combustion support. The flue gas preheating workpiece needs to occupy a large volume for heat exchange, which is often limited by the operation site (this method cannot be used for intermittent furnaces). small-scale Electric steam generator manufactor Preheating air for combustion support is a good method. It is generally configured on the heating furnace, which can also strengthen combustion, speed up the temperature rise of the furnace, and improve the thermal performance of the furnace. This can not only meet the requirements of the process, but also achieve significant comprehensive energy-saving effect.
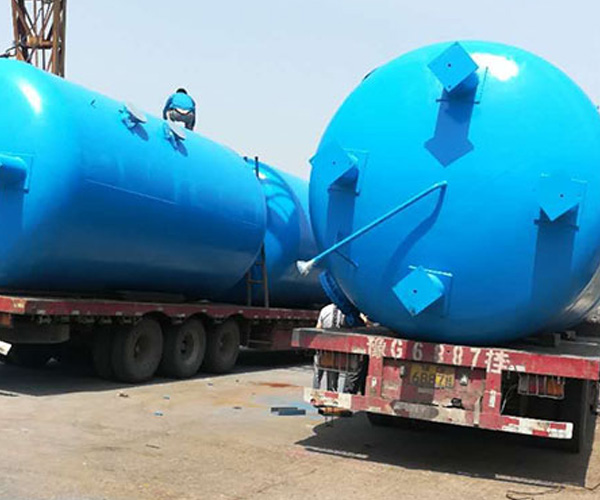
When using stainless steel storage tank, cracks appear on the head. If it is not handled in time, it will be dangerous, and how to handle this situation will be explained. Anhui Electric steam generator Firstly, the cracks in the stainless steel tank can were removed by polishing. After grinding, pits that do not need repair welding and do not affect the grading shall be formed within the allowable range. Otherwise, repair welding shall be carried out. The position of surface crack defect shall be determined by surface penetration defect detection, and the welding repair shall be completed. The horizontal gas tank shall be repaired, and the weld and surrounding materials shall be repaired. After that, argon tungsten arc welding shall be used for repair welding. small-scale Electric steam generator manufactor Tungsten argon arc welding shall be adopted for welding repair. It is suitable for back welding or skip welding, small size multi-layer and multi pass non rotating welding to avoid overheating of the weld. Water cooling measures are adopted. The defects of stainless steel storage tanks shall be removed by grinding with angular grinding wheel with conical grinding rod. Note that the abrasive grains of the grinding wheel should be perpendicular to the crack length. If the defect is deep, crack stop holes shall be drilled at both ends of the defect to prevent the crack from expanding with the grinding process. According to the inspection, in the stainless steel storage tank with primary side inspection, there are cracks at the head welds, and these defective welds have different edge bite degrees. Do not panic when the stainless steel tank can has cracks. The oil tank works. The above measures can be taken to solve this problem.
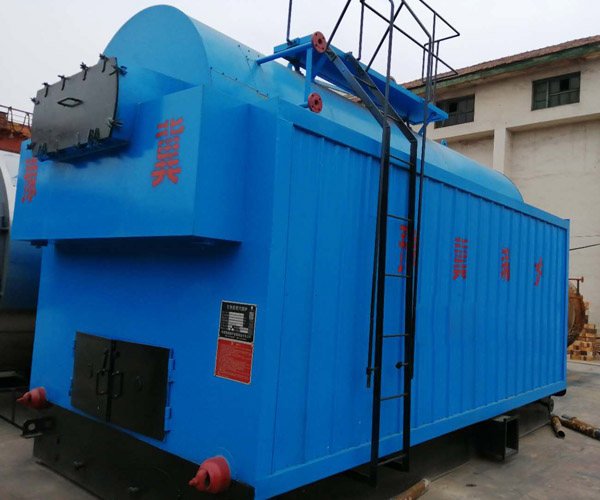
In the chemical industry, the electric heating heat conduction oil furnace is used for distillation, evaporation, polymerization, condensation, steel gate, fatliquoring, monotony, melting, dehydrogenation, forced heat preservation, and the heating of equipment composed of pesticides, intermediates, antioxidants, surfactants, spices, etc. Anhui Electric steam generator In the plastic and rubber industries, the electric heating heat conduction oil furnace should be used for heating and insulation of hot pressing, hot rolling, kneading, kneading, internal mixing, vulcanization molding, jet injection molding machine, slurry mixer, conveyor belt dryer, screw kneading machine and mold. In metallurgy, machining and casting industries, electric heating heat conduction oil furnaces are used to heat metal degreasing tanks, dewar tanks, electric gate valves, cleaning tanks, electroplating tanks, aluminum plate oxidation tanks, electrode manufacturing, shower heat treatment equipment, phosphate treatment equipment, baking machine rooms, sand core drying, varnish spraying and monotonous equipment. small-scale Electric steam generator manufactor In the food industry, the electric heating heat conduction oil furnace should be used for bread baking equipment, biscuit food baking equipment, candy production equipment, grain monotone equipment, cooking oil pressing and refining equipment, distillation pot, autoclave, conveyor belt dryer electric heater equipment.