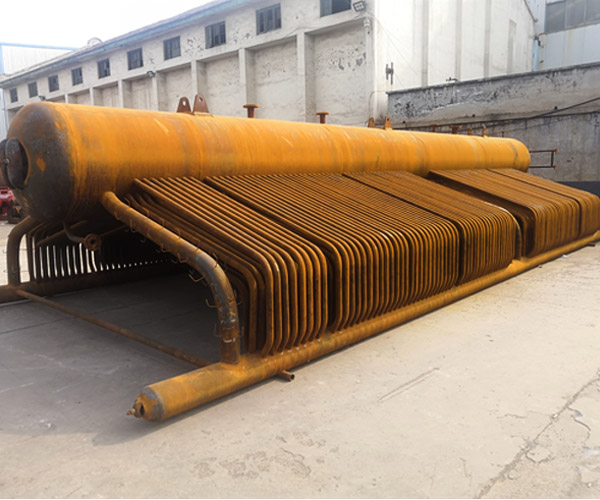
The produced waste heat boiler for hazardous waste incineration is a natural circulation water tube boiler, which adopts a single drum vertical layout and a full membrane water wall structure. Tianjin Electrically heated steam generator The surrounding, top and three middle membrane water-cooled walls form a tight series of heat exchange flues. The convection heating surface is no longer arranged inside the heat exchange flue, and radiation heat exchange is adopted, so as to ensure the smooth flow of high-temperature flue gas containing strong coking adhesive ash in the heat exchange flue. Full automatic shock soot blower is arranged on the membrane water wall, and inspection holes and observation holes are reserved. small-scale Electrically heated steam generator how much The bottom of the boiler is composed of membrane water walls on both sides to form a water-cooled ash bucket, and the lower part is connected with a closed spiral ash extractor. The settled soot in the waste heat boiler and the ash removed by the soot blower are discharged out of the boiler by the ash extractor. The furnace wall is of pipe laying structure, and the outside is covered with corrugated steel plate.
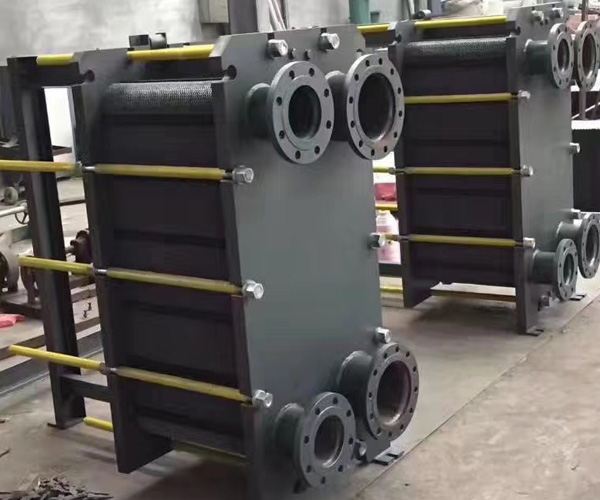
The starting of gas-fired boiler shall be carried out according to the operating procedures. The following is the accurate starting process of the analyzed gas-fired boiler: turn on the main power supply, start the gas-fired incinerator, and close the vent valve on the drum when it emits steam. Tianjin Electrically heated steam generator Check the manhole, handhole flange and valve of the gas boiler. If any leakage is found, fasten them. If leakage occurs after fastening, shut down the boiler for maintenance. When the gas pressure of the gas boiler rises by 0.05~0.1MPA, make up water, blow down, check the experimental water supply system and blow down equipment, and flush the water level gauge together. When the gas boiler pressure rises to 0.1~0.15MPA, flush the pressure gauge trap; When the gas pressure of the gas-fired boiler rises to 0.3MPA, turn the "load high fire/low fire" knob to "high fire" to strengthen incineration. When the pressure of the boiler rises to 2/3 of the operating pressure, start pipe warming and air supply, slowly open the main steam valve to prevent water hammer. small-scale Electrically heated steam generator how much When the drain valve emits steam, close it. After all the drain valves are closed, slowly open the main gas valve to fully open, and then reverse it for half a circle. Turn the "Control of gas incinerator" knob to the automatic gear.
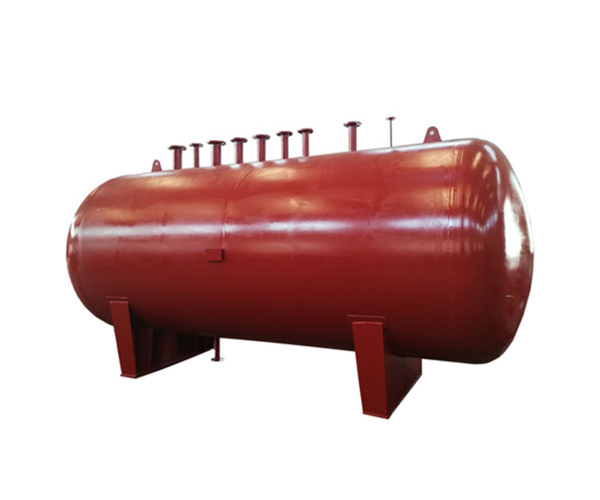
The flue gas waste heat recovery device also has the following characteristics: 1. Energy saving. It uses new heat exchange fins and heat exchange elements to make heat exchange more fully, and the exhaust gas temperature can be reduced to 40 ℃~80 ℃; The boiler efficiency can be increased by 6~15%, and the condensate drainage structure can fully recover the latent heat in the flue gas, with remarkable energy-saving effect. Tianjin Electrically heated steam generator Due to the special structure, the total pressure drop is small and the power consumption is small, that is, the smoke pressure drop is small and meets the system requirements. 2. Beautiful. Due to the use of efficient heat exchange elements and reasonable structural configuration, this product has the characteristics of compact structure, small size, beautiful appearance, etc. small-scale Electrically heated steam generator how much Durable. The heat exchange tube of the flue gas waste heat recovery device is made of stainless steel aluminum fins for efficient anti-corrosion. The thermal stress, anti-corrosion performance and strength are fully considered when the equipment is manufactured, which can ensure the safety, reliability and stability of the equipment, with a service life of more than 25 years.
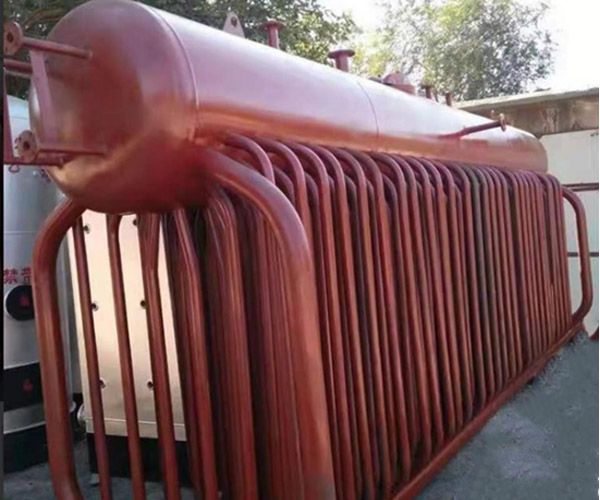
Economical and energy-saving: the new generation of biomass pellet fuel can save 30% - 60% of the operating cost compared with oil, gas and electric heating boilers. Convenient installation: this series of generators do not need to be inspected, and the tedious annual approval procedure can be avoided. Tianjin Electrically heated steam generator At the same time, the machine is assembled for modules, and professional installation procedures are not required. High efficiency operation: adopt the design of multiple flue gas backflow, optimize oxygen enrichment for many times, cooperate with professional dust removal and energy saving equipment, the thermal efficiency reaches more than 90%, and can continuously produce steam. Low carbon and environmental protection: Through reasonable design, biomass fuel is semi gasified and burned, and smokeless combustion is achieved. Reliable security: It is equipped with pressure, water shortage, security valve and other protection devices to ensure stable operation and reliable security of the boiler. small-scale Electrically heated steam generator how much Simple operation: microcomputer intelligent one button operation, automatic feeding, automatic ignition, cycle start stop and fault alarm functions are used for simple operation. The labor intensity is greatly reduced, and the use of the boiler is more humanized. Convenient maintenance: the overall structure of the boiler is reasonable, and the installation is convenient. There is a cleaning port under each furnace. The main components have inspection ports for future maintenance and repair.
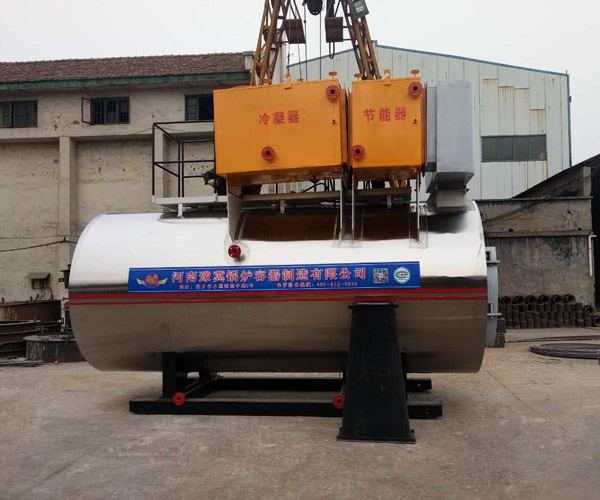
Energy saving. The waste heat boiler adopts new heat exchange fins and heat exchange elements, which enables full heat exchange. The boiler efficiency can be increased by 6~15%, and the condensate drainage structure can fully recover the latent heat in the flue gas. The energy-saving effect is remarkable. Tianjin Electrically heated steam generator Due to the special structure, the total pressure drop is small and the power consumption is small, that is, the smoke pressure drop is small and meets the system requirements. beautiful. Due to the use of efficient heat exchange elements and reasonable structural configuration, the waste heat boiler has the characteristics of compact structure, small size, beautiful appearance, etc. Durable. Heat exchange tubes of waste heat boiler facilities are made of stainless steel aluminum fins for corrosion prevention. small-scale Electrically heated steam generator how much The thermal stress, anti-corrosion performance and strength are fully considered when the equipment is manufactured, which can ensure the safety, reliability and stability of the equipment, with a service life of more than 25 years.
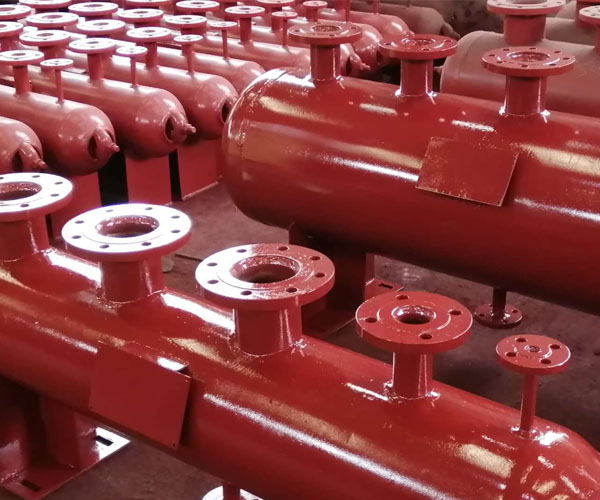
High heat exchange efficiency. The fusion rate at the contact is more than 95%, the contact thermal resistance is small, and the thermal conductivity is good. Low flow resistance. Tianjin Electrically heated steam generator Since H-shaped finned tubes are similar to square structures, after being assembled into heat exchangers, the tubes are divided into many small channels by fins, which has a certain uniform effect on the air flow. The air flow is similar to longitudinal downstream flow, and the air flow resistance is relatively small. However, spiral finned tubes have strong air flow disturbance, high turbulence, and large air flow resistance due to the directivity of the fins. Less ash. The flue gas contains fly ash, which is easy to deposit on the windward side and leeward side of the pipe bundle. H-shaped finned tube bundle has the characteristics of flow equalization and downstream flow, so it is not easy to cause serious local ash deposition, and the fly ash can be taken away with the air flow in time. Therefore, compared with spiral finned tube heat exchanger, H-type finned tube heat exchanger has less ash deposition. small-scale Electrically heated steam generator how much Small size and low weight. H-shaped finned tube has high area expansion rate, less ash deposition, and high heat transfer efficiency. When the heat transfer capacity is equal, the space occupied by the heat exchanger can be small. For reconstruction projects, the heat exchange area can be arranged as much as possible in the limited space to reduce the exhaust gas temperature, improve the waste heat recovery efficiency, or increase the maintenance space to facilitate maintenance.