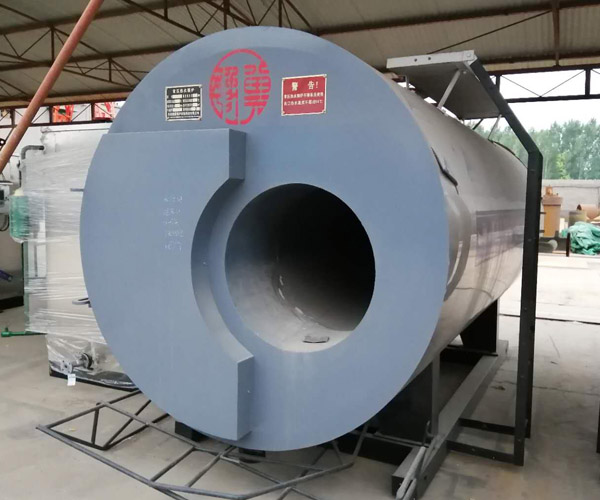
The produced waste heat boiler for hazardous waste incineration is a natural circulation water tube boiler, which adopts a single drum vertical layout and a full membrane water wall structure. Gansu Gas steam generator The surrounding, top and three middle membrane water-cooled walls form a tight series of heat exchange flues. The convection heating surface is no longer arranged inside the heat exchange flue, and radiation heat exchange is adopted, so as to ensure the smooth flow of high-temperature flue gas containing strong coking adhesive ash in the heat exchange flue. Full automatic shock soot blower is arranged on the membrane water wall, and inspection holes and observation holes are reserved. small-scale Gas steam generator factory The bottom of the boiler is composed of membrane water walls on both sides to form a water-cooled ash bucket, and the lower part is connected with a closed spiral ash extractor. The settled soot in the waste heat boiler and the ash removed by the soot blower are discharged out of the boiler by the ash extractor. The furnace wall is of pipe laying structure, and the outside is covered with corrugated steel plate.
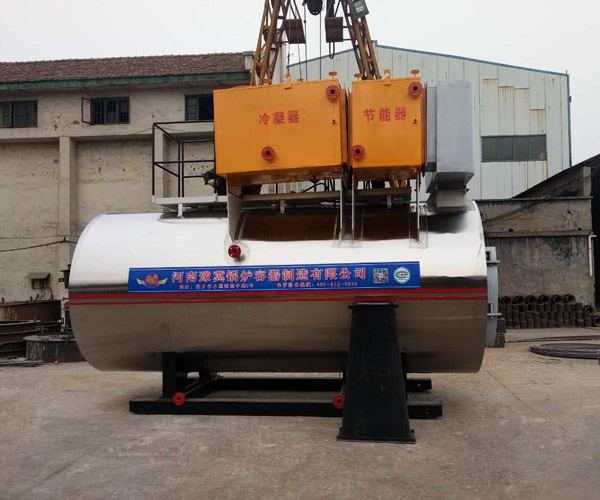
The furnace liner is the combustion chamber of the horizontal gas-fired heat transfer oil furnace. The burner nozzle is placed in the front of the furnace liner, and the high-temperature flue gas generated by combustion extends to the rear, leaving the furnace liner and returning to the space. Generally, the number of times of returning is not more than four, and the common one is the three return heat conduction oil furnace. Gansu Gas steam generator This type of heat transfer oil furnace can be divided into dry back type heat transfer oil furnace and full wet back type heat transfer oil furnace according to the structure of the flue gas reentry space at the rear of the furnace. The flue gas reentry space of the dry back heat conduction oil furnace is enclosed by refractory materials; The flue gas reentry space of the full wet back type heat conduction oil furnace is composed of a recuperative chamber immersed in water. In addition, there is a central regenerative heat conduction oil furnace: that is, the back wall of the furnace liner is sealed inside the boiler shell, and the flue gas is turned back to the front from the inner wall around the furnace liner after encountering. This type of heat transfer oil furnace can also be regarded as a full wet back heat transfer oil furnace. small-scale Gas steam generator factory Although the dry back heat transfer oil furnace is simple in structure, the refractory material at the rear of the furnace liner is easily damaged, and the rear tube plate is often directly washed by high temperature flue gas. The temperature difference is large, so the dry back heat transfer oil furnace is obsolete. At present, few manufacturers produce it; Although the full wet back heat conduction oil furnace has a complex structure, it avoids the problem of flue gas sealing in the reentry space and is suitable for micro positive pressure combustion.
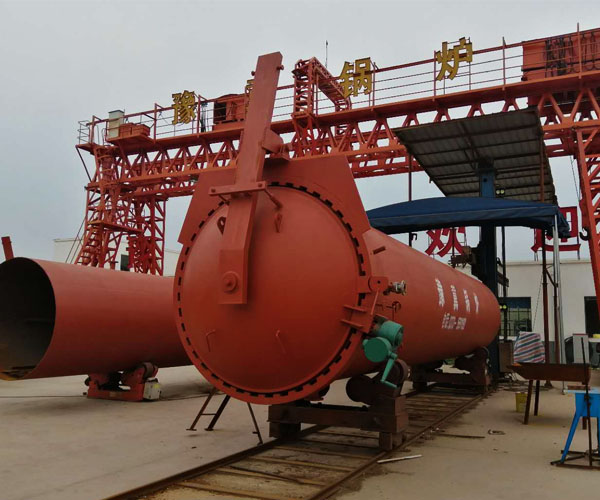
The waste heat recovery of flue gas can not only be used for heating or power generation to achieve energy-saving effect, but also can be beneficial to environmental protection and achieve dual effects of energy conservation and environmental protection. Gansu Gas steam generator In general, the important equipment of waste heat power generation is waste heat boiler, which mainly uses heat or combustible substances in waste gas, waste liquid and other working medium as heat source, and produces steam mainly for power generation. There are many ways to recover waste heat from flue gas of waste heat boiler. Generally, comprehensive utilization of waste heat is followed by direct utilization and indirect utilization. small-scale Gas steam generator factory Generally speaking, if heat sources are needed in the process, the waste heat utilization is mainly comprehensive utilization. First, the heat source is recovered and fed back to the process for reuse. If there is any surplus, it can be used for power generation or as the heat source for central heating; If there is no surplus, it will be directly used instead of being used for power generation; If the process does not need more heat sources, then indirect use, mainly power generation or public heating.
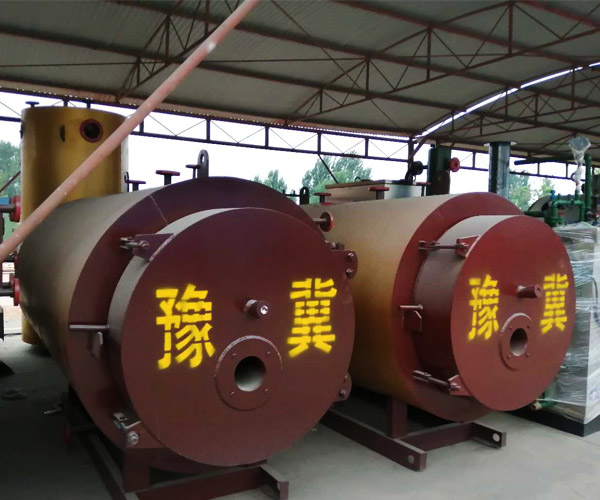
The steam generator pressure controller is used to control the generator, because it has no water level display, no board control, and its heating control is mainly controlled by the floating water level controller. Gansu Gas steam generator When the water level is moderate, the floating point is connected to the control voltage to operate and heat the AC contactor. The generator has a simple structure and is currently used in the market. The common non heating fault of this generator is mainly found in the float level controller. First check the external wiring of the float level controller, connect the upper and lower control lines, and then remove the float level controller to see if it is flexible. small-scale Gas steam generator factory You can use the manual to use the meter to determine whether the upper control point and the lower control point can be connected. Check the equipment and check for water. The float can fill the fuel tank, replace the float, and eliminate faults.
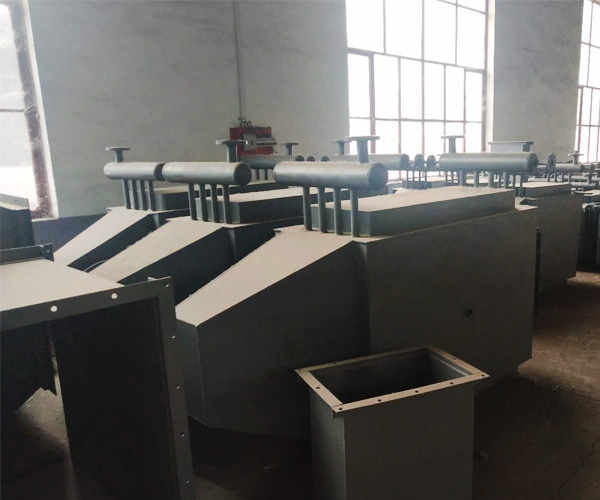
The main parts of the waste heat boiler can be divided into drum, pipe, header, membrane wall, tube panel, tube box, etc. These parts are the parts with specific process requirements in the waste heat boiler. Gansu Gas steam generator For example, the drum should go through metal flaw detection, heat treatment, hydrostatic test and other processes to improve the stability of the waste heat boiler. At the same time, because the header needs high sealing, manual welding is required, and the welding quality needs to be tested. It can be seen that due to the complexity of the working environment of the waste heat boiler, it has special requirements for its internal structural members. small-scale Gas steam generator factory In the process of designing and manufacturing the waste heat boiler, the process designer should consider the advantages and disadvantages of various processes, and then select a reasonable process to complete the manufacturing of the waste heat boiler. For example, the serpentine parts in the waste heat boiler cannot be bent automatically by the machine, so they can only be bent manually.