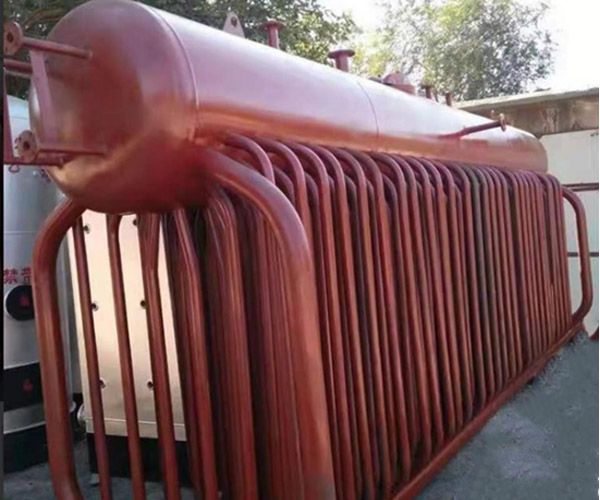
The waste heat recovery of flue gas can not only be used for heating or power generation to achieve energy-saving effect, but also can be beneficial to environmental protection and achieve dual effects of energy conservation and environmental protection. Chengdu Waste heat boiler In general, the important equipment of waste heat power generation is waste heat boiler, which mainly uses heat or combustible substances in waste gas, waste liquid and other working medium as heat source, and produces steam mainly for power generation. There are many ways to recover waste heat from flue gas of waste heat boiler. Generally, comprehensive utilization of waste heat is followed by direct utilization and indirect utilization. small-scale Waste heat boiler factory Generally speaking, if heat sources are needed in the process, the waste heat utilization is mainly comprehensive utilization. First, the heat source is recovered and fed back to the process for reuse. If there is any surplus, it can be used for power generation or as the heat source for central heating; If there is no surplus, it will be directly used instead of being used for power generation; If the process does not need more heat sources, then indirect use, mainly power generation or public heating.
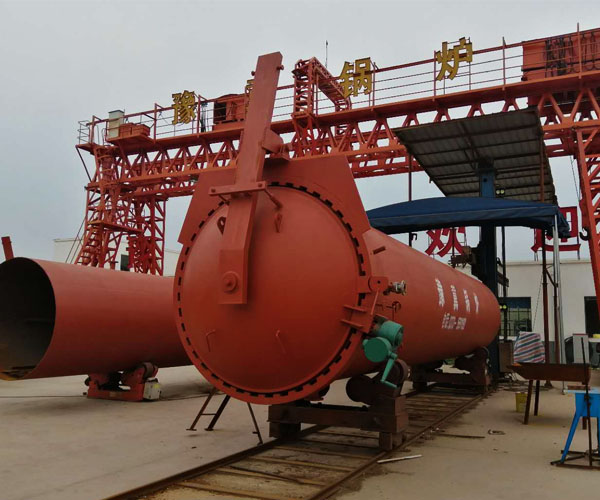
The hardness of water is mainly formed and expressed by calcium and magnesium, so cation exchange resin (water softener) is generally used to replace Ca2+and Mg2+(the main component forming scale) in the water. With the increase of Ca2+and Mg2+in the resin, the efficiency of the resin to remove Ca2+and Mg2+gradually decreases. Chengdu Waste heat boiler When the resin absorbs a certain amount of calcium and magnesium ions, it must be regenerated. The regeneration process is to wash the resin layer with salt water in the salt tank to replace the hardness ions on the resin. With the regeneration waste liquid discharged out of the tank, the resin will resume its softening and exchange function. small-scale Waste heat boiler factory Because the hardness of water is mainly formed by calcium and magnesium and represents that the hardness of water is mainly formed by calcium and magnesium and represents the principle of sodium ion exchange softening treatment, which is to exchange the hardness components Ca2+and Mg2+in the water with the Na+in the resin by passing the raw water through the sodium cation exchange resin, so as to absorb Ca2+and Mg2+in the water and soften the water.
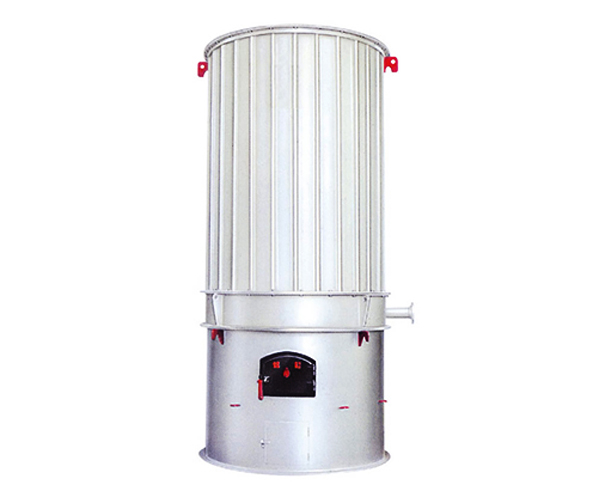
Diaphragm air pressure tank is an energy storage device composed of a steel shell and a rubber diaphragm liner. The rubber diaphragm completely separates the water chamber from the air chamber. When water with external pressure is filled into the liner of the diaphragm air pressure tank, the air sealed in the diaphragm air pressure tank will be compressed. Chengdu Waste heat boiler According to Boyle's gas law, the volume of gas becomes smaller after being compressed, and the pressure increases to store energy. The expansion of compressed gas can press the water in the rubber diaphragm out of the tank. Diaphragm pressure tank is widely used in central air conditioning, boiler, water heater, frequency conversion and constant pressure water supply equipment. It can buffer the pressure fluctuation of the system and eliminate water hammer to stabilize the pressure and unload the load. small-scale Waste heat boiler factory When the water pressure in the system changes slightly, the automatic expansion and contraction of the diaphragm air pressure capsule will have a buffer effect on the change of water pressure, which can ensure the stability of the water pressure in the system, and the water pump will not be opened frequently due to the change of pressure.
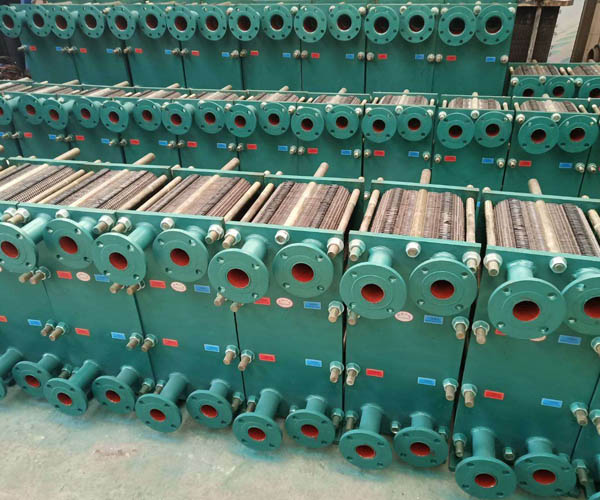
Stainless steel for pressure vessels and its welding characteristics. The so-called stainless steel refers to the addition of a certain amount of chromium in the steel to keep the steel in a passive state and free from rust. Chengdu Waste heat boiler For this purpose, the chromium content must be more than 12%. In order to improve the passivity of steel, it is often necessary to add nickel, molybdenum and other elements that can passivate steel into stainless steel. Stainless steel is generally referred to as stainless steel and acid resistant steel. Stainless steel companies do not have certain acid resistance, and acid resistant steel generally has a good stainless property. small-scale Waste heat boiler factory According to its steel structure, stainless steel can be divided into four categories, namely, austenitic stainless steel, ferritic stainless steel, martensitic stainless steel, and austenitic ferritic duplex stainless steel.
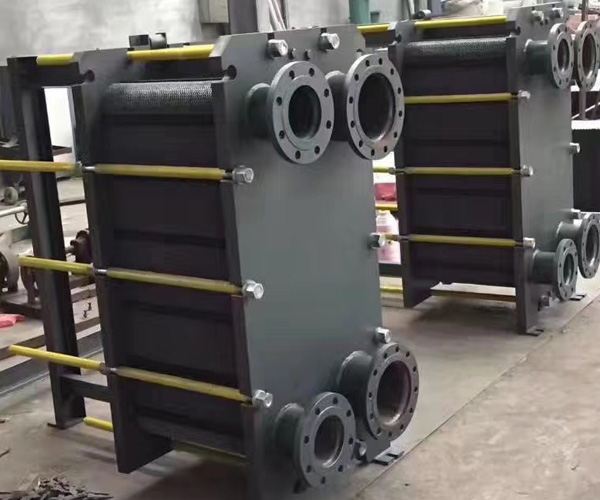
System oil drainage: circulate the heat transfer oil between 120 ± 5 to drain the heat transfer oil in the system (if you do not replace the oil, please find a clean container to store it properly). Prepare an appropriate amount of coke removal cleaning agent for the heat transfer oil system, drain the oil in the gas-fired heat transfer oil boiler system, and disconnect the cleaning system from the oil storage tank (close the valve), including the connection between the high-level tank and the oil storage tank. Chengdu Waste heat boiler Residual oil blowing steps: connect the air compressor at the pressure gauge or other places that can be connected, boost the system to 0.3-0.4MPa, and discharge it instantaneously; Repeat this process until the residual oil is blown out. The gas-fired heat transfer oil boiler, circulating pump, and other heat users form a cleaning circulating circuit for decoking and cleaning: add diluted cleaning agent to the system and fill it up to 1/2 of the water level of the high-level tank. Dosage of coke removal cleaning agent: 10~20%, the specific dosage shall be determined according to the scale thickness. Temperature: 90-95, time: 12-72 hours, which can be determined according to the scale thickness. Rinsing and cleaning: after cleaning, drain the residual liquid in the system and add clean water to rinse twice until the coke remover is free of foam and the water is clear. small-scale Waste heat boiler factory Temperature: 85-95, time: 5-8 hours Water blowing steps: after cleaning, connect the air compressor at the pressure gauge or other places that can be connected, use compressed air to boost the system to 0.3-0.4 MPa, and vent at each low point. Repeat this process until the water is blown out. Waste liquid treatment: the cleaning waste liquid generated in the cleaning process is discharged after being treated in the biochemical tank.