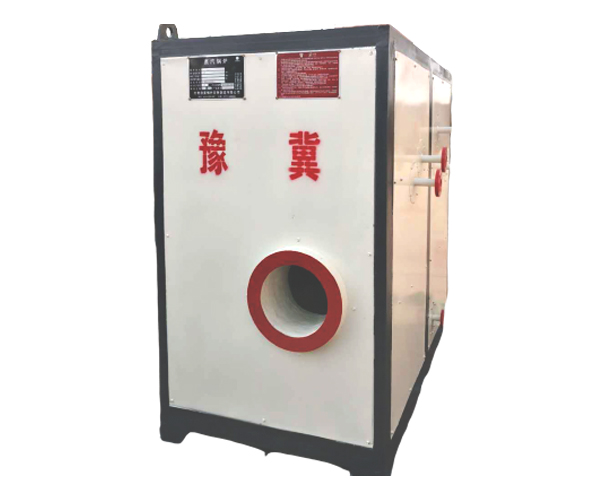
The main parts of the waste heat boiler can be divided into drum, pipe, header, membrane wall, tube panel, tube box, etc. These parts are the parts with specific process requirements in the waste heat boiler. Guangdong Energy saving steam generator For example, the drum should go through metal flaw detection, heat treatment, hydrostatic test and other processes to improve the stability of the waste heat boiler. At the same time, because the header needs high sealing, manual welding is required, and the welding quality needs to be tested. It can be seen that due to the complexity of the working environment of the waste heat boiler, it has special requirements for its internal structural members. vertical Energy saving steam generator factory In the process of designing and manufacturing the waste heat boiler, the process designer should consider the advantages and disadvantages of various processes, and then select a reasonable process to complete the manufacturing of the waste heat boiler. For example, the serpentine parts in the waste heat boiler cannot be bent automatically by the machine, so they can only be bent manually.
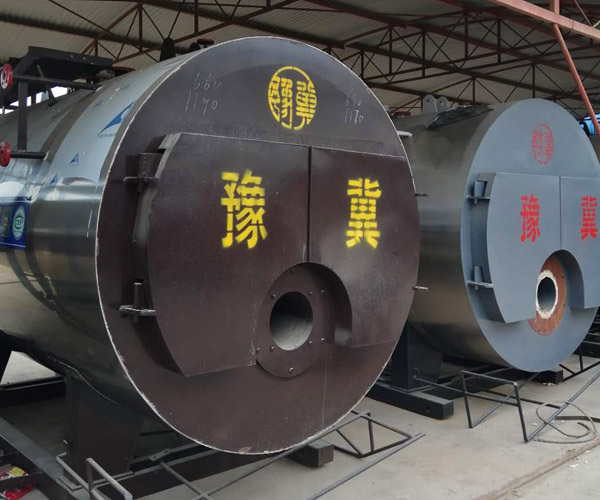
The waste heat boiler is composed of drum, movable smoke hood, feeding pipe groove, oxygen lance mouth, furnace mouth section flue, inclined section 1 flue, inclined section 2 flue, last section 1 flue, last section 2 flue, nitrogen sealing device and nitrogen sealing plug, manhole, micro differential pressure tapping device, flue support and hanger. Guangdong Energy saving steam generator Unlike conventional boilers, waste heat boilers do not produce combustion process and do not have combustion related equipment. Essentially, they are just gas water/steam heat exchangers. The waste heat boiler is divided into six circulation loops. Each circulation loop is composed of downcomer and riser. The feed water of each section of flue is introduced from the drum through downcomer to the lower header of each flue, and then enters into each heating surface. The water passes through the heating surface and generates steam into the header, and then is introduced into the drum through the riser. vertical Energy saving steam generator factory The needle tube waste heat recovery device is a special high-efficient energy-saving product specially designed for waste heat recovery of flue gas. The heat recovery boiler uses needle shaped tubes to strengthen the heat elements to expand the heating surface. The heating surface on the water pipe smoke side can be greatly increased. At the same time, the smoke will form strong turbulence when passing through the needle shaped tube surface, which will improve the heat transfer efficiency and reduce the soot accumulation.
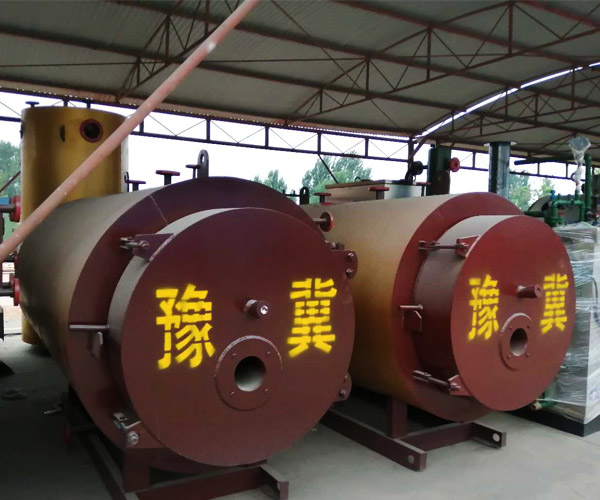
The steam used in the steam generator of the hotel laundry is usually 0.4~0.6MPa saturated steam. The working temperature of steam is not very high. Guangdong Energy saving steam generator The steam boiler of the hotel requires high steam efficiency due to operating costs, so it can save operating costs. The area of the hotel is relatively limited, so the steam boiler with small floor area must be selected. In order to control the investment cost and heat loss of the steam pipe, the steam boiler is usually placed on the side of the laundry room. vertical Energy saving steam generator factory The steam equipment in the hotel laundry room can only be turned on when washing, not when washing. Therefore, the steam generator is required to start steam production quickly. Laundry equipment is sometimes opened a lot and sometimes less, so the steam boiler is required to adjust the steam volume within the specified range.
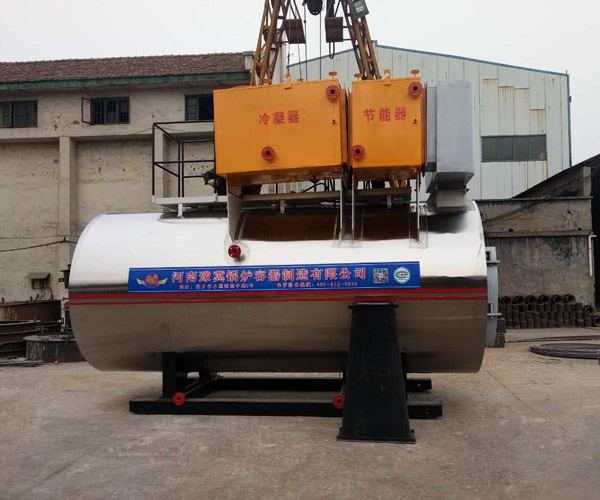
The existing industrial boiler flue gas waste heat recovery equipment mainly includes tubular heat exchanger and full heat pipe heat exchanger. Tube and tube heat exchanger can be composed of finned tube bundles. The advantage of finned tube is that it can withstand higher temperature, but has low heat transfer coefficient and large floor area. Guangdong Energy saving steam generator The flue gas of industrial boilers contains sulfur and other acidic substances. In the low temperature zone (flue gas outlet section), the temperature may be lower than the dew point of the acidic substances. The acidic substances will dew on the pipe wall, corrode the shell of the fin tube. The fin tube heat exchanger has poor operating reliability and low service life. vertical Energy saving steam generator factory The total heat pipe heat exchanger of boiler flue gas waste heat recovery equipment is composed of heat pipe bundles. Its shell is made of multi-layer composite materials. The heat pipe structure is complex, the cost is relatively expensive, the service life is short, and the steel consumption is large. It is difficult for users to accept it, and it is difficult to promote its application in production. The composite heat pipe heater not only takes into account the heat exchange effect, but also takes into account the economic affordability of the investors in production, which is particularly suitable for the current situation in China's industrial production.