The heat transfer coefficient of the waste heat recovery boiler in the brick factory of the power plant is high: the heat transfer of waste gas, water and steam is carried out on the outer surface of the heat pipe, and the outer side of the waste gas heat pipe is finned, so that the heat transfer area is increased, the heat transfer is strengthened, and the heat transfer coefficient is greatly changed.
Strong ability to prevent ash deposition, blocking and corrosion: by adjusting the proportion of the heating surface of the cold and hot sections of the heat pipe, the pipe wall temperature can be adjusted to be higher than the flue gas dew point temperature, which can effectively prevent acid dew point and sulfur corrosion in the flue gas, extend the service life of the heat exchanger, and ensure the heat exchange efficiency of the heat exchanger.
Prevention of leakage of water and steam system: during operation, due to the large amount of waste gas washing, even if the pipe is slightly damaged, the air and water on the cold side will not leak to the hot side, ensuring the safe operation of the system, which is also the characteristics of this equipment different from those in the general flue.
Small resistance loss is applicable to the reconstruction of old units: in general, waste heat recovery equipment is added, and the resistance of hot waste gas is increased to about 1500Pa. The damage of single or multiple heat pipes will not affect the overall use of the equipment.
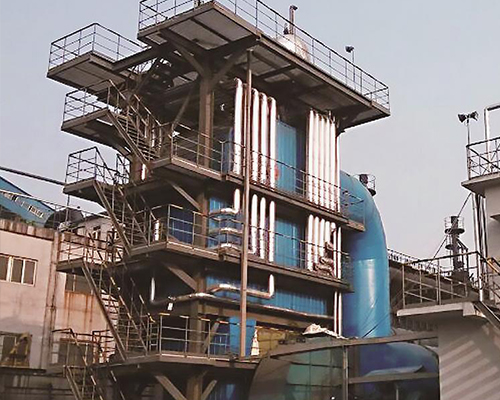

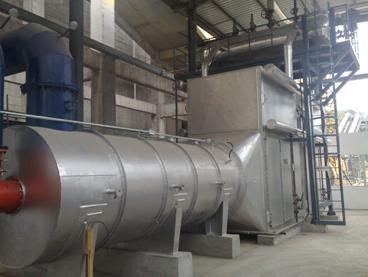
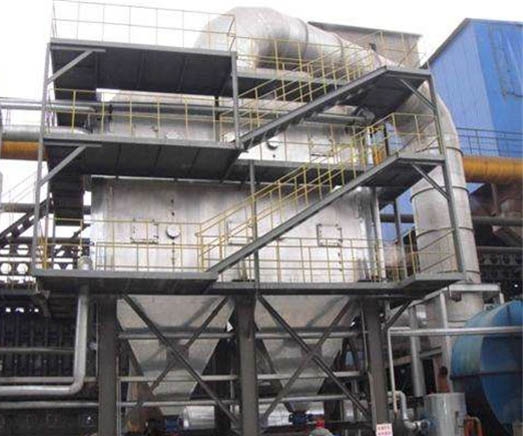
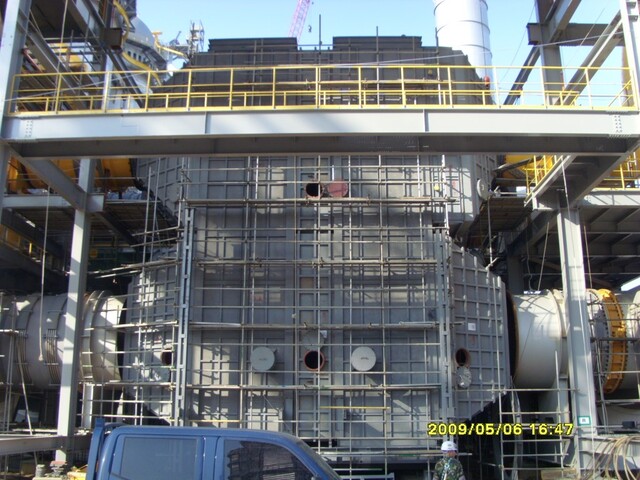
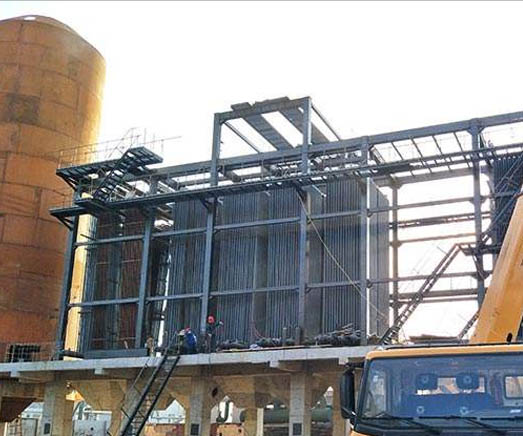
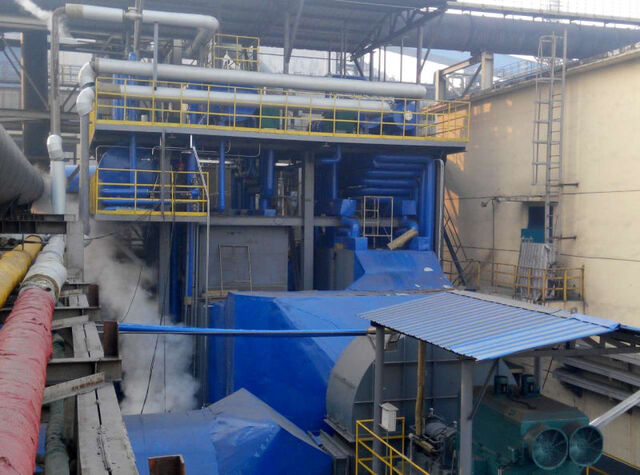