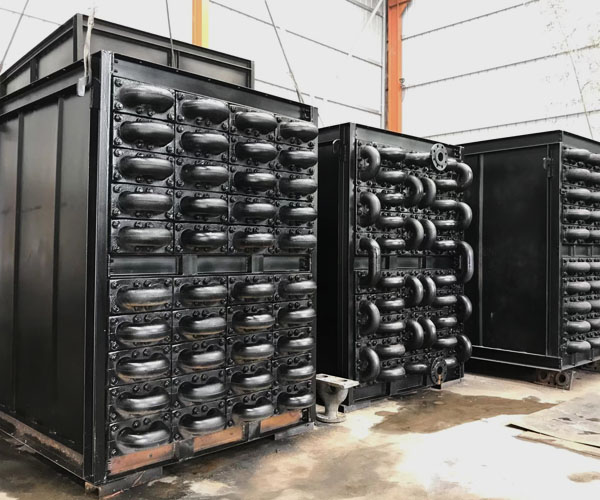
The flue gas waste heat recovery device also has the following characteristics: 1. Energy saving. It uses new heat exchange fins and heat exchange elements to make heat exchange more fully, and the exhaust gas temperature can be reduced to 40 ℃~80 ℃; The boiler efficiency can be increased by 6~15%, and the condensate drainage structure can fully recover the latent heat in the flue gas, with remarkable energy-saving effect. Guangdong Fully automatic steam generator Due to the special structure, the total pressure drop is small and the power consumption is small, that is, the smoke pressure drop is small and meets the system requirements. 2. Beautiful. Due to the use of efficient heat exchange elements and reasonable structural configuration, this product has the characteristics of compact structure, small size, beautiful appearance, etc. vertical Fully automatic steam generator factory Durable. The heat exchange tube of the flue gas waste heat recovery device is made of stainless steel aluminum fins for efficient anti-corrosion. The thermal stress, anti-corrosion performance and strength are fully considered when the equipment is manufactured, which can ensure the safety, reliability and stability of the equipment, with a service life of more than 25 years.
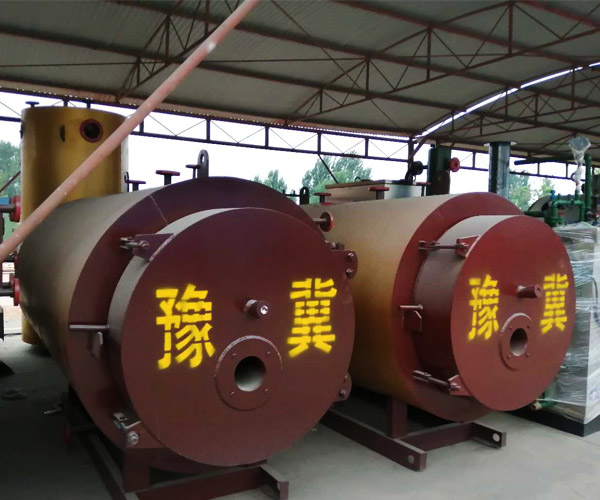
The starting of gas-fired boiler shall be carried out according to the operating procedures. The following is the accurate starting process of the analyzed gas-fired boiler: turn on the main power supply, start the gas-fired incinerator, and close the vent valve on the drum when it emits steam. Guangdong Fully automatic steam generator Check the manhole, handhole flange and valve of the gas boiler. If any leakage is found, fasten them. If leakage occurs after fastening, shut down the boiler for maintenance. When the gas pressure of the gas boiler rises by 0.05~0.1MPA, make up water, blow down, check the experimental water supply system and blow down equipment, and flush the water level gauge together. When the gas boiler pressure rises to 0.1~0.15MPA, flush the pressure gauge trap; When the gas pressure of the gas-fired boiler rises to 0.3MPA, turn the "load high fire/low fire" knob to "high fire" to strengthen incineration. When the pressure of the boiler rises to 2/3 of the operating pressure, start pipe warming and air supply, slowly open the main steam valve to prevent water hammer. vertical Fully automatic steam generator factory When the drain valve emits steam, close it. After all the drain valves are closed, slowly open the main gas valve to fully open, and then reverse it for half a circle. Turn the "Control of gas incinerator" knob to the automatic gear.
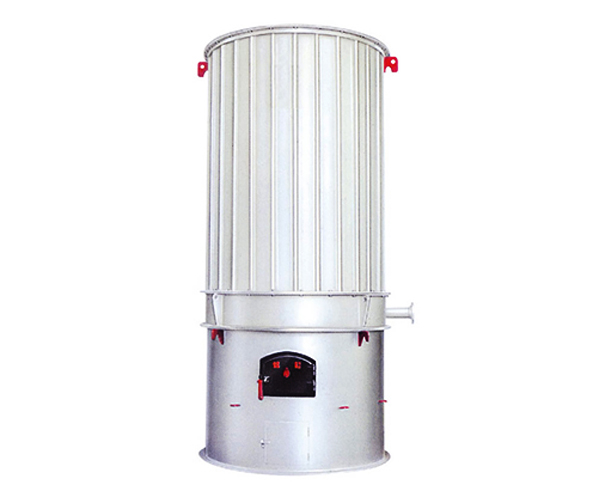
The waste heat boiler greatly improves the utilization rate of heat released by fuel combustion, so this kind of boiler saves energy; Fuel oil, gas and coal combustion generate high-temperature flue gas to release heat. The high-temperature flue gas first enters the furnace, then enters the waste heat recovery device of the front smoke box, then enters the pyrotechnic tube, and then enters the waste heat recovery device in the flue of the rear smoke box. The high-temperature flue gas turns into low-temperature flue gas and is discharged into the atmosphere through the chimney. Guangdong Fully automatic steam generator Conditions conducive to quick startup of waste heat boiler: (1) The waste heat boiler adopts forced circulation, which has the priority of quick startup. (2) The flue gas baffle is hydraulically controlled, which can be used to adjust the sky in principle. The flue gas flow into the boiler is reduced. (3) The adjustable guide vane at the inlet of gas turbine can not only adjust the flue gas flow of gas turbine, but also increase or decrease the exhaust gas temperature of gas turbine through the selection of IGV temperature control mode. (4) The steam turbine bypass is designed for the rated evaporation capacity of the boiler. (5) The welded bends and headers of each heating module of the boiler are in the boiler. (6) Similar boilers in other gas turbine power plants can not be reduced when starting, and can be used to adjust the main steam pressure of the boiler. Outside the wall, contact with high-temperature smoke is avoided. vertical Fully automatic steam generator factory Operating experience of gas turbine load, such as simultaneous startup of gas turbine and waste heat boiler (flue gas damper fully open). Under the possibility of quick startup of waste heat boiler, the water level of steam drum and deaerator will lose control after the flue gas baffle is opened.
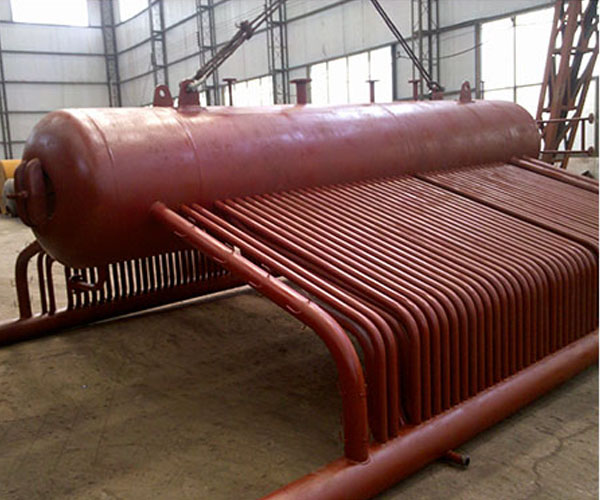
System oil drainage: circulate the heat transfer oil between 120 ± 5 to drain the heat transfer oil in the system (if you do not replace the oil, please find a clean container to store it properly). Prepare an appropriate amount of coke removal cleaning agent for the heat transfer oil system, drain the oil in the gas-fired heat transfer oil boiler system, and disconnect the cleaning system from the oil storage tank (close the valve), including the connection between the high-level tank and the oil storage tank. Guangdong Fully automatic steam generator Residual oil blowing steps: connect the air compressor at the pressure gauge or other places that can be connected, boost the system to 0.3-0.4MPa, and discharge it instantaneously; Repeat this process until the residual oil is blown out. The gas-fired heat transfer oil boiler, circulating pump, and other heat users form a cleaning circulating circuit for decoking and cleaning: add diluted cleaning agent to the system and fill it up to 1/2 of the water level of the high-level tank. Dosage of coke removal cleaning agent: 10~20%, the specific dosage shall be determined according to the scale thickness. Temperature: 90-95, time: 12-72 hours, which can be determined according to the scale thickness. Rinsing and cleaning: after cleaning, drain the residual liquid in the system and add clean water to rinse twice until the coke remover is free of foam and the water is clear. vertical Fully automatic steam generator factory Temperature: 85-95, time: 5-8 hours Water blowing steps: after cleaning, connect the air compressor at the pressure gauge or other places that can be connected, use compressed air to boost the system to 0.3-0.4 MPa, and vent at each low point. Repeat this process until the water is blown out. Waste liquid treatment: the cleaning waste liquid generated in the cleaning process is discharged after being treated in the biochemical tank.