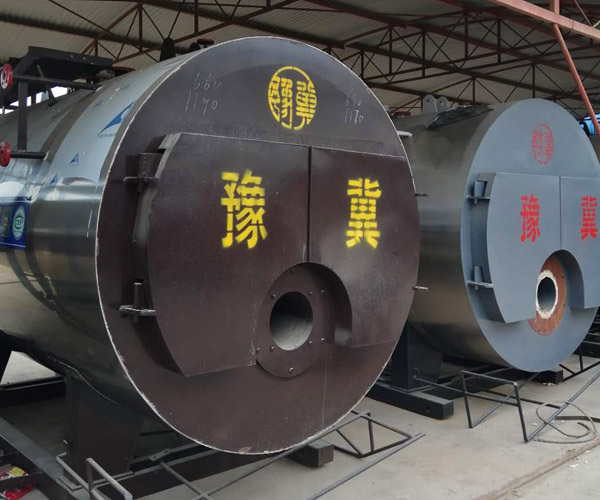
Energy saving. The waste heat boiler adopts new heat exchange fins and heat exchange elements, which enables full heat exchange. The boiler efficiency can be increased by 6~15%, and the condensate drainage structure can fully recover the latent heat in the flue gas. The energy-saving effect is remarkable. Anhui Energy saving steam generator Due to the special structure, the total pressure drop is small and the power consumption is small, that is, the smoke pressure drop is small and meets the system requirements. beautiful. Due to the use of efficient heat exchange elements and reasonable structural configuration, the waste heat boiler has the characteristics of compact structure, small size, beautiful appearance, etc. Durable. Heat exchange tubes of waste heat boiler facilities are made of stainless steel aluminum fins for corrosion prevention. small-scale Energy saving steam generator factory The thermal stress, anti-corrosion performance and strength are fully considered when the equipment is manufactured, which can ensure the safety, reliability and stability of the equipment, with a service life of more than 25 years.
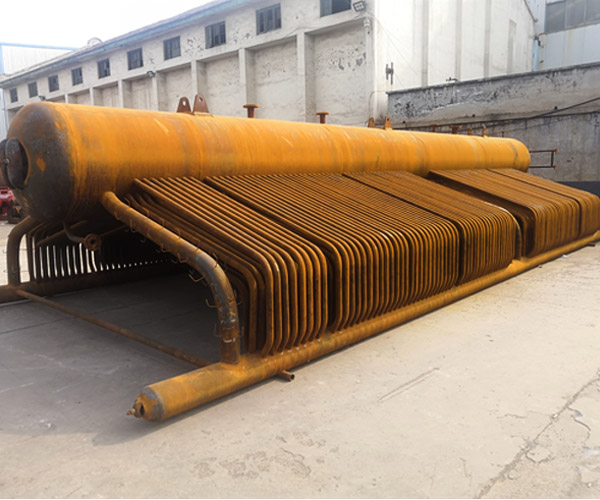
The produced waste heat boiler for hazardous waste incineration is a natural circulation water tube boiler, which adopts a single drum vertical layout and a full membrane water wall structure. Anhui Energy saving steam generator The surrounding, top and three middle membrane water-cooled walls form a tight series of heat exchange flues. The convection heating surface is no longer arranged inside the heat exchange flue, and radiation heat exchange is adopted, so as to ensure the smooth flow of high-temperature flue gas containing strong coking adhesive ash in the heat exchange flue. Full automatic shock soot blower is arranged on the membrane water wall, and inspection holes and observation holes are reserved. small-scale Energy saving steam generator factory The bottom of the boiler is composed of membrane water walls on both sides to form a water-cooled ash bucket, and the lower part is connected with a closed spiral ash extractor. The settled soot in the waste heat boiler and the ash removed by the soot blower are discharged out of the boiler by the ash extractor. The furnace wall is of pipe laying structure, and the outside is covered with corrugated steel plate.
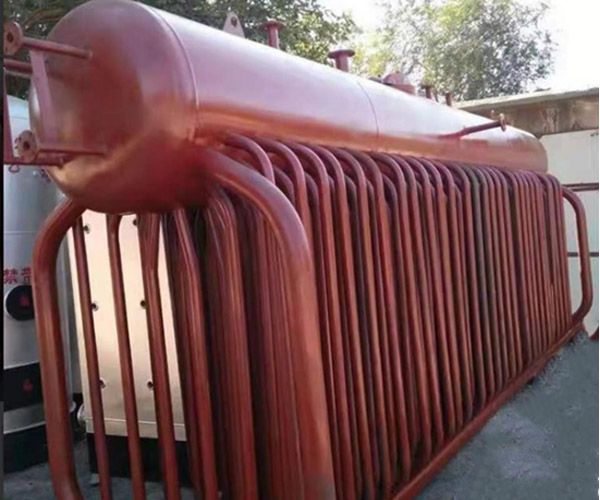
The boiler adopts the combustion equipment suitable for the combustion of biomass fuel - reciprocating grate. In the structural design of the boiler, the furnace space of the boiler is larger than that of the traditional boiler, and the reasonable arrangement of the secondary air is conducive to the full combustion of a large amount of volatile matter released instantaneously during the combustion of biomass fuel. The boiler can be equipped with oil (gas) ignition burner to realize ignition automation. Anhui Energy saving steam generator The feeding, combustion, slag removal, water supply and ignition of the boiler can be automatically controlled, and the operation is convenient. The boiler is equipped with an automatic ash cleaning device, which can remove the ash on the heating surface of the boiler in time to ensure the efficient and stable operation of the boiler. The tail of the boiler is equipped with an economizer, or an air preheater according to the user's needs. Compared with the traditional boiler, the boiler has higher efficiency and lower exhaust gas temperature. High efficiency thermal insulation materials are used, the boiler surface temperature is low, and the heat dissipation loss can be ignored. small-scale Energy saving steam generator factory All pressure parts are made of excellent boiler steel in strict accordance with Chinese national codes and standards. Each boiler shall be strictly inspected and tested before leaving the factory, including hydrostatic test and X-ray inspection. Manholes, inspection doors, fire observation holes, etc. are set to facilitate maintenance. The major characteristics of biomass boiler are: energy conservation, environmental protection, and easy installation and use.
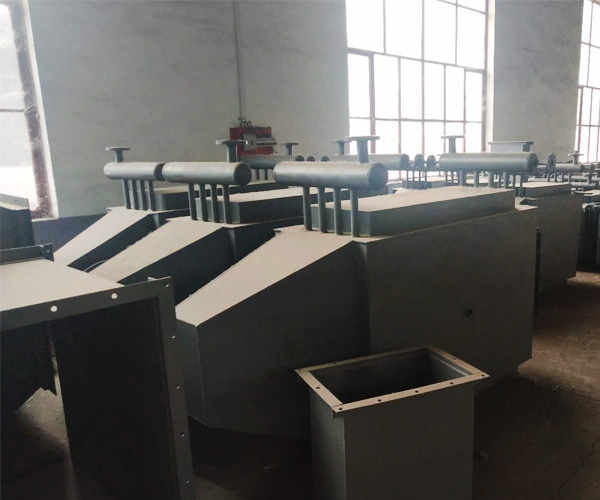
The waste heat boiler greatly improves the utilization rate of heat released by fuel combustion, so this kind of boiler saves energy; Fuel oil, gas and coal combustion generate high-temperature flue gas to release heat. The high-temperature flue gas first enters the furnace, then enters the waste heat recovery device of the front smoke box, then enters the pyrotechnic tube, and then enters the waste heat recovery device in the flue of the rear smoke box. The high-temperature flue gas turns into low-temperature flue gas and is discharged into the atmosphere through the chimney. Anhui Energy saving steam generator Conditions conducive to quick startup of waste heat boiler: (1) The waste heat boiler adopts forced circulation, which has the priority of quick startup. (2) The flue gas baffle is hydraulically controlled, which can be used to adjust the sky in principle. The flue gas flow into the boiler is reduced. (3) The adjustable guide vane at the inlet of gas turbine can not only adjust the flue gas flow of gas turbine, but also increase or decrease the exhaust gas temperature of gas turbine through the selection of IGV temperature control mode. (4) The steam turbine bypass is designed for the rated evaporation capacity of the boiler. (5) The welded bends and headers of each heating module of the boiler are in the boiler. (6) Similar boilers in other gas turbine power plants can not be reduced when starting, and can be used to adjust the main steam pressure of the boiler. Outside the wall, contact with high-temperature smoke is avoided. small-scale Energy saving steam generator factory Operating experience of gas turbine load, such as simultaneous startup of gas turbine and waste heat boiler (flue gas damper fully open). Under the possibility of quick startup of waste heat boiler, the water level of steam drum and deaerator will lose control after the flue gas baffle is opened.
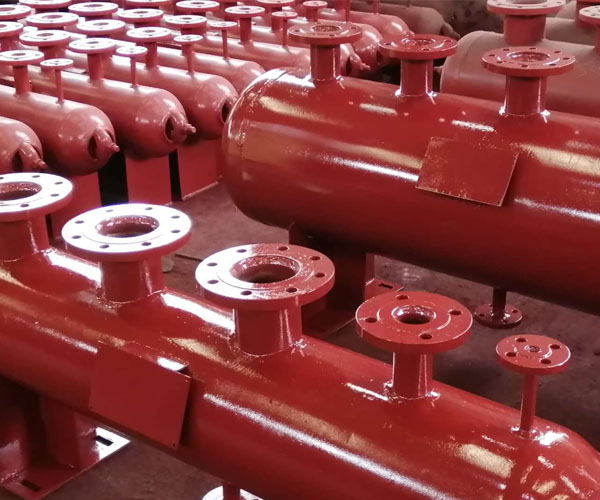
Most people may already know something about flue gas waste heat recovery, because they have already explained a lot about it. In order to let you know the relevant knowledge of flue gas waste heat recovery, the following is a brief introduction to the two methods commonly used for recovery. Anhui Energy saving steam generator Two methods are usually adopted for flue gas waste heat recovery: one is to preheat the workpiece; The other is to preheat air for combustion support. The flue gas preheating workpiece needs to occupy a large volume for heat exchange, which is often limited by the operation site (this method cannot be used for furnaces that are used intermittently). small-scale Energy saving steam generator factory Preheating air for combustion support is a good method. It is generally configured on the heating furnace, which can also strengthen combustion, speed up the temperature rise of the furnace, and improve the thermal performance of the furnace. This can not only meet the requirements of the process, but also achieve significant comprehensive energy-saving effect.