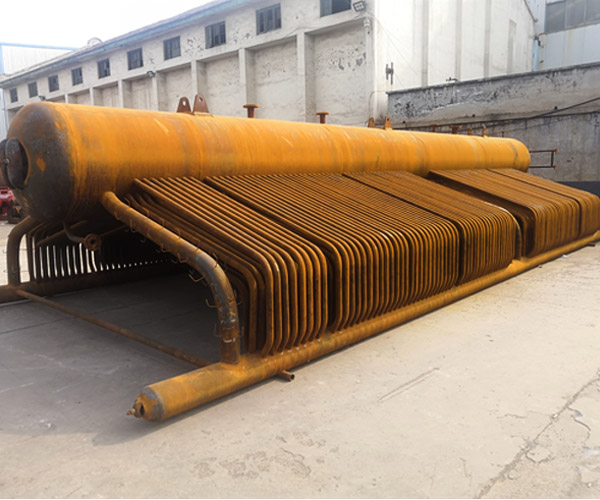
As is known to all, the boiler using sensible heat of various waste gases and waste heat after waste incineration as heat source is called waste heat boiler, also called waste heat boiler. Therefore, the country advocates vigorously developing waste heat utilization, energy conservation and emission reduction, which plays a positive role in protecting energy and improving the quality of human living environment. Shenyang Electric steam generator In the design of waste heat boiler, how to reasonably divide the temperature range is the basis for reasonably arranging the heating surface of waste heat boiler and making maximum use of waste heat. Under the condition of a given exhaust gas temperature at the inlet of the waste heat boiler, there are two requirements for the exhaust gas temperature. One is to limit the exhaust gas temperature, which is required to be within a reasonable range; The other is that the exhaust gas temperature is not limited, requiring greater use of waste heat. small-scale Electric steam generator how much In either case, for medium and low temperature waste heat utilization, the narrow point temperature difference directly affects the evaporation capacity of the waste heat boiler and the layout of the heating surface. Narrow point temperature difference, also known as node temperature difference, is a small temperature difference between evaporator outlet flue gas and heated saturated water vapor during heat exchange. With the change of narrow point temperature difference, the relative total heat exchange area, relative evaporation capacity and relative exhaust gas temperature of the waste heat boiler also change.
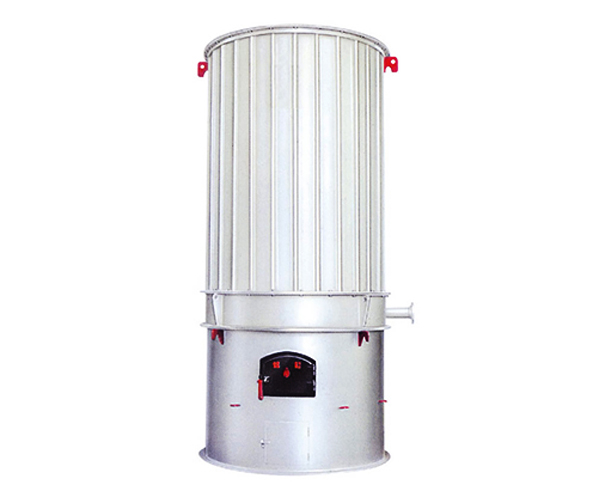
Energy saving. The waste heat boiler adopts new heat exchange fins and heat exchange elements, which enables full heat exchange. The boiler efficiency can be increased by 6~15%, and the condensate drainage structure can fully recover the latent heat in the flue gas. The energy-saving effect is remarkable. Shenyang Electric steam generator Due to the special structure, the total pressure drop is small and the power consumption is small, that is, the smoke pressure drop is small and meets the system requirements. beautiful. Due to the use of efficient heat exchange elements and reasonable structural configuration, the waste heat boiler has the characteristics of compact structure, small size, beautiful appearance, etc. Durable. Heat exchange tubes of waste heat boiler facilities are made of stainless steel aluminum fins for corrosion prevention. small-scale Electric steam generator how much The thermal stress, anti-corrosion performance and strength are fully considered when the equipment is manufactured, which can ensure the safety, reliability and stability of the equipment, with a service life of more than 25 years.
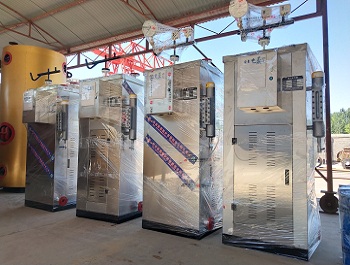
When the boiler is shut down, the temperature of the heat transfer oil can be reduced to below 70 ℃ before the hot oil pump is shut down. In case of sudden power failure, extinguish the fire immediately, and then implement the operating procedures. Otherwise, the furnace tube will be burned out and the loss will be large. According to the type of heat transfer oil boiler, heat transfer oil shall be reasonably selected to prevent overheating. Shenyang Electric steam generator When purchasing unqualified heat transfer oil, do not save money or mix heat transfer oil indiscriminately. Otherwise, the consequences will be very serious. Prevent the oxidation of heat transfer oil. The strict heat transfer oil is more than 50 degrees in contact with the air, which will make the heat transfer oil crack. Its speed is amazing, and the consequences are relatively serious. After normal operation, the test crew needs to close the exhaust valve on the auxiliary exhaust pipe. After 6 months of use, the heat transfer oil must be sampled and tested according to the instructions. If problems are found, the heat transfer oil must be replaced immediately. small-scale Electric steam generator how much However, it should be noted that different types of heat transfer oil should not be mixed. The circulation speed of the heat transfer oil should not be less than 1.5m/s. Due to the excessive temperature difference between some entrances and exits, the original design requirements were destroyed, the heat transfer oil could not maintain the original circulation state, the boundary layer became thicker, and the thermal resistance became larger, making the furnace wall exceed the oil film temperature, leading to carbon deposition, cracking, polymerization, coking, and even burning through the furnace tube.
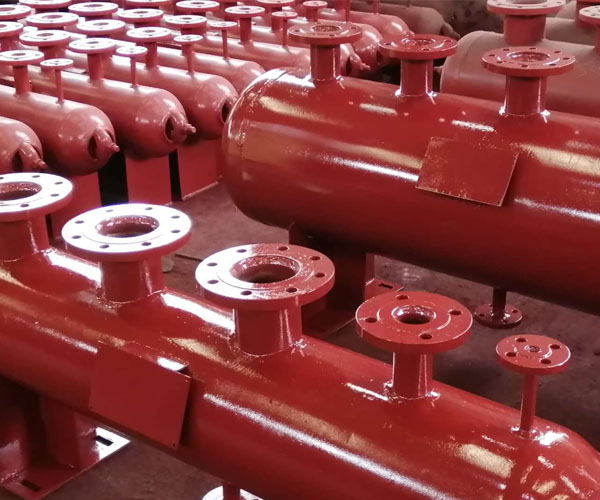
System oil drainage: circulate the heat transfer oil between 120 ± 5 to drain the heat transfer oil in the system (if you do not replace the oil, please find a clean container to store it properly). Prepare an appropriate amount of coke removal cleaning agent for the heat transfer oil system, drain the oil in the gas-fired heat transfer oil boiler system, and disconnect the cleaning system from the oil storage tank (close the valve), including the connection between the high-level tank and the oil storage tank. Shenyang Electric steam generator Residual oil blowing steps: connect the air compressor at the pressure gauge or other places that can be connected, boost the system to 0.3-0.4MPa, and discharge it instantaneously; Repeat this process until the residual oil is blown out. The gas-fired heat transfer oil boiler, circulating pump, and other heat users form a cleaning circulating circuit for decoking and cleaning: add diluted cleaning agent to the system and fill it up to 1/2 of the water level of the high-level tank. Dosage of coke removal cleaning agent: 10~20%, the specific dosage shall be determined according to the scale thickness. Temperature: 90-95, time: 12-72 hours, which can be determined according to the scale thickness. Rinsing and cleaning: after cleaning, drain the residual liquid in the system and add clean water to rinse twice until the coke remover is free of foam and the water is clear. small-scale Electric steam generator how much Temperature: 85-95, time: 5-8 hours Water blowing steps: after cleaning, connect the air compressor at the pressure gauge or other places that can be connected, use compressed air to boost the system to 0.3-0.4 MPa, and vent at each low point. Repeat this process until the water is blown out. Waste liquid treatment: the cleaning waste liquid generated in the cleaning process is discharged after being treated in the biochemical tank.