The commonly used waste heat boiler adopts smoke tube heat exchange, and the wall temperature of its metal heating surface is roughly in a multiple relationship with the discharge temperature of hot fluid. As for the smoke pipe heat exchanger, if the wall temperature of the metal heating surface is required to be no less than 150 ℃, the exhaust gas temperature shall generally be no less than 300 ℃, otherwise it will inevitably cause low-temperature dew corrosion.
Considering the low temperature condition of equipment operation, the safety factor is 1.5 times, Waste heat boiler The exhaust gas temperature of steam drum and waste heat boiler is not lower than 450 ℃. At this time, the waste heat boiler can recover about 0.5 tons of heat. The recovery efficiency of low-temperature waste heat boiler is still very low. In addition, the temperature is only the check temperature at this time. When the adjustment must be stopped due to the operation demand under the operation condition, there is no way to directly stop the adjustment and control of the wall temperature.
When the metal wall temperature of the heating surface at the tail of the waste heat boiler is lower than the condensation point of sulfuric acid steam, liquid sulfuric acid will be formed on its surface. For a long time, the corrosion caused by condensation on the tail heating surface of each heat exchange equipment often occurs. As a result, during the design of the waste heat boiler, it is necessary to improve the exhaust gas temperature or use non-metallic data with poor heat transfer to alleviate the generation of condensation and corrosion, but the problem is still not basically solved. However, the waste heat recovery equipment often shows corrosion after one to two years of operation until perforation.
Low temperature waste heat Boiler factory The operation method is as follows: fill 1514 liters of hot water first, and maintain the water temperature at 93 ℃. Use a container to put 2270 liters of hot water, dissolve trisodium phosphate and wetting agent, isolate the connection between the water supply and steam pipes and the external system, and isolate the elements that do not need to be boiled. Then connect the water supply and steam systems with the boiling solution system. Start the solution pump and inject the boiling solution into the boiler. In order to keep the temperature of boiling solution within the range of 138 ℃~150 ℃, steam should be supplied to boiling solution from other steam sources. Steam can be supplied from the regular blowdown pipe at the lower part of the steam drum. Turn on the solution pump every half an hour for 5 minutes to ensure uniform solution distribution. After boiling out, drain the solution and flush it with hot water. Check the PH value of the water at the drain to see if the flushing is qualified. After inspection, if there is still oil or grease inside, the steam waste heat boiler will repeat the plain furnace until there is no oil.
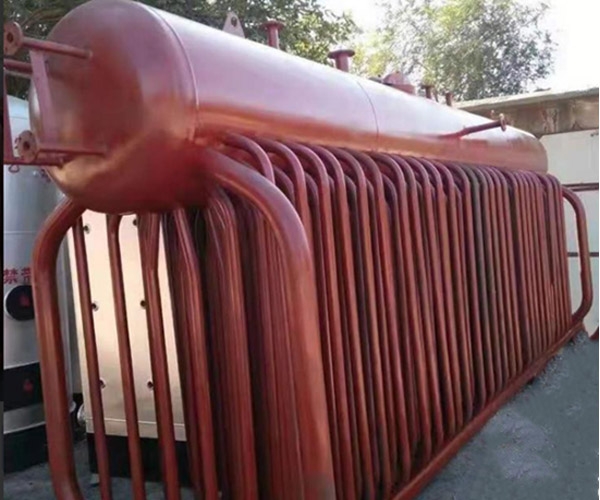