Manufacturer of flue gas waste heat recovery device It means that the use efficiency of oil, gas and coal-fired boilers is about 70%, and flue gas heat accounts for the majority of wasted heat. This part of heat can be recovered by the flue gas waste heat recovery device, which can increase the boiler water inlet temperature, air blast inlet temperature or directly generate steam for production and domestic use. The transformation of the boiler is simple. The flue gas waste heat recovery device can be installed and replaced in the flue of the first section of the boiler. It can be installed arbitrarily without changing the original equipment status. At the same time, full automatic control can be added to realize unattended. It has the advantages of safety, environmental protection, energy conservation and consumption reduction.
The utilization efficiency of waste heat recovery of industrial oil, gas and coal-fired boilers is about 70%, and flue gas heat accounts for the majority of wasted heat. Generally, the exhaust gas temperature at the tail of steam and hot water boilers is more than 280~350 ℃. The boiler economizer can recover this part of heat to increase the boiler water inlet temperature, air blast temperature or directly generate steam production and domestic gas.
The hotel boiler waste heat recovery heat exchanger uses the waste heat gas discharged from the boiler flue to produce hot water or heating gas, which is heated simultaneously during the boiler heating process. The hot water and hot gas produced can be directly or auxiliary used. The transformation of the boiler is simple. The gas gas or gas water heat exchanger produced by us can be installed and replaced in the primary boiler flue. It has the characteristics of not affecting the boiler ignition, combustion, consumption, no need to shut down, safety, environmental protection, energy conservation, etc., and the return on investment period is 12-18 months.
The kitchen flue gas waste heat recovery heat exchanger is directly installed in the rear flue of the traditional boiler range, Manufacturer of flue gas waste heat recovery device Using the heat energy carried by the boiler exhaust gas temperature of about 500-600 degrees, the produced hot water is sent to the storage tank for standby. The hot water stored in the tank can be used by the kitchen itself or other occasions. The kitchen flue gas heat exchanger can effectively reduce the exhaust gas temperature and reduce the potential fire hazard. It can automatically start up and operate with the stove and the stove, without manual operation, and the heat efficiency of the stove can be increased by more than 30%.
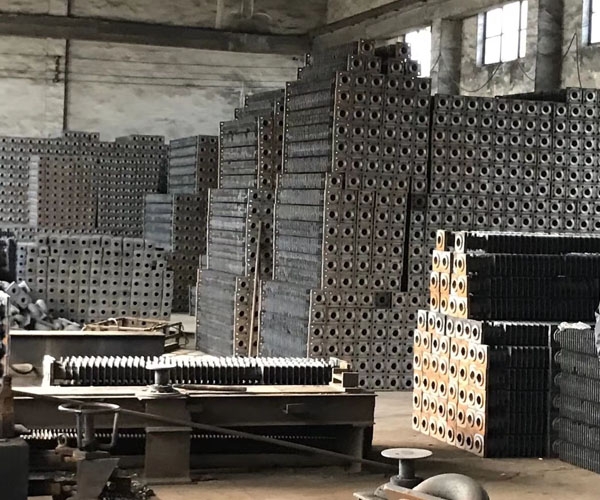