With the development of iron and steel industry, the proportion of hot metal produced by electric furnace steelmaking is gradually rising, some even more than 30%. The increase of hot metal proportion has caused the increase of flue gas volume, heat waste and dust removal problems in electric furnace steelmaking. How to fully recover the sensible heat in this part of high-temperature flue gas, turn "waste" into treasure, convert it into heat energy, and make the flue gas of electric furnace more stable, create conditions for efficient dust removal, so as to reduce the operating cost of the dust removal system and the production cost of enterprises, this is a problem that electric furnace steelmaking enterprises must pay attention to.
Flue gas waste heat boiler For the device, the vaporization cooling system with high and low pressure, natural and forced combined circulation has successfully recovered the residual heat of the flue gas at the fourth hole outlet of the electric furnace, which is about 2100~80 ℃. At the same time, the flue gas temperature has been reduced. After mixing with the closed cover of the electric furnace and the roof dust cover, the flue gas temperature has reached the ideal dust removal temperature of about 250 ℃.
In order to prevent insufficient flue gas process, the pipeline is equipped with a steam heating device to prevent the temperature drop caused by heat loss in the process of hot water circulation, and also to prevent the situation that the heat provided by the flue gas is too small to meet the requirements of users in the whole plant. As the hot water will cause floor drain, a desalted water supplement device is set to automatically supplement the desalted water according to the water level in the storage tank. Since there is pressure in the superheated water production device, it is necessary to set the pressure control unit to control the system pressure.
During the whole smelting cycle, Flue gas waste heat boiler The quantity and composition of furnace gas vary greatly. If the excess air coefficient is adopted, the flue gas volume will also fluctuate greatly. Therefore, it is recommended to adjust the opening of the water cooling sliding sleeve according to the flue gas composition at the outlet of the combustion settling chamber.
The use of waste heat boiler to recover waste heat has good effect, stable operation, high efficiency and high heat recovery rate. Its final product (steam) is easy to achieve production scheduling balance in the whole plant area. When the steam consumption of the production line is lower than the system output, the surplus steam will be added to the workshop steam pipe network, so there is no problem of insufficient heat recovery caused by high capacity. The production capacity of waste heat boiler decreases with the reduction of annealing furnace processing capacity. With the waste heat boiler recovery system, the heat recovery rate can reach 14%.
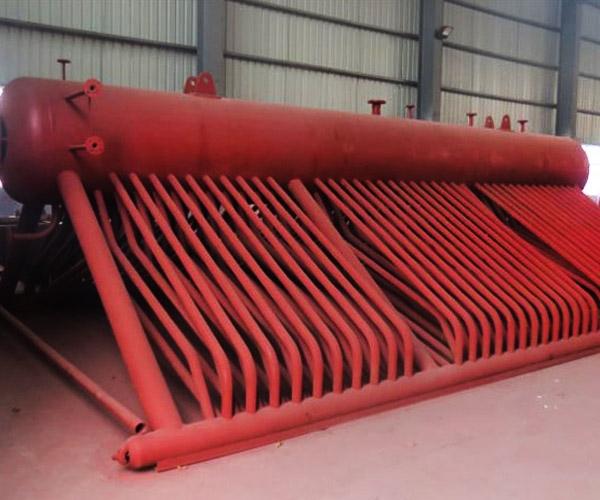